ABB ACS800-07 manuals

ACS800-07
Table of contents
- ACS800 Single Drive Manuals
- What this chapter contains
- Installation and maintenance work
- Grounding
- Operation
- Permanent magnet motor drives
- Table Of Contents
- Table Of Contents
- Table Of Contents
- Table Of Contents
- Table Of Contents
- Table Of Contents
- Installation and commissioning flowchart
- Product and service inquiries
- Terms and abbreviations
- Swing-out frame
- Cabling direction
- Single-line circuit diagram of the drive
- Controls
- Supply unit control electronics
- Reading and setting of values (page 1 of
- Terminal blocks
- Digital input and relay output terminals
- Emergency stop input
- Earth (ground) current function
- Power loss ride-through function
- Motor control
- Type code
- Moving the unit
- by fork-lift or pallet truck
- Final placement of the unit
- Before installation
- Installation procedure
- Fastening the cabinet to the floor (Non-marine units)
- Holes inside the cabinet
- Fastening the unit to the floor and wall (Marine units)
- Joining the shipping splits
- Connecting the DC busbars and the PE busbar
- DC busbars
- Miscellaneous
- Cooling air intake through bottom of cabinet
- Electric welding
- Protecting the motor insulation and bearings
- Requirements table
- Permanent magnet synchronous motor
- Thermal overload protection of the motor
- Emergency stop devices
- Alternative power cable types
- Conduit
- Power factor compensation capacitors
- Relay output contacts and inductive loads
- Selecting the control cables
- Connection of a motor temperature sensor to the drive I/O
- Control cable ducts
- Electrical installation
- IT (ungrounded) systems
- Input power connection – Units without load switch-disconnector or air circuit breaker
- pulse connection, two supply modules in parallel
- Connection procedure
- Use of the dual-cable screw lug connector
- Input power connection – Units with load switch-disconnector or air circuit breaker
- Motor connection – Units without common motor terminal cubicle
- Motor connection – Units with common motor terminal cubicle
- Control connections
- Installation of optional modules and PC
- Connections and tap settings of the auxiliary voltage transformer
- Note on external power supply
- External control connections (non-US)
- External control connections (US)
- RMIO board specifications
- Relay outputs
- Installation checklist
- Start-up procedure
- Starting the supply unit
- Maintenance intervals
- Replacing the PPCS branching unit (APBU-xx) memory backup battery
- Checking and replacing the air filters
- Cooling fans
- Inverter module fan replacement
- Control and I/O cubicle cooling fans
- Air circuit breaker cubicle fans
- Heatsinks
- Other LEDs of the drive
- Symbols
- ACS800-07 frame sizes and power module types
- Internal AC fuses
- DC fuses at inverter module input
- Input power connection
- Motor connection
- Efficiency
- Cooling
- Materials
- CE marking
- Second environment
- C-tick" marking
- Cabinet line-ups
- Frame size 1×D4 + 2×R8i
- Frame size 1×D4 + 2×R8i (with load switch-disconnector)
- Frame size 1×D4 + 2×R8i (with top entry/exit)
- Frame size 2×D4 + 2×R8i
- Frame size 2×D4 + 2×R8i (with load switch-disconnector)
- Frame size 2×D4 + 3×R8i
- Frame size 2×D4 + 3×R8i (with load switch-disconnector)
- Frame size 2×D4 + 3×R8i (with air circuit breaker)
- Frame size 3×D4 + 4×R8i
- Frame size 3×D4 + 4×R8i (with load switch-disconnector)
- Frame size 3×D4 + 4×R8i (with air circuit breaker)
- Common motor terminal cubicle
- Chopper/Resistor combinations – Technical data
- Verifying the capacity of the braking equipment
- Calculating the maximum braking power (P br )
- Example 3
- Custom resistor installation and wiring
- Brake circuit commissioning

ACS800-07
