ABB IRB 7600-400/2.55 manuals

IRB 7600-400/2.55
Table of contents
- Table Of Contents
- Table Of Contents
- Table Of Contents
- Table Of Contents
- Overview of this manual
- Circuit diagram
- Spare part lists
- Product manual, spare parts - IRB
- Product documentation, M2000/M2000A
- Product documentation, IRC5
- How to read the product manual
- Safety
- Protective stop and emergency stop
- Safety actions
- Emergency release of the robot axes
- Make sure that the main power has been switched off
- Safety risks
- Moving robots are potentially lethal
- First test run may cause injury or damage
- Work inside the working range of the robot
- Enabling device and hold-to-run functionality
- Risks associated with live electric parts
- The unit is sensitive to ESD
- Hot parts may cause burns
- Safety risks related to pneumatic/hydraulic systems
- Brake testing
- Safety risks during handling of batteries
- Safety risks during work with gearbox lubricants (oil or grease)
- Safety signals and symbols
- Safety symbols on product labels
- Installation and commissioning
- Robot transportation precautions
- Securing the robot with a transport support
- Unpacking
- Working range, IRB 7600 - 150/3.5
- Working range, IRB 7600 - 340/2.8
- Working range, IRB 7600 - 400/2.55, IRB 7600 - 500/2.55
- Working range, IRB 7600 - 500/2.3
- Risk of tipping/stability
- On-site installation
- Lifting robot with lifting slings
- Lifting robot with roundslings
- Manually releasing the brakes
- Lifting the base plate
- Securing the base plate
- Orienting and securing the robot
- Fitting equipment on robot
- Installation of base spacers (option)
- Extended working range, axis 1 (option 561-1)
- Installation of cooling fan for motors (option)
- Installation of Foundry Plus Cable guard (option no. 908-1)
- Loads fitted to the robot, stopping time and braking distances
- Signal lamp (option)
- Restricting the working range
- Mechanically restricting the working range of axis 1
- Mechanically restricting the working range of axis 2
- Mechanically restricting the working range of axis 3
- Installation of position switches (option)
- Electrical connections
- Start of robot in cold environments
- Maintenance
- Maintenance schedule and expected life
- Maintenance schedule
- Expected component life
- Inspection activities
- Inspecting the oil level in axis-1 gearbox
- Inspecting the oil level in axis-2 gearbox
- Inspecting the oil level in axis-3 gearbox
- Inspecting the oil level in axis-4 gearbox
- Inspecting the oil level in axis-5 gearbox
- Inspecting the oil level in axis-6 gearbox
- Inspecting the balancing device
- Inspecting the cable harness
- Inspecting the axis-1 mechanical stop pin
- Inspecting the mechanical stops on axes 1, 2, and 3
- Inspecting the damper on axes 2 to 5
- Inspecting the position switch on axes 1, 2, and 3
- Inspecting the information labels
- Inspecting the UL lamp
- Changing/replacement activities
- Changing oil, axis-1 gearbox
- Changing oil, axis-2 gearbox
- Changing oil, axis-3 gearbox
- Changing oil, axis-4 gearbox
- Changing oil, axis-5 gearbox
- Changing oil, axis-6 gearbox
- Replacing the SMB battery
- Lubrication activities
- Cleaning activities
- Cleaning the IRB 7600
- Service Information System, M2000
- Description of Service Information System (SIS)
- SIS system parameters
- Setting the SIS parameters
- Reading the SIS output logs
- Exporting the SIS data
- Repair
- General procedures
- Mounting instructions for bearings
- Product manual - IRB
- Mounting instructions for seals
- Cut the paint or surface on the robot before replacing parts
- The brake release buttons may be jammed after service work
- Complete robot
- Replacement of cable harness, axes 5-6
- Replacement of complete arm system
- Upper and lower arm
- Replacement of complete wrist unit
