ABB ACS355 Quick Installation And Start-up Manual
Also see for ACS355 series: Quick start up guideQuick start guideInstallation instructionsInstallation instructionsApplication guide
![]() ![]() |
![]()
Safety instructionsWARNING! Obey these instructions. If you ignore them, injury or death,or damage to the equipment can occur. If you are not a qualifiedelectrical professional, do not do electrical installation or maintenancework.• Keep the drive in its package until you install it. After unpacking, protect thedrive from dust, debris and moisture.• Use the required personal protective equipment: safety shoes with metal toecap, safety glasses, protective gloves and long sleeves, etc.• When the drive or connected equipment is energized, do not do work on thedrive, motor cable, motor, control cables or control circuits.• Do not do work on the drive when a rotating permanent magnet motor isconnected to it. A rotating permanent magnet motor energizes the drive,including its input and output power terminals. Electrical safety precautions1. Clearly identify the work location and equipment.2. Disconnect all possible voltage sources. Make sure that re-connection is notpossible. Lock out and tag out.• Open the main disconnecting device of the drive.• If you have a permanent magnet motor connected to the drive,disconnect the motor from the drive.• Disconnect any dangerous external voltages from the control circuits.• After you disconnect power from the drive, always wait 5 minutes to letthe intermediate circuit capacitors discharge before you continue.3. Protect any other energized parts in the work location against contact.4. Take special precautions when close to bare conductors.5. Measure that the installation is de-energized.• Use a multimeter with a minimum impedance of 1 Mohm.• Make sure that the voltage between the drive input power terminals (U1,V1, W1) and the ground (PE) is close to 0 V.• Make sure that the voltage between the drive output terminals (U2, V2,W2) and the ground (PE) is close to 0 V.• Make sure that the voltage between the drive DC terminals (BRK+ andBRK-) and the ground (PE) is close to 0 V.6. Install temporary grounding as required by the local regulations.7. Ask the person in control of the electrical installation work for a permit towork.See the drive user’s manual for the complete safety instructions.1. Examine the installation areaThe drive is intended for cabinet installation and has a degree of protection ofIP20 / UL open type as standard.Make sure that in the installation area:• There is sufficient space above and below the drive for cooling, and hot airdoes not recirculate. Refer toFree space requirements.• The ambient conditions are suitable. Refer toAmbient conditions.• The mounting surface is non-flammable and can hold the weight of the drive.Refer toDimensions and weights.• Materials near the drive are non-flammable.• There are no sources of strong magnetic fields, such as high-current single-core conductors or contactor coils near the drive. A strong magnetic fieldcan cause interference in the operation of the drive.2. Install the driveYou can install the drive with screws or to a DIN rail [Top Hat, W x H = 35 ×7.5 mm (1.4 × 0.3 in)].• Make sure that there is a minimum of 75 mm (3 in) of free space above andbelow the drive for cooling air.• When placing drives on top of each other in a panel or cabinet, make surethat the hot air from the drives below do not directly enter the drive above.WARNING! Do not install the drive upside down. Make sure that thecooling air exhaust (at the top) is above the cooling air inlet (at thebottom). To install the drive with screws1. Cut out the mountingtemplate from thepackage and use it tomark the locations forthe mounting holes.2. Make the holes for themounting screws andinstall suitable plugs oranchors.