Table of contents
- List of related manuals
- What this chapter contains
- Installation and maintenance work
- Grounding
- Mechanical installation and maintenance
- Operation
- Permanent magnet synchronous motor
- Table Of Contents
- Table Of Contents
- Table Of Contents
- Table Of Contents
- Table Of Contents
- Table Of Contents
- Contents
- Installation and commissioning flowchart
- Terms and abbreviations
- Type designation key
- Main circuit and control
- Diagram
- Printed circuit boards
- Before installation
- Cooling air flow
- Fastening the cabinet to the floor and wall (non-marine units)
- Fastening the cabinet with the outside brackets
- Fastening the cabinet through the holes inside the cabinet
- Fastening the cabinet to the floor and roof/wall (marine units)
- Electric welding
- Protecting the motor insulation and bearings
- Requirements table
- Additional requirements for explosion-safe (EX) motors
- Additional requirements for non-ABB high-output and IP23 motors
- Additional data for calculating the rise time and the peak line-to-line voltage
- Thermal overload and short-circuit protection
- Protection against short-circuit inside the drive or in the supply cable
- Ground fault protection
- Prevention of unexpected start-up
- Safe torque off (STO)
- Selecting the power cables
- Alternative power cable types
- Additional US requirements
- Equipment connected to the motor cable
- Protecting the relay output contacts and attenuating disturbances in case of inductive loads
- Selecting the control cables
- Connection of a motor temperature sensor to the drive I/O
- Control cable ducts
- Electrical installation
- Brake resistor assembly
- Example wiring diagram
- Power cable connection diagram
- Connecting the power cables
- Additional instructions for frame size R6
- Connecting the control cables
- Routing the cables (frame sizes R7 and R8)
- degrees EMC grounding at the cable entry
- Special for top entry
- Connecting the cables to the I/O terminals
- Settings of the cooling fan transformer
- Pulse encoder module cabling
- Layout drawing of factory installed optional equipment
- Frame size R7 and R8
- Note on external power supply
- External control connections (non-US)
- External control connections (US)
- RMIO board specifications
- Relay outputs
- Start-up procedure
- Required tools for maintenance
- Cabinet layout
- Frame sizes R7 and R8 without du/dt filter
- Frame sizes R7 and R8 with du/dt filter
- Designations
- Layout of the drive module
- Checking and replacing the air filters
- Replacing the drive module fan (R5 and R6)
- Replacing the drive module fan (R7)
- Replacing the drive module fan (R8)
- Replacing the cabinet fans (R5 and R6)
- Replacing the cabinet fans (frame size R8 only)
- Replacing the IP54 (UL type 12) fan in frame size R6 (option +B055 and +B059)
- Replacing the IP54 (UL type 12) fan in frame sizes R7 and R8 (option +B055 and +B059)
- Capacitors
- Replacing the capacitor pack (R8)
- Replacing the drive module (R5 and R6)
- Replacing the drive module (R7 and R8)
- LEDs
- Symbols
- Fuses
- Notes concerning the fuse tables
- Ultrarapid (aR) fuses
- Optional gG fuses
- Quick guide for selecting between gG and aR fuses
- Cable types
- Cable entries
- NEMA data
- Free space around the unit
- Input power connection
- Cooling
- Materials
- CE marking
- Second environment (drive of category C3)
- C-tick" marking
- UL/CSA markings
- Dimensional drawings
- Frame sizes R5 and R6
- Frame sizes R7 and R8
- IP54 and IP54R units of frame sizes R7 and R8
- Optional brake chopper and resistor(s)
- Resistor installation and wiring
- Protection of frame sizes R6, R7 and R8
- Product and service inquiries
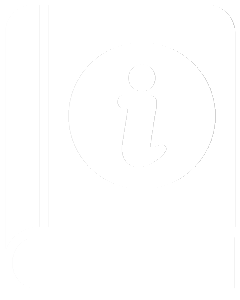
manualsdatabase
Your AI-powered manual search engine