WALKY WL1024 Instructions And Warnings For Installation And Use
Also see for WL1024: Instructions and warnings for installation and useQuick start guide
![]() ![]() ![]() ![]() ![]() ![]() ![]() ![]() ![]() ![]() ![]() ![]() ![]() ![]() ![]() ![]() ![]() ![]() ![]() ![]() ![]() ![]() ![]() ![]() ![]() ![]() ![]() ![]() ![]() ![]() ![]() ![]() ![]() ![]() ![]() ![]() ![]() ![]() ![]() ![]() ![]() ![]() ![]() ![]() ![]() ![]() ![]() ![]() ![]() ![]() ![]() ![]() ![]() ![]() ![]() ![]() ![]() ![]() ![]() ![]() ![]() ![]() ![]() ![]() ![]() ![]() ![]() ![]() ![]() ![]() ![]() ![]() ![]() ![]() ![]() ![]() ![]() ![]() ![]() ![]() ![]() ![]() ![]() ![]() ![]() ![]() ![]() ![]() ![]() ![]() ![]() ![]() ![]() ![]() ![]() ![]() ![]() ![]() ![]() ![]() ![]() ![]() ![]() ![]() ![]() ![]() ![]() ![]() ![]() ![]() ![]() ![]() | |
Contents
| ![]()
ENEnglish – 5The electrical connection of the various devices (photocells, digital keyboards,transponder card readers, etc.) of the automation system with a control unit iscarried out with the Nice “Bluebus” system. This system makes it possible tocarry out the electrical connections with the use of just 2 wires along whichboth the electricity supply and the communication signals travel. The electricalconnection to be used is parallel and does not require any polarity to beobserved. During the recognition phase, every device connected to the controlunit will be recognised individually by the latter, thanks to a univocal code. Everytime a device is added or removed, you must carry out the control unit recogni-tion phase (see paragraph 4.7).4.1 - Description of the electrical connections (fig. 23)M1 gearmotor output 1ELS utput for 12 VAC electrical lock (max 15 VA). The ELS output can beprogrammed with other functions using the Oview programmer (seechapter 8.3) (e.g. flashing, courtesy light, etc.)BLUEBUS input for compatible devices (MOFB, MOFOB, MOB and MOTB).The device connection is in parallel with the use of 2 wires alongwhich both the electricity supply and the communication signalstravel; there is no need to observe any polarity when making theconnection. Each device is recognised individually by the controlunit because a univocal address is assigned to it during the installa-tion (see paragraph 4.7)ELECTRICAL CONNECTIONS4• for phase 12 – Open out the cable fully, cut the excess portion and positionthe cables in such a way that they do not cast any shadows over the LEDs andthe light sensor fitted on the back of the electrical board.• for phase 13 – The arrow on the cover and the one on the base should align.Ensure the 4 cogs on the base fit into the grooves inside the cover.Note – If the WLT multi-purpose lamp is not installed on the upper part of the“Walky” gearmotor, it should be connected to the ELS terminal as described inparagraph 4.1- “Description of the electrical connections”.3.6 - How to remove the control unit01. Remove the gearmotor’s lower cover (fig. 19 phase 1-2);02. Undo the 4 screws of the cable sleeve support and remove it (fig. 24phase 1-2);03. Pull the control unit about 4 centimetres in the direction of the arrow, anddetach the motor connector (fig. 24 phase 3-4);04. Finally, remove the control unit completely;Important! - When reconnecting the motor to the control unit, observe thepolarity of the connector (this can only be inserted one way around!).3.7 - Adjusting the alignment of the gate leaves when closed01. Remove the slotted arm from the fastening bracket on the gate leaf;02. Loosen the screws on the bracket and move it by a few millimetres towardsthe gearmotor;03. Then replace the slotted arm in the bracket, close the leaf and check that itis both aligned with the other leaf and in contact with the end stop. Impor-tant! - If necessary, repeat point 02 until an optimum alignment is achieved;04. Drill a hole in the leaf, to correspond to the hole in the centre of the fasten-ing bracket, and insert a screw. Then fix the bracket permanently in placeby tightening the three screws;05. Finally, attach the slotted arm to the bracket, inserting the pin and the Ben-zing retaining ring.3.8 - Securing and releasing the gearmotor manuallyThe gearmotor is equipped with a mechanical system which allows the gate tobe opened and closed manually.These manual operations are required in the event of power cuts, operationalfaults, or during installation.Releasing (fig. 22-A):01. Raise the flap;02. Insert the key into the release pin;03. Turn the key by almost a full turn clockwise.04. The gate leaf can now be moved manually into the required position.Securing (fig. 22-B):01. Turn the key anticlockwise in the release pin and move the gate leaf manu-ally until you can hear the leaf engage mechanically with the drive mecha-nism.02. Remove the key from the pin and rotate the release disc anticlockwise by90° so that the hole is blocked and replace