Danfoss vlt aqua manuals

vlt aqua
Table of contents
- Table Of Contents
- Table Of Contents
- How to Read this Design Guide
- Symbols
- Abbreviations
- Introduction to the VLT AQUA Drive
- CE labeling
- Vibration and shock
- Control Structures
- General aspects of EMC
- Immunity Requirements
- Galvanic isolation (PELV)
- Ground leakage current
- Control with brake function
- Safe Stop Operation (optional)
- VLT AQUA Selection
- Efficiency
- Special Conditions
- Options and Accessories
- Index
- General Description
- High Power Options
- Outside Installation/ NEMA 3R Kit for Rittal enclosures
- Installation on Pedestal
- Input Plate Option
- Installation of Line Power Shield for Adjustable Frequency Drives
- Frame size F Panel Options
- How to Order
- Type Code String
- Ordering Numbers
- How to Install
- Pre-installation
- Lifting
- Cooling and Airflow
- Electrical Installation
- Connections - Frame sizes D, E and F
- Disconnectors, circuit breakers and contactors
- Final Set-Up and Test
- Safe Stop Installation
- Safe Stop Commissioning Test
- Additional Connections
- Installation of misc. connections
- Safety
- Residual Current Device
- Application Examples
- Potentiometer Reference
- SLC Application Example
- System Status and Operation
- Cascade Controller Wiring Diagram
- Lead Pump Alternation Wiring Diagram
- RS-485 Installation and Set-up
- FC Protocol Overview
- Network Configuration
- Examples
- Modbus RTU Overview
- Modbus RTU Message Framing Structure
- How to Access Parameters
- Danfoss FC Control Profile

vlt aqua
Table of contents
- Table Of Contents
- How to Read this Instruction Manual
- Approvals
- Safety
- General Warning
- Avoid unintended Start
- Safe Stop of the Adjustable Frequency Drive (optional)
- Introduction
- Mechanical installation
- Electrical installation
- Specifications
- DC bus connection
- Relay Connection
- How to program the adjustable frequency drive
- Electrical Installation and Control Cables
- How to Test Motor and Direction of Rotation
- Troubleshooting
- Application Examples
- Submersible Pump Application
- How to operate the adjustable frequency drive
- How to operate the numeric LCP (NLCP)
- Tips and tricks
- Q1 My Personal Menu
- Q2 Quick Set-up
- Q5 Changes Made
- Commonly Used Parameters - Explanations
- Default settings
- Brakes
- Analog In/Out
- Index
- Fault messages
- Special Conditions
- Smart Logic
- Motor wiring overview
- Application Functions

vlt aqua
Table of contents
- Table Of Contents
- How to Read these Operating Instructions
- Safety
- General Warning
- Avoid unintended Start
- IT Mains
- Introduction
- Type Code String
- Mechanical installation
- How to install
- Electrical installation
- Mains wiring overview
- How to connect motor - foreword
- Motor wiring overview
- How to Test Motor and Direction of Rotation
- Application Examples
- Submersible Pump Application
- How to operate the frequency converter
- How to operate numeric LCP (NLCP)
- Tips and tricks
- How to programme the frequency converter
- Q1 My Personal Menu
- Q5 Changes Made
- Common Used Parameters - Explanations
- Parameter Options
- Troubleshooting
- Brakes 2
- Warning/Alarm list
- Specifications
- Special Conditions
- Digital In/Out 5
- Profibus 9

vlt aqua
Table of contents
- Table Of Contents
- How to Read this Design Guide
- Abbreviations
- Introduction to VLT AQUA Drive
- CE labelling
- Air humidity
- Vibration and shock
- VLT AQUA Controls
- General aspects of EMC
- Galvanic isolation (PELV)
- Control with brake function
- Mechanical brake control
- Extreme running conditions
- Safe Stop Operation (optional)
- VLT AQUA Selection
- Efficiency
- Special Conditions
- Mechanical Dimension
- Options and Accessories
- Analog I/O option MCB 109
- How to Order
- Type Code String
- Ordering Numbers
- How to Install
- Electrical Installation
- Final Set-Up and Test
- Safe Stop Installation
- Additional Connections
- Installation of misc. connections
- Safety
- EMC-correct Installation
- Residual Current Device
- Application Examples
- Potentiometer Reference
- SLC Application Example
- System Status and Operation
- Cascade Controller Wiring Diagram
- Lead Pump Alternation Wiring Diagram
- Master/Follower Operation Application
- RS-485 Installation and Set-up
- FC Protocol Overview
- Network Configuration
- Examples
- VLT AQUA with Modbus RTU
- How to Access Parameters
- Danfoss FC Control Profile
- Troubleshooting
- Fault messages
- Index

