KADANT PTX 9750 Repair Instructions
![]() ![]() |
![]()
Repair Instructions for the 9750 PTX® Rotary Jointfluidhandling.kadant.com/en/knowledge-center/installation-and-repair-instructions/piston-type-pt-ptx-pt2x-rotary-joints/repair-instructions-for-the-9750-ptx-rotary-jointEffective: December 1, 2021IntroductionRead all of the instructions before proceeding.Refer to Kadant Johnson assembly drawing for part identification and to drawing A37640 for torque specifications.For easy identification, parts used in individual steps are often accompanied with their position in the assemblydrawing [e.g. gasket (8B)]. Tighten all fasteners in a star pattern. Certified drawings are available upon request.Dimensions are for reference only and subject to change.SafetyThis safety symbol alerts you to risk of death or injury if the instructions are not followed. In all steps, death or injury may result if the machine is not de-energized, depressurized, cooled, and stopped. Death or injury may occur if the product is operated with a fluid type or at a pressure, temperature, or speedthat do not meet its specifications. Death or injury may occur if heavy parts and pinch hazards are not handled properly. Follow your company’s safetyprocedures.ToolsStep 1 - RemovalDisconnect piping. Remove the head and set aside.Equipment must be cool and free of pressure.Step 2Bend tabs back from hollow bolt.Tools Per Crew(2) 9/16" Combination Wrenches(2) 3/4" Combination Wrenches13/16" Combination Wrench13/16" Shallow Socket15/16" Combination Wrench15/16" Shallow Socket1/4" Hex Head Socket5/16" Hex Head Socket3/8" Hex Head Socket1/2" Hex Head Socket(2) 6 1/2" Drive Extension0 to 150 lbs Torque Wrench1/2 to 3/8" Square Drive Reducer3 lbs HammerGasket ScraperEndcap Assembly Repair6 mm Hex Head Socket with extension5 mm Hex Head SocketO-ring PickTo Pass Between Crews300 lbs Torque Wrench2 1/2" Socket and Adapters for Torque WrenchStep 3Unthread the hollow bolt approximately 1/4" (6.4 mm). Place a block of wood over the hollow bolt and strike it witha hammer. This will break the tapered seal inside of the rotary joint. Remove the hollow bolt and set aside for reuse.Step 4Remove the body and set aside with O-ring side up. Remove and discard the O-ring (26).Step 5Remove the end cap assembly and seal ring. Place the end cap assembly with the seal ring surface facing up. Ifworking on the dryer bearing, move the support tube into the journal.Spring force present during end cap assembly installation.Step 6Remove the ring bracket and wear plate.Tip: If dryer bearing work is needed, remove the journal flange (if necessary) and bearing cover to access thebearing. Reinstall after bearing work is complete.Note: There are two types of repair kits. If using the preassembled end cap assembly kit, proceed to step 12.Step 7 - End Cap Asembly RepairPlace the assembly in a press with the seal ring surface facing up. Compress the nipple and remove the cap screws.Release the press and separate the nipple from the end cap.Step 8Remove the O-rings and discard. Inspect the nipple groove(s) and sealing surfaces. Replace if damaged. Install andlubricate new O-rings. |
Related manuals for KADANT PTX 9750
This manual is suitable for:
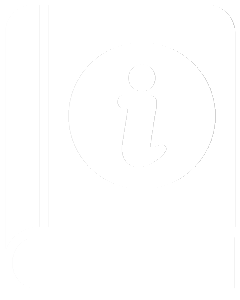
manualsdatabase
Your AI-powered manual search engine