ABB IRB 7600 manuals

IRB 7600
Table of contents
- Table Of Contents
- Table Of Contents
- Table Of Contents
- Table Of Contents
- Overview of this manual
- Circuit diagram
- Spare part lists
- Product manual, spare parts - IRB
- Product documentation, M2000/M2000A
- Product documentation, IRC5
- How to read the product manual
- Safety
- Protective stop and emergency stop
- Safety actions
- Emergency release of the robot axes
- Make sure that the main power has been switched off
- Safety risks
- Moving robots are potentially lethal
- First test run may cause injury or damage
- Work inside the working range of the robot
- Enabling device and hold-to-run functionality
- Risks associated with live electric parts
- The unit is sensitive to ESD
- Hot parts may cause burns
- Safety risks related to pneumatic/hydraulic systems
- Brake testing
- Safety risks during handling of batteries
- Safety risks during work with gearbox lubricants (oil or grease)
- Safety signals and symbols
- Safety symbols on product labels
- Installation and commissioning
- Robot transportation precautions
- Securing the robot with a transport support
- Unpacking
- Working range, IRB 7600 - 150/3.5
- Working range, IRB 7600 - 340/2.8
- Working range, IRB 7600 - 400/2.55, IRB 7600 - 500/2.55
- Working range, IRB 7600 - 500/2.3
- Risk of tipping/stability
- On-site installation
- Lifting robot with lifting slings
- Lifting robot with roundslings
- Manually releasing the brakes
- Lifting the base plate
- Securing the base plate
- Orienting and securing the robot
- Fitting equipment on robot
- Installation of base spacers (option)
- Extended working range, axis 1 (option 561-1)
- Installation of cooling fan for motors (option)
- Installation of Foundry Plus Cable guard (option no. 908-1)
- Loads fitted to the robot, stopping time and braking distances
- Signal lamp (option)
- Restricting the working range
- Mechanically restricting the working range of axis 1
- Mechanically restricting the working range of axis 2
- Mechanically restricting the working range of axis 3
- Installation of position switches (option)
- Electrical connections
- Start of robot in cold environments
- Maintenance
- Maintenance schedule and expected life
- Maintenance schedule
- Expected component life
- Inspection activities
- Inspecting the oil level in axis-1 gearbox
- Inspecting the oil level in axis-2 gearbox
- Inspecting the oil level in axis-3 gearbox
- Inspecting the oil level in axis-4 gearbox
- Inspecting the oil level in axis-5 gearbox
- Inspecting the oil level in axis-6 gearbox
- Inspecting the balancing device
- Inspecting the cable harness
- Inspecting the axis-1 mechanical stop pin
- Inspecting the mechanical stops on axes 1, 2, and 3
- Inspecting the damper on axes 2 to 5
- Inspecting the position switch on axes 1, 2, and 3
- Inspecting the information labels
- Inspecting the UL lamp
- Changing/replacement activities
- Changing oil, axis-1 gearbox
- Changing oil, axis-2 gearbox
- Changing oil, axis-3 gearbox
- Changing oil, axis-4 gearbox
- Changing oil, axis-5 gearbox
- Changing oil, axis-6 gearbox
- Replacing the SMB battery
- Lubrication activities
- Cleaning activities
- Cleaning the IRB 7600
- Service Information System, M2000
- Description of Service Information System (SIS)
- SIS system parameters
- Setting the SIS parameters
- Reading the SIS output logs
- Exporting the SIS data
- Repair
- General procedures
- Mounting instructions for bearings
- Product manual - IRB
- Mounting instructions for seals
- Cut the paint or surface on the robot before replacing parts
- The brake release buttons may be jammed after service work
- Complete robot
- Replacement of cable harness, axes 5-6
- Replacement of complete arm system
- Upper and lower arm
- Replacement of complete wrist unit
- Replacement of complete upper arm
- Replacement of complete lower arm
- Replacement of lower arm shaft
- Frame and base
- Replacement of brake release board
- Replacement of spherical roller bearing, balancing device
- Replacement of balancing device
- Unloading the balancing device using hydraulic press tool
- Restoring the balancing device using a hydraulic press tool
- Motors
- Replacement of motor axis 2
- Replacement of motor, axis 3
- Replacement of motor, axis 4
- Replacement of motor, axis 5
- Replacement of motor, axis 6
- Gearboxes
- Replacement of gearbox, axis 2
- Replacement of gearbox, axis 3
- Replacement of gearbox, axis 4
- Replacement of gearbox, axis 5
- Replacement of gearbox, axis 6
- Calibration
- Calibration methods
- When to calibrate
- Synchronization marks and axis movement directions
- Calibration movement directions for all axes
- Updating revolution counters
- Calibrating with Axis Calibration method
- Calibration tools for Axis Calibration
- Installation locations for the calibration tools
- Axis Calibration - Running the calibration procedure
- Calibrating with Calibration Pendulum method
- Verifying the calibration
- Checking the synchronization position
- Decommissioning
- Scrapping of robot
- Decommissioning of balancing device
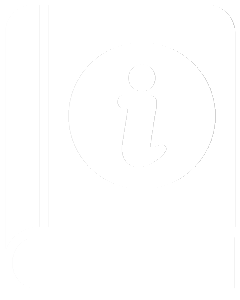
manualsdatabase
Your AI-powered manual search engine