- Replacement of complete upper arm
- Replacement of complete lower arm
- Replacement of lower arm shaft
- Frame and base
- Replacement of brake release board
- Replacement of spherical roller bearing, balancing device
- Replacement of balancing device
- Unloading the balancing device using hydraulic press tool
- Restoring the balancing device using a hydraulic press tool
- Motors
- Replacement of motor axis 2
- Replacement of motor, axis 3
- Replacement of motor, axis 4
- Replacement of motor, axis 5
- Replacement of motor, axis 6
- Gearboxes
- Replacement of gearbox, axis 2
- Replacement of gearbox, axis 3
- Replacement of gearbox, axis 4
- Replacement of gearbox, axis 5
- Replacement of gearbox, axis 6
- Calibration
- Calibration methods
- When to calibrate
- Synchronization marks and axis movement directions
- Calibration movement directions for all axes
- Updating revolution counters
- Calibrating with Axis Calibration method
- Calibration tools for Axis Calibration
- Installation locations for the calibration tools
- Axis Calibration - Running the calibration procedure
- Calibrating with Calibration Pendulum method
- Verifying the calibration
- Checking the synchronization position
- Decommissioning
- Scrapping of robot
- Decommissioning of balancing device

IRB 7600-400/2.55
Table of contents
- Table Of Contents
- Table Of Contents
- Table Of Contents
- Table Of Contents
- Table Of Contents
- Overview of this manual
- Product documentation, M2000/M2000A
- Product documentation, M2004
- How to read the product manual
- Safety
- General safety information
- Safety risks
- CAUTION - Hot parts may cause burns
- Safety risks related to tools/work pieces
- Safety risks related to pneumatic/hydraulic systems
- Safety risks during operational disturbances
- Risks associated with live electric parts
- Safety actions
- Fire extinguishing
- Emergency release of the manipulator's arm
- Brake testing
- Risk of disabling function "Reduced speed 250 mm/s
- Safe use of the FlexPendant
- Work inside the manipulator's working range
- Signal lamp (optional)
- Safety stops
- Safety related instructions
- Safety symbols on manipulator labels
- DANGER - Moving manipulators are potentially lethal
- DANGER - First test run may cause injury or damage
- WARNING - The brake release buttons may be jammed after service work
- WARNING - The unit is sensitive to ESD
- WARNING - Safety risks during work with gearbox lubricants (oil or grease)
- Installation and commissioning
- Robot transportation precautions
- Securing the robot
- Unpacking
- Working range, IRB 7600 - 150/3.5
- Working range, IRB 7600 - 340/2.8
- Working range, IRB 7600 - 400/2.55, IRB 7600 - 500/2.55
- Working range, IRB 7600 - 500/2.3
- Risk of tipping/stability
- On-site Installation
- Lifting robot with lifting slings
- Lifting robot with roundslings
- Manually releasing the brakes
- Manually releasing the brakes, external brake release unit
- Lifting the base plate
- Securing the base plate
- Orienting and securing the robot
- Fitting equipment on robot
- Installation of base spacers (option)
- Installation of cooling fan for motors, axes 1-3 (option)
- Installation of Foundry Plus Cable guard (option no. 908-1)
- Loads
- Restricting the working range
- Mechanically restricting the working range of axis 1
- Mechanically restricting the working range of axis 2
- Mechanically restricting the working range of axis 3
- Installation of position switches (option)
- Electrical connections
- Making robot ready for operation (Foundry Prime)
- Commissioning (Foundry Prime)
- Maintenance
- Maintenance schedule and expected life
- Maintenance schedule
- Expected component life
- Inspection activities
- Inspection, oil level gearbox axis 2
- Inspection, oil level gearbox axis 3
- Inspection, oil level gearbox axis 4
