
Eaton PBI Technical Manual
![]()
3Call point pBi/BGi & pBW/BGW February 2024 www.eaton.comCall point PBI/BGI & PBW/BGWEnglishconfiguration until the glass has been broken and theswitch contacts have closed. Upon closure of the switchthe current is then sent through R1 and hence changesthe resistive value in the circuit which triggers the alarm.The R2 resistor always has a current flowing throughwhich provides the reference resistive value for thecircuit. The circuit can diagnose an open circuit failure inR1 without having to trigger the system via a continuitycheck which is a form of diagnostics for determiningif an R1 resistor has failed Open Circuit. This form ofdiagnostics does however require a proof test to beconducted in order to identify the failure and dependingon the set up of the system the defective Resistor maynot be easily traceable if there are several BGI break glassUnits in the system. The end of line resistor R2 is usedfor the purpose of detecting an open or short circuit in thesupply conductors.The safety function of the Call Point is to raise the alarmwhen the Glass is Broken.Under No fault (Normal) Operating conditions the BGBreak Glass Unit will raise the alarm upon operating theswitch via breaking the glass.Under fault conditions the failure mode of the Break Glassis a failure to raise the alarm. For the failure rate associatedwith this failure mode please refer to the table below.Assessment of functional safetyThe BG Call Point is intended for use in a safety systemconforming to the requirements of IEC61508. Sira Test &certification Ltd has conducted a Failure Modes Effect andDiagnostic Analysis (FMEDA) of the BG Break Glass unitagainst the requirements of IEC61508-2 using a proof testinterval of 8760hrs. The Call Point is classed as a Type Adevice.BGi breakglass unitSafety Function of BG Break Glass Unit:‘To raise the alarm upon breaking the glass’Architecturalconstraints: Type AHFT=0SFF= 97%Proof Test Interval=8760HrsMTTR = 8 HrsSIL3Random hardwarefailures: λDD = 0λDU = 5.72E-07 λSD = 0λSU = 2.04E-05Probability of failureon demand: PFDAVG=2.51E-03(Low Demand Mode) SIL2Probability ofDangerous failure onsafety function:PFH = 5.72E-07(High Demand Mode) SIL2Hardware safetyintegrity compliance[1] Route 1HSystematic safetyintegrity compliance Route 1SSystematic Capability SC2Overall SIL-capabilityachieved SIL 2 (Low Demand)SIL 2 (High Demand)Conditions of safe useThe following conditions apply to the installation,operation and maintenance of the assessed equipment.Failure to observe these may compromise the safetyintegrity of the assessed equipment:1. The user shall comply with the requirements given inthe manufacturer’s user documentation (This SafetyManual and Technical manual) in regard to all relevantfunctional safety aspects such as application of use,installation, operation, maintenance, proof tests,maximum ratings, environmental conditions, repair,etc;2. Selection of this equipment for use in safety functionsand the installation, configuration, overall validation,maintenance and repair shall only be carried out bycompetent personnel, observing all the manufacturer’sconditions and recommendations in the userdocumentation.3. All information associated with any field failuresof this product should be collected under adependability management process (e.g., IEC60300-3-2) and reported to the manufacturer.4. The unit should be tested at regular intervals toidentify any malfunctions; in accordance with thissafety manual. |
Related manuals for Eaton BGI
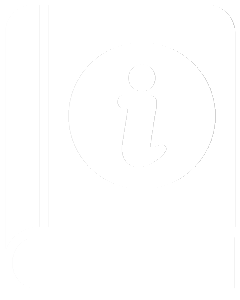
manualsdatabase
Your AI-powered manual search engine