
Carrier 30HR Product Data
Also see for 30HR Series: Wiring diagramsInstallation, Start-Up and Service InstructionsInstallation instructionsInstallation, Start-Up and Service Instructions
![]()
Additional features ensure smooth,trouble-free operation. Compres-sors are mounted on heavy-duty springvibration isolators to minimize poten-tially damaging vibration transmis-sion to the building structure. Sound-deadening mufflers dampen hot gaspulsations. Servicing is made easy bybolted, readily-accessible semi-hermeticcompressors that can be removedwith minimal field labor when adjust-ments or repairs are needed.Flotronic™ Plus control sys-tem regulates the refriger-ant cycle for optimumefficiencyThe 30HR,HS Flotronic Plus chillersfeature an electronic expansion valve(EXV) operated by a microprocessor-based control system. The systemmonitors safety functions and controlsunit capacity to maintain leavingchilled fluid temperature. The micro-processor controls loading and un-loading of compressors to matchchanging cooling load requirements.The control system consists of acontrol box with a keypad and displaymodule, an EXV for each refrigera-tion circuit, and thermistors (tempera-ture sensors) which provide analoginputs to the microprocessor. Thecontrol also operates a quick test pro-gram to check input and output sig-nals to and from the microprocessor.The 30HR,HS control system is selfcontained and can operate on astand-alone basis if desired.ComponentsThe control box — All themicroprocessor-based controls re-quired to optimize chiller operationand protect it against unsafe con-ditions are contained in the controlbox. This includes the processor mod-ule, relay module, EXV driver mod-ule, keypad and display module, relays,and transformers. The box has ahinged door for ready access.The EXV driver — The driver posi-tions the EXVs (based on commandsfrom the microprocessor) andmonitors the status of the oil andrefrigerant pressure switches.The keypad and display module— This module consists of a key-pad with 11 function keys and 12 nu-meric keys (0 to 9, . , -) and analphanumeric 8-character liquid crystaldisplay. The module allows the op-erator to perform the followingfunctions:• read and change set point• configure unit• run quick test unit checkout• observe diagnostic information• schedule chiller operationControl featuresLeaving fluid temperature controlwith return compensation —The rate at which the compressorsare turned on will depend on the dif-ference between the actual leavingfluid temperature and the set point,the rate of change of leaving fluidtemperature, the return fluid tempera-ture, and the number of compressorstages on. The control is primarilyfrom leaving fluid temperature, andthe other factors are used as compen-sation. Because the control operatesfrom leaving fluid, the chiller is in-dependent of cooling gpm (L/s). It is atrue droopless control.Return temperature reset — Thecontrol system is capable of han-dling leaving fluid temperature resetbased on return cooler temperature.Because the change in temperaturethrough the cooler is a measure of thebuilding load, the return temperaturereset is in effect an average build-ing load reset method. All sensors re-quired to activate return reset arestandard with the unit.Space and outdoor-air tempera-ture reset — Space temperaturereset and outdoor-air temperaturereset allow for the reset of the leavingfluid temperature based on an exter-nal temperature sensor. (Accessorythermistor required.)Energy management system reset— Many energy management sys-tems have the capability to transmit a4 to 20 mA signal in proportion tothe desired leaving chilled-fluid setpoint. The Flotronic Plus chillers havethe ability to recognize a propor-tioned signal to establish the resetcondition (field-installed componentsare required).Remote alarm — Upon initializationof an alarm condition, an internalcontact will close to activate a signalsuitable for remote alarm activation.Load shed (demand limit) — A2-step demand limit can be pro-grammed through the Flotronic Pluscontrols. The control limits total powerdraw of the unit by controlling thenumber of steps of capacity operatingduring the demand limiting period.Pulldown control — Pulldown con-trol is used to minimize compressorusage and reduce the peak kW thatoccurs at start-up, when the coolerfluid temperature is very warm but theload is small. When activated, thisfeature limits the pulldown rate to1° F (.56° C) per minute.Unit checkout (quick test) — Thequick test feature allows determinationof the status (on or off) of variousFlotronic Plus control components (i.e.,solenoid valves, compressors, andunloaders). When the unit is in standbymode, these steps will energize thesecomponents and indicate whetheror not the components are operational.Diagnostics — The Flotronic Pluscontrol system features extensive self-diagnostics as standard. The displaywill show a 2-digit diagnostic code,and will scroll an explanation of thecode for failures that cause the unit toshut down, terminate a reset option,or use a default value as set point.Time schedule — The Flotronic Pluscontrol system has an integral func-tion that allows scheduling of the cir-culating pump and chiller operationfor up to 8 occupied/unoccupied peri-ods per schedule, with 7 differentschedule days.Table of contents PageFeatures/Benefits . . . . . . . . . . . . . . . . . . . . . . . . . . . . . . . . . . . . . . . . 1-4Model Number Nomenclature . . . . . . . . . . . . . . . . . . . . . . . . . . . . . . . 4Physical Data . . . . . . . . . . . . . . . . . . . . . . . . . . . . . . . . . . . . . . . . . . . 5-8Accessories (Field Installed) . . . . . . . . . . . . . . . . . . . . . . . . . . . . . . . . . 9Base Unit Dimensions . . . . . . . . . . . . . . . . . . . . . . . . . . . . . . . . . . . . 10-12Application Data . . . . . . . . . . . . . . . . . . . . . . . . . . . . . . . . . . . . . . . . 13-16Selection Procedure . . . . . . . . . . . . . . . . . . . . . . . . . . . . . . . . . . . . . . . 17Performance Data . . . . . . . . . . . . . . . . . . . . . . . . . . . . . . . . . . . . . . . 18-28Electrical Data . . . . . . . . . . . . . . . . . . . . . . . . . . . . . . . . . . . . . . . . . . . . 29Typical Field Control Wiring . . . . . . . . . . . . . . . . . . . . . . . . . . . . . . . . . . 30Controls . . . . . . . . . . . . . . . . . . . . . . . . . . . . . . . . . . . . . . . . . . . . . . . 31Typical Piping and Wiring . . . . . . . . . . . . . . . . . . . . . . . . . . . . . . . . . . . 32Guide Specifications . . . . . . . . . . . . . . . . . . . . . . . . . . . . . . . . . . . . . . 33-362 |
Related manuals for Carrier 30HR Series
This manual is suitable for:
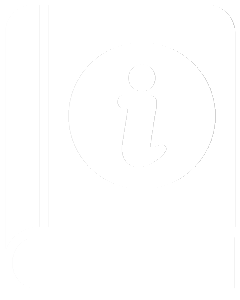
manualsdatabase
Your AI-powered manual search engine