- Inspection, oil level, gearbox axis 5
- Inspection, oil level gearbox axis 6
- Inspection, balancing device
- Inspection, cable harness
- Inspecting, mechanical stop pin, axis 1
- Inspection, mechanical stop, axes 1, 2 and 3
- Inspection, damper axes 2-5
- Inspection, position switch axes 1, 2 and 3
- Inspection, information labels
- Inspection, UL-lamp
- Inspection of air hoses (Foundry Prime)
- Changing/replacement activities
- Oil change, gearbox axis 1
- Oil change, gearbox axis 2
- Oil change, gearbox, axis 3
- Oil change, gearbox, axis 4
- Oil change, gearbox, axis 5
- Oil change, gearbox axis 6
- Replacing SMB battery
- Lubrication activities
- Rust preventive measures, bearing axis 1 (Foundry Prime)
- Rust preventive measures, sealing axis 4 (Foundry Prime)
- Rust preventive measures, support bearing in wrist (Foundry Prime)
- Cleaning activities
- Cleaning, robot
- Service Information System, M2000
- Description of Service Information System (SIS)
- SIS system parameters
- Setting the SIS parameters
- Reading the SIS output logs
- Exporting the SIS data
- Repair
- General procedures
- Mounting instructions for bearings
- Mounting instructions for seals
- Complete robot
- Replacement of cable harness, axes 5-6
- Replacement of complete arm system
- Replacement of air nipple and hose (Foundry Prime)
- Upper and lower arm
- Replacement of complete wrist unit
- Replacement of complete upper arm
- Replacement of complete lower arm
- Frame and base
- Replacement of brake release unit
- Replacement of balancing device
- Replacement of spherical roller bearing, balancing device
- Unloading the balancing device using hydraulic press tool
- Restoring the balancing device using a hydraulic press tool
- Motors
- Replacement of motor axis 2
- Replacement of motor, axis 3
- Replacement of motor, axis 4
- Replacement of motor, axis 5
- Replacement of motor, axis 6
- Gearboxes
- Replacement of gearbox, axis 2
- Replacement of gearbox, axis 3
- Replacement of gearbox, axis 4
- Replacement of gearbox, axis 5
- Replacement of gearbox, axis 6
- Calibration information
- Calibration methods
- Calibration scale and correct axis position
- Calibration movement directions for all axes
- Updating revolution counters
- Checking the calibration position
- Decommissioning
- Decommissioning of balancing device
- Reference information
- Applicable safety standards
- Unit conversion
- Screw joints
- Weight specifications
- Standard toolkit
- Special tools
- Lifting accessories and lifting instructions
- Spare part / part list
- Spare parts
- Spare part list
- Part list
- Rebuilding parts
- Part list, overview
- Mechanical stop axis 1, 3HAC12812-2
- Base incl frame axis 1, 3HAC12304-1
- Axis 3-4, 3HAC13063-1 (IRB 7600 - 150/3.5, - 325/3.1, -340/2.8, -400/2.55, -500/2.55)
- Axis 3-4, 3HAC13063-2 (IRB 7600 - 500/2.3)
- Axis 3-4 Foundry, 3HAC13063-5 (IRB 7600 - 500/2.3)
- Wrist, 3HAC16628-4 / 3HAC16628-3
- Material set robot, 3HAC13079-1
- Material set axis 1-2, 3HAC13077-1
- Material set balancing device, 3HAC13082-1
- Arm extension set, 956 mm, 3HAC12311-1 (IRB 7600 - 150/3.5)
- Arm extension set, 250 mm, 3HAC12311-2 (IRB 7600 - 340/2,8)
- Exploded views
- Base incl. Frame
- Frame-Lower arm 1
- Frame-Lower arm 2
- Upper arm
- Wrist complete
- Circuit Diagram
- Circuit diagram 3HAC 025744-001
- Circuit diagram 3HAC 13347-1
- Index
Related products
IRB 7600 - 400/2.55IRB 7600-500/2.55IRB 7600 - 500/2.55IRB 4600 - 40/2.55IRB 7600 - 500/2.3IRB 7600-500/2.3IRB 7600400/2.55IRB 6600 - 225/2.55IRB 7600-340/2.8ABB categories
Industrial Equipment
DC Drives
Controller
Relays
Measuring Instruments
Circuit breakers
Battery Charger
Industrial Electrical
Transformer
Switch
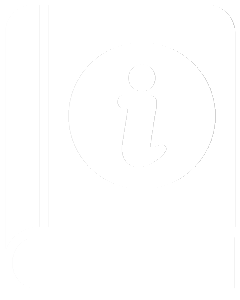
manualsdatabase
Your AI-powered manual search engine