the flap.STOP input for devices which, when activated, cause the manoeuvre inprogress to halt immediately, followed by a brief inversion; possibili-ty of connecting NO, NC contacts or devices with a 8.2 kΩ con-stant resistance output (sensitive edges). Each device connected tothis input is recognised individually by the control unit during therecognition phase (paragraph 4.7); after this phase, if the controlunit detects any variation with respect to the status recognised, itcauses a STOP. One or more devices - including different ones -can be connected to this input:– several NO devices can be connected in parallel, with no limits asto quantity;– several NC devices can be connected in series, with no limits asto quantity;– 2 devices with a 8.2 kΩ constant resistance output can be con-nected in parallel. If there are more than 2 devices, they need to beconnected in a cascade configuration with a single terminationresistance of 8.2 kΩ;– 2 NO and NC devices can be connected in parallel, connecting inseries with the NC contact a 8.2 kΩ resistance (this makes thecombination of 3 NO - NC and 8.2 kΩ devices possible)P.P. input for control devices which, when activated, cause the Step-step manoeuvre to take place; possibility of connecting NO contactsAERIAL input for the aerial of a radio receiver4.2 - Connecting the power cableWARNING: The electricity supply line must be equipped with a device whichensures the complete disconnection of the automation system from the mains.The disconnection device’s contacts must have an opening distance which issufficient to achieve full disconnection in category III overload conditions, inconformance with the rules of installation. When the need arises, this deviceensures that the power is disconnected quickly and safely; it must therefore bepositioned where it can be seen from the automation system. If, however, it isnot located in a visible position, it must be provided with a system to preventthe power supply being reconnected accidentally or without authorisation, inorder to avoid any risk. The product is not supplied with a disconnectiondevice.IMPORTANT!– The connection must be carried out exclusively by qualified experts.– All electrical connections must be carried out without any mains electri-cal power supply and with the back-up battery disconnected - wherepresent in the automation system.01. Access the power unit by undoing the 3 screws in the gearmotor’s uppercover and slowly rotate the cover in the direction of the arrow (fig. 24),keeping a careful eye on the cables underneath;02. Connect the phase and neutral wires to the power unit terminal board,observing the instructions on the label; close the earth cable grommetusing the screw (fig. 25): care required! -the terminal should be pointingtowards the opening from which the power cable emerges;03. Then pull the power cable towards the control unit, so that it is just longenough to allow the power unit to rotate and the cover to close;04. Close the power unit cover; tighten the screws on the cable gland; insertthe control unit into its seat, and remount the cable sleeve support;Important! - Fasten the cover of the power unit with all the screwsand ensure that the seal is well positioned in its seat. If the seal or oneof the screws is missing, this can compromise the electronics inside.4.3 - Connecting the gearmotor without a control unit mod.WL102401. Remove the lower cover of the gearmotor without control unit, as shown infig. 19, phase 1-2;02. Using a Phillips screwdriver, undo the 4 screws of the cable sleeve support(fig. 20) and remove it (important! - do not lose the 2 spacers).03. Loosen the two screws on the cable gland (fig. 20, phase 6) and feed theconnection cable through; connect the 3 cables to the terminal board,observing the symbols as labelled; then tighten the screws of the cablegland.04. Adjust the 2 feet inside the gearmotor with an Allen key, until they are fullyresting on the column (fig. 20, phase 7).05. Cut the edge of the cable sleeve support (fig. 20, phase 8); put the 2 spac-ers back into position; remount the cable sleeve support (fig. 20, phase 9)and replace the gearmotor’s lower cover (fig. 20, phase 10).4.4 - Connecting other devicesIf you need to power further devices in the system, such as a transponder cardreader or the light for the key selector, these devices can be connected to thecontrol unit on terminals “P.P. (positive)” and “STOP (negative)” (fig. 23). Thesupply voltage varies from 18 to 31 VDC when mains or solemyo operated andfrom 11 to approx. 14 VDC when operating on back-up battery PS424. Themaximum available current is 200 mA.Note – The voltage available in terminals “P.P.” and “STOP” remains presenteven when the “Stand By” function is activated on the board. |
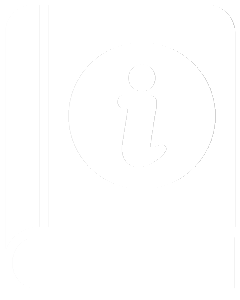
manualsdatabase
Your AI-powered manual search engine