Carrier 45J Installation, Start-up And Service Instructions Manual
Also see for 45J: Installation, Start-Up and Service Instructions
![]() ![]() ![]() ![]() ![]() ![]() ![]() ![]() ![]() ![]() ![]() ![]() ![]() ![]() ![]() ![]() ![]() ![]() ![]() ![]() ![]() ![]() ![]() ![]() | |
![]()
5unit, low voltage controls from the side and line voltagemotor controls or electric heat (if equipped) from the rear(discharge end) of the unit.Bottom access panel removal requires a minimum of 3-in.minimum clearance, plus substantial horizontal clearanceto slide the access panel out of the way for service. Actualhorizontal dimensions will vary due to varying access pan-els for different sized units. See your particular unit’s sub-mittal drawings for more detail.NOTE: Be certain appropriate accommodations for panelremoval of most unit casings are large enough to allow ad-equate internal service room once the panels are removed.A clearance of 18-in. is recommended for control enclosureaccess. Unit control enclosure will vary depending onwhich control package is used. Control enclosure locationis specified on unit submittals. Low voltage enclosure cov-ers are removable, not hinged.A clearance of 36-in. is recommended for line voltage mo-tor controls and electric heat control access. High-voltagemotor controls or electric heat control access is suppliedwith hinged access doors for units with fused disconnect.Specific location is indicated on the unit submittal.NOTE: These recommendations do not supersede NEC(National Electrical Code) or local codes that may be appli-cable, which are the responsibility of the installing contrac-tor.4. Whenever possible, fan-powered boxes should be installedover halls or passageways (rather than over occupied spac-es) in order to limit the sound reaching occupants.POSITION UNIT1. When moving boxes, use appropriate material handlingequipment and avoid contact with shaft extensions, con-trols, wiring, piping, heaters, and control boxes.2. Raise unit to position using safe mechanical equipment andsupport until hanging means are attached and box is level.INSTALL UNIT1. Install field-supplied eye bolts, strap hangers or bolt rodsupports as desired. Figure 6 illustrates possible unit sus-pension methods. A typical installation is shown in Fig. 7.2. Care should be taken to use hanging materials of sufficientstiffness and strength, rigidly attached to the unit. Strapsshould not be located on coil flanges, electric heat sections,or control boxes. When using trapeze supports, avoid areaswhere access is required to side mounted controls, or sideor bottom access doors. For best installation with trapezesupports, provide elastomeric material between unit andsupports.3. Hangers should be securely attached to bar joist or mount-ing anchors properly secured to building structure with lugsor poured-in-place hangers. Percussion nails are not con-sidered adequate anchors.Step 2 — Make Duct Connections1. Install supply ductwork on each of the unit inlet collars. Itis recommended that 3 duct diameters of straight duct aresupplied to the inlet of the unit. An elbow put at the inlet ofthe unit will create turbulence at the inlet making it difficultfor the flow sensor to accurately measure the airflow.Check that the pressure pick-up in primary air collar is lo-cated properly and that air supply duct connections are air-tight. Install supply ductwork on unit inlet collar, followingall accepted medium-pressure duct installation procedures.Seal joints against leakage.NOTE: For maximum efficiency in controlling radiated noise incritical applications, inlet ducts should be fabricated of 24-gageminimum sheet metal in place of flex connections. Flex duct isextremely transparent to radiated sound; consequently high inletstatics (Ps) or sharp bends with excessive pressure drop cancause a radiated noise problem in the space. If flex duct is used,it should be limited to the connection between the distributionduct and the boot diffuser.2. Install the discharge duct. On units with electric heat, therecommended minimum distance of straight duct beforeany transitions, elbows or branch connections is 48 inches.It is strongly recommended that lined discharge duct beused downstream of the unit. Insulate duct as required.3. Fan boxes should not be attached to octopus sections im-mediately downstream of the unit.4. Install optional return-air filters before operating the unit.5. Where construction filters were supplied with the box,leave filters in place until installation is complete andbuilding is cleaned for occupancy.Step 3 — Connect Power Wiring (See Fig. 8)1. All power wiring must comply with local codes and withthe NEC (National Electrical Code) ANSI/NFPA (Ameri-can National Standards Institute/National Fire ProtectionAssociation) 70-2017. Disconnect switches are optionalequipment. Electrical, control and piping diagrams areshown on the exterior labeling or on a diagram inside thecontrol and high-voltage enclosure covers, unless other-wise specified in the order write-up. All units are wired fora single point electrical connection to the fan and electricheater (if equipped). Electric heaters provided by Carrierare balanced by kW per stage. The installing electricianshould rotate incoming electric service by phase to helpbalance overall building load.2. All field wiring must be provided with a safety disconnectper NEC 424-19, 20, and 21.3. Disconnect all incoming power before wiring or servicingunit. All disconnect switches on the terminal (if equipped)should be in the OFF position while making power connec-tions.4. Units with electric heat should use copper wires rated atleast 125% of rating plate amperage. Refer to the unit’s rat-ing label and minimum supply circuit amps.5. Observe wiring diagram and instructions attached to theunit. The 480-v, 3-phase units require a Wye power sourcewith a fourth (neutral) wire in addition to the full sizedground wire. All units must be grounded as required byNEC 424-14 and 250. |
Related manuals for Carrier 45J
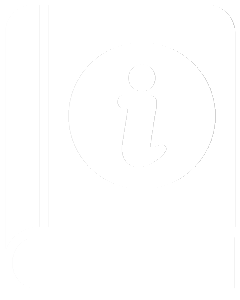
manualsdatabase
Your AI-powered manual search engine