vlt aqua
Table of contents
- Table Of Contents
- Table Of Contents
- Introduction
- Application Types
- Master-Follower Configuration
- Mixed Pump Configuration
- Mixed Pump Configuration with Alternation
- Sleep Mode
- Basic Cascade Controller
- Installation
- Advanced Cascade Controller MCO 102
- Configuring the System
- Closed Loop Control
- Operation
- Runtime Balancing
- Staging/De-staging in Mixed Pump Configurations
- Flow Compensation for Applications with Cascade Controller
- Parameter Descriptions
- Cascade CTL Option, 27
- Parameter Lists
- Cascade CTL Option
- Configuration Examples
- Follower Drive Settings
- Index

vlt aqua
Table of contents
- Table Of Contents
- MG.20.P3.02 - VLT ® is a registered Danfoss trademark
- How to Read these Operating Instructions
- Approvals
- Safety
- General Warning
- Avoid unintended start
- Safe Stop of the Frequency Converter
- IT mains
- How to Install
- Receiving the Frequency Converter
- Lifting
- Mechanical Dimensions
- Rated Power
- Mechanical Installation
- Terminal locations - frame size D
- Terminal Locations - frame size E
- Terminal Locations - frame size F
- Cooling and Airflow
- Field Installation of Options
- Outside installation/ NEMA 3R kit for Rittal enclosures
- Installation on pedestal
- Input plate option
- Installation of Mains Shield for frequency converters
- Electrical Installation
- Mains connection
- Fuses
- Motor Insulation
- Control cable routing
- Electrical Installation, Control Terminals
- Connection Examples
- Electrical Installation - additional
- Switches S201, S202, and S801
- Final Set-up and Test
- Additional Connections
- How to operate the frequency converter
- How to operate numeric LCP (NLCP)
- Tips and tricks
- How to programme the frequency converter
- Q1 My Personal Menu
- Q5 Changes Made
- Q6 Loggings
- Main Menu
- Commonly Used Parameters - Explanations
- Parameter Options
- General Specifications
- Troubleshooting
- Fault messages
- Index
- Digital In/Out 5
- Profibus 9

vlt aqua
Table of contents
- Table Of Contents
- Table Of Contents
- How to Read these Operating Instructions
- Symbols
- Safety
- General Warning
- Avoid unintended start
- Safe Stop Installation
- IT Mains
- Introduction to the Low Harmonic Drive
- Ordering Form Type Code
- How to Install
- Pre-installation
- Lifting
- Mechanical Dimensions
- Mechanical Installation
- Assembly of F Frame Sections
- Control Wire Connection between Drive and Filter
- Terminal Locations - Frame size D
- Terminal Locations - Frame size E
- Terminal Locations - Frame size F
- Cooling and Airflow
- Field Installation of Options
- Electrical Installation
- Mains Connection
- Fuses
- Control Cable Routing
- Connection Examples for Control of Motor with External Signal Provider
- Electrical Installation - additional
- Switches S201, S202, and S801
- Final Set-up and Test
- Additional Connections
- Motor Thermal Protection
- How to Operate the Low Harmonic Drive
- Tips and tricks
- How to Programme the Low Harmonic Drive
- How to Programme the Active Filter
- VLT AQUA Drive - Description of Common Parameters
- Parameter Options
- Operation/Display 0
- Load/Motor 1
- Brakes 2
- Limits / Warnings 4
- Digital In/Out 5
- Analog In/Out 6
- Comm. and Options 8
- Profibus 9
- Smart Logic 13
- FC Information 15
- Data Readouts 16
- Data Readouts 2 18
- FC Closed Loop 20
- Ext. Closed Loop 21
- Application Functions 22
- Timed Actions 23
- Cascade Controller 25
- Analog I/O Option MCB 109 26
- Water Application Functions 29
- Parameter Options - Filter
- Special Functions 14
- AF Readouts301
- RS-485 Installation and Set-up
- Network Configuration
- Examples
- How to Access Parameters
- General Specifications
- Troubleshooting
- Alarms and Warnings - Filter (left LCP)

