ABB ACS560 manuals

ACS560
Table of contents
- Table Of Contents
- Table Of Contents
- Table Of Contents
- Table Of Contents
- Table Of Contents
- Table Of Contents
- Contents of this chapter
- General safety in installation, start-up and maintenance
- Electrical safety in installation, start-up and maintenance
- Additional instructions and notes
- Grounding
- General safety in operation
- Quick installation and commissioning flowchart
- Terms and abbreviations
- Related documents
- Layout
- Frame size R3
- Frame R4...R8
- Overview of power and control connections
- External control connecting terminal, Frame size R0...R2
- External control connecting terminal, Frame size R3...R5
- External control connection terminals, frames R6...R8
- Control panel
- Type designation label
- Locations of the labels on the drive
- Type designation key
- Checking the installation site
- Required tools
- Unpacking and examining delivery, frames R3...R4
- Unpacking and examining delivery, frames R5
- Unpacking and examining delivery, frames R6...R8
- Installing the drive
- Installing the drive vertically, frame size R3...R4
- Installing the drive vertically, frames size R5...R8
- Installing the drive vertically side by side
- Other regions
- Alternative power cable types
- Recommended power cable types
- Conduit
- Signals in separate cables
- Separate control cable ducts
- Protecting the motor and motor cable in short-circuits
- Implementing the Safe torque off function
- Switching the motor power supply from drive to direct-on-line
- Switching the motor power supply from direct-on-line to drive
- Input power cable
- Checking the compatibility with IT (ungrounded) and corner-grounded TN systems
- Frames R0...R3
- Frames R4...R8
- Connecting the power cables
- Connection procedure, frames R0...R2
- electrical installation
- Finalization
- Motor cable
- Notes
- Connection procedure, frames R5...R8
- Notes for frame R8
- DC connection
- Default control connections for the ABB standard macro
- PNP configuration for digital inputs
- Connection for obtaining 0...10 V from analog output 2 (AO2)
- DI5 as frequency input
- Safe torque off (X4)
- R0...R2
- R3...R5
- R6...R8
- Option slot 1 (fieldbus adapter modules)
- Reinstalling covers, frame size R3, R4
- Recommended annual maintenance actions by the user
- Heatsink
- Replacing the cooling fan, frames size R0...R4
- Replacing the main cooling fan, frames size R6...R8
- Replacing the auxiliary cooling fan, frames R6...R8
- Capacitors
- LEDs
- Definitions
- Sizing
- Switching frequency derating
- Fuses (IEC)
- gG fuses
- gR fuses
- Circuit breakers
- Dimensions, weights and free space requirements
- Thermal losses, cooling data and noise
- Terminal and lead-through data for the power cables
- Terminal and lead-through data for the control cables
- Electrical power network specification
- EMC compatibility and motor cable length
- Brake resistor connection data for frames R0...R3
- Auxiliary circuit power consumption
- Degree of protection
- Materials
- CE marking
- Compliance with the EN 61800-3:2004 + A1:2012
- Category C3
- Frame R0, IP20
- Frame R1, IP20
- Frame R3, IP20
- Frame R5, IP20
- Frame R6, IP20
- Frame R7, IP20
- Frame R8, IP20
- Selecting and routing the brake resistor cables
- Placing the brake resistor
- Mechanical installation
- Resistor braking, frames R4...R8
- What this chapter contains
- Compliance with the European Machinery Directive
- Connection principle (R0...R2)
- Connection principle (R3-R8)
- Activation switch
- Grounding of protective shields
- Acceptance test reports
- Maintenance
- Safety data
- Abbreviations
- Declaration of conformity
- Description, installation and technical data of the FOCH filters
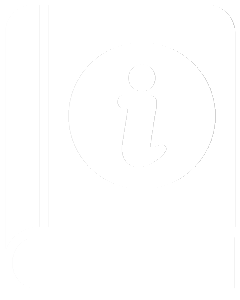
manualsdatabase
Your AI-powered manual search engine