—ABB MACHINERY DRIVESACS355 drivesQuick installation and start-up guide3. Start to tighten thescrews into themounting holes.4. Place the drive ontothe mounting screws.5. Tighten the mountingscrews securely. To install thedrive to a DINrail1. Place the top of thedrive onto the DINinstallation rail in anangle as shown infigure.2. Set the drive againstthe wall.3. To remove the drive,press the release leveron top of the drive.3. Attach the clamping plates1. Fasten the clampingplate to the plate atthe bottom of the drivewith the providedscrews.2. Frame sizes R0…R2:Fasten the I/Oclamping plate to theclamping plate withthe provided screws.4. Measure the insulation resistanceMeasuring the insulation is typically not required in North America.Drive: Do not do voltage tolerance or insulation resistance tests on the drive,because this can cause damage to the drive.Input power cable: Before you connect the input power cable, measure theinsulation of the input power cable. Obey the local regulations.Motor and motor cable:1. Make sure that the motor cable is connected to the motor and disconnectedfrom the drive output terminals U2, V2 and W2.2. Use a voltage of 1000 V DC to measure theinsulation resistance between each phaseconductor and the protective earth conductor.The insulation resistance of an ABB motor mustbe more than 100 Mohm (at 25 °C/77 °F). For theinsulation resistance of other motors, refer tothe manufacturer’s documentation. Moisture inthe motor decreases the insulation resistance.If you think that there is moisture in the motor,dry the motor and do the measurement again.5. Select the cablesInput power cable: IEC/EN 61800-5-1 requires two protective earth (ground)conductors. Prefer a symmetrical shielded cable (VFD cable).Motor cable: Use a symmetrical shielded cable (VFD cable) for the best EMCperformance and to meet the European EMC requirements.Control cable: Use a double-shielded twisted-pair cable for analog signals. Use adouble- or single-shielded cable for digital, relay and I/O signals. Do not mix 24 Vand 115/230 V signals in the same cable.6. Connect the power cables Connection diagram (shielded cables) Connection procedure (shielded cables)WARNING! Make sure that the drive is compatible with the earthingsystem. You can connect all drive types to a symmetrically groundedTN-S system. For other systems, see the drive user’s manual.1. Strip the inputpower cable. Groundthe cable shield (ifany) under thegrounding clamp.Twist the cableshield into a bundle,mark it accordinglyand connect it to thegrounding terminal.Connect othergroundingconductors (PE) to the grounding terminal. Connect the phase conductors tothe U1, V1 and W1 terminals.2. Strip the motor cable. Ground the cable shieldunder the grounding clamp. Twist the motorcable shield into a bundle, mark it accordinglyand connect it to the grounding terminal.Connect the phase conductors to the U2, V2 andW2 terminals.3. If applicable, connect the brake resistor cable tothe BRK+ and BRK- terminals. Use a shieldedcable and ground the shield under thegrounding clamp.4. Mechanically attach the cables on the outside ofthe drive.1 360-degree grounding of the cable shield. Required for the motor cable and brakeresistor cable, recommended for the input power cable.2 Use a separate grounding cable if the conductivity of the cable shield is not sufficient(smaller than the conductivity of the phase conductor) for the protective grounding, orthere is no symmetrically constructed grounding conductor in the cable.3 In one-phase installations, connect phase to U1/L, neutral to V1/N and leave W1disconnected.4 Use two grounding conductors if the cross-section of a single grounding conductor isless than 10 mm2 Cu or 16 mm2 AI (IEC/EN 61800-5-1). For example, use the cable shieldin addition to the fourth conductor.5 Use a separate grounding cable (line side) if the conductivity of the fourth conductor orshield is not sufficient for the protective grounding.R0…R21000 V DC 100 M hM3~U1V1W1 PEohmU2 V2 W21)DriveU1/ L V1/N W1Motor3 ~V1U1 W1PEPE L1/L L2/N L3/-2)BRK+ BRK-Optional brakeresistor orcommon DC3)5)1)4)7. Connect the control cables Default I/O connectionsThe diagram shows the I/O connections when parameter9902 has value 1(ABB STANDARD). Connection procedureTo prevent inductive coupling, keep thesignal wire pairs twisted all the way upto the terminals.1. Remove the terminal cover.2. Strip the outer insulation of thecable and ground