vlt aqua
Table of contents
- Table Of Contents
- How to Read this Design Guide
- Approvals
- Abbreviations
- Introduction to VLT AQUA Drive
- CE labelling
- Air humidity
- VLT AQUA Controls
- General aspects of EMC
- Immunity Requirements
- Galvanic isolation (PELV)
- Earth leakage current
- Control with brake function
- Mechanical brake control
- Safe Stop Operation (optional)
- VLT AQUA Selection
- Efficiency
- Special Conditions
- Options and Accessories
- General Description
- How to Order
- Type Code String
- Ordering Numbers
- How to Install
- Electrical Installation
- Final Set-Up and Test
- Safe Stop Installation
- Safe Stop Commissioning Test
- Brake Connection Option
- Relay Connection
- Installation of misc. connections
- Safety
- EMC-correct Installation
- Residual Current Device
- Application Examples
- Potentiometer Reference
- SLC Application Example
- System Status and Operation
- Fixed Variable Speed Pump Wiring Diagram
- Lead Pump Alternation Wiring Diagram
- Submersible Pump Application
- Master/Follower Operation Application
- RS-485 Installation and Set-up
- FC Protocol Overview
- Network Configuration
- Examples
- Modbus RTU Overview
- How to Access Parameters
- Danfoss FC Control Profile
- Troubleshooting
- Index

vlt aqua
Table of contents
- Table Of Contents
- Table Of Contents
- How to Read the Instruction Manual
- Symbols
- Safety
- General Warning
- Avoid unintended start
- Safe Stop of the Adjustable Frequency Drive
- IT Line Power
- Introduction to the Low Harmonic Drive
- IEEE519 Compliance
- Ordering Form Type Code
- How to Install
- Pre-installation
- Lifting
- Mechanical Dimensions
- Mechanical Installation
- Assembly of F Frame Sections
- Control Wire Connection between Drive and Filter
- Terminal Locations - Frame size D
- Terminal Locations - Frame size E
- Terminal Locations - Frame size F
- Cooling and Airflow
- Field Installation of Options
- Frame size F Panel Options
- Electrical Installation
- AC line input connections
- Power and Control Wiring for Non-shielded Cables
- Fuses
- Control Cable Routing
- Electrical Installation, Control Terminals
- Connection Examples for Control of Motor with External Signal Provider
- Pulse Start/Stop
- Electrical Installation - additional
- Switches S201, S202, and S801
- Final Set-up and Test
- Additional Connections
- Motor Thermal Protection
- How to Operate the Low Harmonic Drive
- Tips and tricks
- How to Program the Low Harmonic Drive
- How to Program the Active Filter
- VLT AQUA Drive - Description of Common Parameters
- Index
- Operation and Display
- Load / Motor
- Brakes
- Limits / Warnings
- Digital In / Out
- Analog In / Out
- Communication and Options
- Profibus
- Special Functions
- FC Information
- Data Readouts
- Info & Readouts
- Ext. Closed-loop
- Application Functions
- Time-based Funtions
- Cascade Controller
- Analog I / O Option MCB 109
- Parameter Options - Filter
- Digital In/Out 5-**
- Special Functions 14-**
- FC Information 15-**
- Data Readouts 16-**
- AF Readouts301-**
- RS-485 Installation and Set-up
- Network Configuration
- Examples
- How to Access Parameters
- Troubleshooting
- Alarms and Warnings - Filter (left LCP)

vlt aqua
Table of contents
- Table Of Contents
- How to Read this Design Guide
- Approvals
- Abbreviations
- Introduction to the VLT AQUA Drive
- Disposal Instructions
- CE labeling
- Air humidity
- Vibration and shock
- VLT AQUA Controls
- General aspects of EMC
- Galvanic isolation (PELV)
- Ground leakage current
- Mechanical brake control
- Safe Stop Operation
- VLT AQUA Selection
- Line Supply 3 x 380-480 V AC
- Efficiency
- Special Conditions
- Automatic adaptations to ensure performance
- Mechanical Dimension
- Options and Accessories
- Analog I/O option MCB 109
- How to Order
- Type Code String
- Ordering Numbers
- How to Install
- Electrical Installation
- Access to Control Terminals
- Electrical Installation, Control Terminals
- Final Set-Up and Test
- Safe Stop Installation
- Safe Stop Commissioning Test
- Installation of misc. connections
- Safety
- EMC-correct Installation
- Residual Current Device
- Application Examples
- RS-485 Installation and Set-up
- FC Protocol Overview
- Network Configuration
- Examples
- Modbus RTU Overview
- VLT AQUA with Modbus RTU
- How to Access Parameters
- Danfoss FC Control Profile
- Troubleshooting
- Index

