ABB ACS800-37LC-0690-5 manuals

ACS800-37LC-0690-5
Table of contents
- Table Of Contents
- Table Of Contents
- Table Of Contents
- Table Of Contents
- Table Of Contents
- Table Of Contents
- Table Of Contents
- What this chapter contains
- Safety in installation and maintenance
- Grounding
- Permanent magnet motor drives
- General safety
- Use of the hand-operated winch
- Safe start-up and operation
- Related documents
- Terms and abbreviations
- Single-line circuit diagram of the drive
- Example circuit diagram (frame 2×R8i+2×R8i)
- Block diagram of the main circuit with options
- General information on drive cabinet layout
- Cabinet layout (frames R7i+R7i and R8i+R8i)
- Swing-out frame layout
- Auxiliary control cubicle layout
- Main switch disconnecter cubicle layout (frames 2×R8i+2×R8i and up)
- Layout of LCL filter and supply module cubicles (frame 2×R8i and up)
- Layout of inverter module cubicle (frame 2×R8i)
- Layout of inverter module cubicle (frame 3×R8i)
- Layout of inverter module cubicles (frames 4×R8i to 9×R8i)
- Overview of supply and inverter modules (R7i and R8i)
- Overview of power and control connections
- Control of the supply unit
- Emergency stop push button
- Connections and use of the I/O in the supply unit
- Connections to standard I/O terminals
- Control of the inverter unit and motor
- Type designation labels
- Type designation key
- Checking the delivery
- Moving the unit by fork-lift or pallet truck
- Placing the unit
- Overview of the installation procedure
- Fastening the cabinet to the floor and wall (non-marine units)
- Alternative 2 – Using the holes inside the cabinet
- Fastening the unit to the floor and wall (marine units, option +C121)
- Joining the shipping splits
- Connecting the liquid pipes
- Connecting the DC busbars
- Miscellaneous
- Electric welding
- Protecting the motor insulation and bearings
- Requirements for motor insulation and bearings and drive filters
- Explosion-safe (EX) motors
- High-output motors and IP 23 motors
- Sine filters
- Typical power cable sizes
- Alternative power cable types
- Additional US requirements
- Relay cable
- Separate control cable ducts
- Protecting the motor and motor cable in short-circuit situations
- Insulation requirements for the motor temperature sensor circuit
- Implementing the Prevention of unexpected start function
- Implementing the Safe torque off function
- Terminals for connecting external control voltage (option +G307)
- Implementing a safety switch between the drive and motor
- Implementing a bypass connection
- Switching the motor power supply from direct-on-line to drive
- Considering the PELV on installation sites above 2000 metres (6562 feet)
- Braking resistor assembly
- Connecting the input power cable
- Connecting the motor cable – units with no common motor terminals cubicle option +H359
- Connection diagram – parallel inverter modules feed one motor
- Connection procedure
- Connection diagram
- Connecting external power supply for the auxiliary circuits
- Frames 2×R8i and up
- tional auxiliary control voltage transformer
- Connecting the control cables for the inverter unit
- Connecting a PC
- Cabling of I/O and fieldbus modules
- Connecting voltage to the input terminals and auxiliary circuit
- On-load checks
- Switching the control panel between the supply and inverter units
- ACS800-17LC-specific parameters in the IGBT Supply Control Program
- Default values of parameters with the ACS800-17LC
- ACS800-17LC-specific parameters in the application program
- LEDs
- Replacing the additional fan in the incoming cubicle (frames R7i+R7i and R8i+R8i)
- Replacing the auxiliary control cubicle fan (frames 2×R8i+2×R8i and up)
- Replacing the fan in the incoming cubicle (frames 2×R8i+2×R8i and up)
- Replacing the cooling fans in supply module cubicle
- Replacing the inverter module fans (2×R8i and up)
- Reduced run capability
- Replacing supply and inverter modules
- Installing the winch
- Installing the installation stand
- Capacitors
- Replacing the PPCS branching unit (APBU-xx) memory backup battery
- General
- Connection to a cooling unit
- Filling up and bleeding the internal cooling circuit
- Draining the internal cooling circuit
- Specifications
- Water quality
- Materials
- Definitions
- Altitude derating
- phase brake choppers (option +D150) and resistors (option +D151)
- Fuses
- Main circuit DC fuses
- Dimensions, weights and free space requirements
- Losses, cooling data and noise
- Internal cooling circuit data
- Terminal and lead-through data for the input power cable
- Terminal and lead-through data for the motor cable
- Units with the Common Motor Terminal (CMT) cubicle (option +H359)
- Electrical power network specification
- Control unit (RDCU/RMIO) connection data
- Relay outputs
- Isolation and grounding diagram
- Ambient conditions
- Auxiliary circuit current consumption
- Applicable standards
- CE marking
- Category C2
- Category C4
- UL marking
- Cyber security disclaimer
- Frame sizes R7i+R7i and R8i+R8i (bottom entry/exit)
- Frame sizes R7i+R7i and R8i+R8i (marine units, +C121)
- Product and service inquiries
Related products
ACS800-37LC-0310-5ACS800-37LC-0520-5ACS800-37LC-0170-5ACS800-37LC-0250-5ACS800-37LC-0120-5ACS800-37LC-0410-5ACS800-37LC-0210-5ACS800-37LC-2000-5ACS800-37LC-3930-5ACS800-37LC-0390-7ABB categories
Industrial Equipment
DC Drives
Controller
Relays
Measuring Instruments
Circuit breakers
Battery Charger
Industrial Electrical
Transformer
Switch
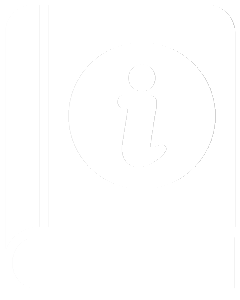
manualsdatabase
Your AI-powered manual search engine