
Eaton MVS Instructional Booklet
![]()
21Instructional Booklet IB02102006EEffective May 2011Type MVS (previously WLImetal-enclosed switchgear4.76 kV, 15.0 kV, 27.0 kV, and 38.0 kVeaton corporation www.eaton.comMethod BFor the following procedure, refer to Figure 29Step 1e: Remove components fastened to the hinge end terminal padand retain for later re-installationStep 2e: Remove the four bolts holding the stationary hinge partsand the terminal pad to the insulator Retain the terminal pad forlater re-installation with the new blade and hinge assemblyStep 3e: Remove the two bolts holding the break jaw to the upperterminal The jaw is now freeStep 4e: Replace the jaw, but only finger tighten its two mountingbolts at this timeStep 5e: Install the new main blade assembly and terminal pad to theinsulator by installing the four bolts, but only finger tightening themat this timeCompleting method A or BStep 6e: Align each blade following the instructions givenin “Closed-Open-Stop adjustment” section on page 18Step 7e: Tighten the jaw mounting boltsStep 8e: Method B only—tighten the blade and hinge assemblymounting boltsStep 9e: Method B only—install all previously retained componentsfastened to the terminal padStep 10e: Align the flicker blade and arc chute following theinstructions given in “Closed-Open-Stop adjustment” section onpage 18Step 11e: Check the flicker blade functioning following theinstructions given in “Main blade alignment” section on page 19If the functioning is satisfactory, connect the drive rod to main bladeStep 12e: Check the switch for adjustments following theinstructions given in sections “Override of the switch interlocksafety latch” through “Arc chute alignment ”Step 13e: Perform the pre-operation check detailed on this pageSpring replacementThe main spring is a large compression spring along the inside ofthe switch frame on the operating handle side (see Figure 30) Forseveral higher fault-close ratings, there is also an auxiliary springconnected to the other end of the main shaft If possible, close theswitch before removal of either springFigure 30. Stored Energy Spring Replacement or AdjustmentMain spring replacementStep 1e: To disengage the main spring, remove the switchmechanism cover (see Figure 23)Step 2e: Take a 5/16”–18 threaded rod 4 00 inches (101 6 mm) longand screw it into the rear end of the spring rodStep 3e: Make a spacer 3 00 inches (76 2 mm) long from a pipe ortube with a 1 00 inch (25 4 mm) I D Put this over the 5/16” rod andthe main spring rodStep 4e: Take a washer with an outside diameter larger than thespacer and place it on the rodStep 5e: Turn a 5/16”–18 nut onto the rod until it is hand-tight andthen center the spacerStep 6e: Use a tool to tighten the nut until the tensionon the pin at the front of the spring rod is releasedStep 7e: Remove one or both of the retaining E-rings holding the pinin place and remove the pin The spring assembly is now free fromthe shaftStep 8e: Loosen the 5/16–18 nut on the piece of all-thread rod torelieve the tensionStep 9e: Remove the piece of all thread from the spring rod The rodand spring now may be removedTo install the main spring assembly, reverse this procedureAuxiliary spring replacementStep 1e: To remove the auxiliary spring, put the switch in the“Closed” position While the compression spring is in its longestcondition, remove the elastic stop nut and bolt holding the springretaining rod to the small arm of the main shaftStep 2e: Pull the spring rod away from its rear support The spring isnow free of the rodTo install the auxiliary spring, reverse the order of this procedureShaft or bearing replacementStep 1e: Disengage the springs as instructed in “Closed-Open-Stopadjustment” section on page 18Step 2e: Remove the drive rods from the switch main shaft ears byunbolting the connectionsStep 3e: Remove the four bolts that hold the bearing support plateson the end of the shaft opposite the operating mechanismStep 4e: Slide the bearing support plates rearward, away fromthe shaftStep 5e: “Spring” the front of the unit slightly if the spring won’tdislodge The bearings can now be removed and replacedStep 6e: To install the bearings or shaft, reverse the order ofthis procedurePre-operation checkAfter completing any maintenance, the alignment should be checked(see page 17) After completing any alignment, the switch shouldbe put through at least three “Close-Open” operations to check forproper performance |
Related manuals for Eaton MVS

Eaton DMVS160N Instruction Leaflet

Eaton DMV160N Instruction Leaflet

Eaton SPD Series Instruction Manual

Eaton PKZ Series Instruction Leaflet

Eaton Bussmann Series Instruction Sheet

Eaton AUX1NO+1NCDMM Instruction Leaflet

Eaton DMM-40 Series Instruction Leaflet

Eaton RAMO5 A Series Instruction Leaflet

Eaton KLV-xUPM-F Series Instruction Leaflet

Eaton Crouse-Hinds Series Instruction Manual
This manual is suitable for:
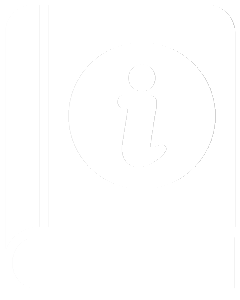
manualsdatabase
Your AI-powered manual search engine