vlt aqua
Table of contents
- Table Of Contents
- How to Read these Operating Instructions
- Symbols
- Safety
- General Warning
- Avoid unintended Start
- Safe Stop of the Frequency Converter
- IT Mains
- How to Install
- Receiving the Frequency Converter
- Mechanical Dimensions
- General Considerations
- Installation in Enclosures - IP00 / Chassis units
- Floor Mounting - Pedestal Installation IP21 (NEMA1) and IP54 (NEMA12)
- Gland/Conduit Entry - IP21 (NEMA 1) and IP54 (NEMA12)
- IP21 Drip shield installation (D1 and D2 enclosure)
- Installation on pedestal
- Electrical Installation
- Power Connections
- Mains connection
- Fuses
- Electrical Installation, Control Terminals
- Connection Examples
- Speed Up/Down
- Electrical Installation - continued
- Switches S201, S202, and S801
- Final Set-up and Test
- Additional Connections
- How to programme the frequency converter
- Initialisation to Default Settings
- Parameter Options
- Digital In/Out

vlt aqua
Table of contents
- Table Of Contents
- How to Programme
- Quick Transfer of Parameter Settings between Multiple Frequency Converters
- Display Mode - Selection of Displayed Variables
- Changing Data
- How to operate numeric LCP (NLCP)
- Initialisation to Default Settings
- Parameter Description
- Main Menu - Operation and Display - Group 0
- Main Menu - Load and Motor - Group 1
- Main Menu - Brakes - Group 2
- Main Menu - Reference/Ramps - Group 3
- Main Menu - Limits/Warnings - Group 4
- Main Menu - Digital In/Out - Group 5
- Main Menu - Analog In/Out - Group 6
- Main Menu - Communications and Options - Group 8
- Main Menu - Profibus - Group 9
- Main Menu - CAN Fieldbus - Group 10
- Main Menu - Smart Logic - Group 13
- Main Menu - Special Functions -Group 14
- Main Menu - Frequency Converter Information - Group 15
- Main Menu - Data Readouts - Group 16
- Main Menu - Data Readouts 2 - Group 18
- Main Menu - FC Closed Loop - Group 20
- Main Menu - Extended Closed Loop - Group 21
- Main Menu - Application Functions - Group 22
- Main Menu - Time-based Functions - Group 23
- Main Menu - Cascade Controller - Group 25
- Main Menu - Analog I/O Option MCB 109 - Group 26
- Main menu – Water application – Group 29
- Main Menu - Bypass Option - Group 31
- Parameter Lists
- Load/Motor
- Brakes
- Profibus
- Special Functions
- Timed Actions

vlt aqua
Table of contents
- Table Of Contents
- Table Of Contents
- How to Read this Instruction Manual
- Symbols
- Safety
- General Warning
- Avoid unintended Start
- Safe Stop Installation
- Safe Stop of the Adjustable Frequency Drive
- IT Line Power
- How to Install
- Pre-installation
- Transportation and Unpacking
- Lifting
- Mechanical Dimensions
- Rated Power
- Mechanical Installation
- Terminal locations - frame size D
- Terminal Locations - frame size E
- Terminal Locations - frame size F
- Cooling and Airflow
- Field Installation of Options
- Outside installation/ NEMA 3R kit for Rittal enclosures
- Installation on pedestal
- Input plate option
- Installation of Line Power Shield for Adjustable Frequency Drives
- Frame size F Panel Options
- Electrical Installation
- AC line input connections
- Fuses
- Motor Insulation
- Motor Bearing Currents
- Control cable routing
- Electrical Installation, Control Terminals
- Connection Examples
- Electrical Installation - continued
- Switches S201, S202, and S801
- Final Set-up and Test
- Troubleshooting
- Additional Connections
- Motor Thermal Protection
- How to operate the adjustable frequency drive
- How to operate the numeric LCP (NLCP)
- Tips and tricks
- How to program the adjustable frequency drive
- Q1 My Personal Menu
- Q5 Changes Made
- Commonly Used Parameters - Explanations
- Parameter Options
- Operation/Display
- Load/Motor
- Reference / Ramps
- Limits / Warnings
- Digital In/Out
- Analog In/Out
- Comm. and Options
- Profibus
- Smart Logic
- FC Information
- Data Readouts
- Data Readouts 2
- Ext. Closed-loop
- Application Functions
- Timed Actions
- Cascade Controller
- Analog I/O Option MCB 109
- Cascade CTL Option 27-**
- Water Application Functions
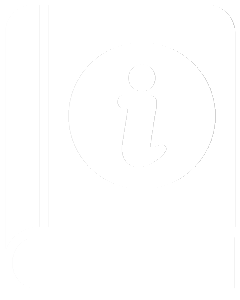
manualsdatabase
Your AI-powered manual search engine