the bare shield360 degrees under the clamp.3. Connect the conductors to thecorrect control terminals. Torquethe terminals to 0.4 N·m (3.5 lbf·in).4. For double-shielded cables, twistalso the grounding conductors ofeach pair in the cable together andconnect the bundle to the SCRterminal (terminal 1).5. Mechanically attach the controlcables on the outside of the drive.6. If you are going to use an optionalSafe Torque Off function, connectSTO conductors to the correctterminals. Use a tightening torqueof 0.4 N·m (3.5 lbf·in).7. Unless you need to install theoptional fieldbus module, slide theterminal cover back into place.8. Install the fieldbusmodule (optional)See the drive user’s manual.9. Install the control panel (if any)10. Start up the driveWARNING! Before you start up the drive, make sure that the installationis complete. Make sure that the cover of the drive is in place. Make surealso that the motor does not cause danger when it starts. Disconnectthe motor from other machinery, if there is a risk of damage or injury.There is an extensive installation checklist in the drive user’s manual. Start up without a control panel1. Apply input power and wait for a moment.2. Check that the red LED is not lit and the greed LED is lit but not blinking.The drive is now ready for use. Start up with a control panel (manual start-up)You can use the basic control panel or the assistant control panel. Theinstructions below are valid for both control panels, but the displays shown arethe basic control panel displays, unless the instruction applies to the assistantcontrol panel only.Before you start, ensure that you have the motor nameplate data at hand.Frame size Tightening torquesU1, V1, W1, U2, V2, W2,BRK+ and BRK-PER0…R2 0.8 N·m (7 lbf·in) 1.2 N·m (11 lbf·in)R3 1.7 N·m (15 lbf·in) 1.2 N·m (11 lbf·in)R4 2.5 N·m (22 lbf·in) 1.2 N·m (11 lbf·in)00353783 LPOWER-UPApply input power.The basic control panel powers up into theOutput mode.The assistant control panel asks if you want torun the Start-up assistant. If you press , theStart-up assistant is not run, and you cancontinue with manual start-up in a similarmanner as described below for the basic controlpanel.X1A1 SCR Signal cable shield (screen)2 AI1 Output frequency reference: 0…10 V 1)3 GND Analog input circuit common4 +10V Reference voltage: +10 V DC, max. 10 mA5 AI2 Not in use by default. 0…10 V6 GND Analog input circuit common7 AO Output frequency value: 0…20 mA8 GND Analog output circuit common9 +24V Auxiliary voltage output: +24 V DC, max. 200 mA10 GND Auxiliary voltage output common11 DCOM Digital input common12 DI1 Stop (0) / Start (1)13 DI2 Forward (0) / Reverse (1)14 DI3 Constant speed selection 2)15 DI4 Constant speed selection 2)16 DI5 Acceleration and deceleration selection 3)X1B17 ROCOM Relay output 1No fault [Fault (-1)]18 RONC19 RONO20 DOSRC Digital output, max. 100 mANo fault [Fault (-1)]21 DOOUT22 DOGNDX1C:STO1 OUT1 STO (Safe torque off) connection2 OUT23 IN14 IN2max.500 ohm1…10 kohm4)1) AI1 is used as a speed reference if vectormode is selected.2) See parameter group12 CONSTANTSPEEDS:3) 0 = ramp times according to parameters2202 and2203. 1 = ramp times according toparameters2205 and2206.4) 360 degree grounding under a clamp.Tightening torque: 0.4 N·m / 3.5 lbf·in.DI3 DI4 Operation (par.)0 0 Set speed through AI11 0 Speed 1 (1202)0 1 Speed 2 (1203)1 1 Speed 3 (1204)00.REM HzOUTPUT FWDEXITDo you want touse the start-upassistant?YesNoEXIT OK00:00REM CHOICE |
Related manuals for ABB ACS355 series

ABB ACS355 Quick Installation And Start-up Manual

ABB ACS380 Quick Installation And Start-up Manual

ABB ACS380 Quick Installation And Start-up Manual

ABB ACS560 Quick Installation And Start-up Manual

ABB ACS560 Quick Installation And Start-up Manual

ABB ACS480 Quick Installation And Start-up Manual

ABB ACS560 Quick Installation And Start-up Manual

ABB ACS180 Quick Installation And Start-up Manual

ABB ACS560 Quick Installation And Start-up Manual

ABB ACS480 Quick Installation And Start-up Manual
This manual is suitable for:
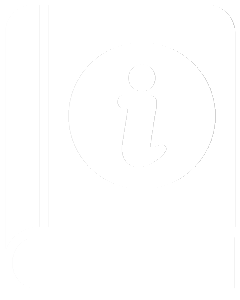
manualsdatabase
Your AI-powered manual search engine