ABB ACS850-04 series manuals

ACS850-04 series
Table of contents

ACS850-04 series
Table of contents
- List of related manuals
- Table Of Contents
- Table Of Contents
- Table Of Contents
- Table Of Contents
- Table Of Contents
- Table Of Contents
- Table Of Contents
- Table of contents
- What this chapter contains
- Safety in installation and maintenance
- Grounding
- Permanent magnet motor drives
- General safety
- Fiber optic cables
- Safe start-up and operation
- Categorization by option code
- Terms and abbreviations
- Product overview
- Alternative output busbar configurations
- Component placement
- Power connections and control interfaces
- Cables for connecting the control unit to the drive module and control panel
- Type designation label
- Planning the layout of the cabinet
- Layout examples, door open
- Arranging the grounding inside the cabinet
- Planning the cabinet placement on a cable channel
- Planning the grounding of the cable shields at the cabinet lead-through
- Preventing the recirculation of hot air
- Free space at top with high air inlet gratings in the cabinet door
- Free space at the side and front of the drive module
- Planning the placement of the control panel
- Checking the installation site
- Checking the delivery
- Fastening the cable lug terminals to the output busbars
- Fastening the drive module to the cabinet base
- Installing the drive control unit
- Vertical DIN rail mounting
- Horizontal DIN rail mounting
- Checking the compatibility of the motor and drive
- Requirements table
- Selecting the power cables
- Typical power cable sizes
- Typical power cable sizes (US)
- Alternative power cable types
- Conduit
- Signals in separate cables
- Diagram
- Continuous motor cable shield or enlosure for equipment in the motor cable
- Protecting the motor and motor cable in short-circuits
- Protecting the drive against ground faults
- Implementing the Power-loss ride-through function
- Using power factor compensation capacitors with the drive
- Implementing a bypass connection
- Protecting the contacts of relay outputs
- Connecting a motor temperature sensor to the drive I/O
- Brake resistor and resistor cable
- Connecting the power cables
- Input cable connection procedure
- Motor cable connection procedure
- DC connection
- Removing the cover assembly
- Fastening the control cable clamp plate
- Connecting the control unit to the drive module
- Connecting the control cables
- Default I/O connection diagram
- Jumpers
- External power supply for the JCU Control Unit (XPOW)
- Drive-to-drive link (XD2D)
- Safe torque off (XSTO)
- Routing the control cables
- Connecting a PC
- Groundings and protection
- Cooling and driven equipment
- Heatsink
- Replacing the cooling fan of the module
- Replacing the drive module
- Capacitors
- Replacing the capacitor pack
- Memory unit
- Ambient temperature derating
- Calculation example
- Fuse tables
- Quick guide for selecting between gG and aR fuses
- Dimensions, weights and free space requirements
- Losses, cooling data and noise
- Terminal and lead-through data for the power cables
- Brake resistor connection data
- Efficiency
- Ambient conditions
- Materials
- CE marking
- Category C3
- UL marking
- Frame size G with busbars on the left side (mm)
- Frame size G pedestal busbars on the long side (mm)
- Drive control unit (JCU)
- Package
- Dimension drawings (USA)
- Frame size G with busbars on the left side (inches)
- Frame size G pedestal busbars on the long side (inches)
- Example circuit diagram
- Placing the brake resistors
- Protecting the system in fault situations
- Minimizing electromagnetic interference
- Technical data
- Product and service inquiries

ACS850-04 series
Table of contents
- List of related manuals
- Table Of Contents
- Table Of Contents
- Table Of Contents
- Table Of Contents
- Table Of Contents
- Table Of Contents
- What this chapter contains
- Safety in installation and maintenance
- Grounding
- Permanent magnet motor drives
- General safety
- Fiber optic cables
- Printed circuit boards
- Categorization by option code
- Terms and abbreviations
- Layout
- Power connections and control interfaces
- External control unit connection cables
- Type designation key
- Layout examples, door closed
- Layout examples, door open
- Arranging the grounding inside the cabinet
- Planning the cabinet placement on a cable channel
- Planning the grounding of the cable shields at the cabinet lead-through
- Preventing the recirculation of hot air
- Free space at top with air inlet gratings in the cabinet door
- Planning the use of the cubicle heaters
- Protecting the motor insulation and bearings
- Requirements table
- Explosion-safe (EX) motors
- High-output motors and IP 23 motors
- Sine filters
- Typical power cable sizes
- Typical power cable sizes (US)
- Motor cable shield
- Selecting the control cables
- Separate control cable ducts
- Implementing thermal overload and short-circuit protection
- Protecting the drive and the input power and motor cables against thermal overload
- Implementing the Emergency stop function
- Implementing the ATEX-certified Safe motor disconnection function (option +Q971)
- Implementing a safety switch between the drive and motor
- Example bypass connection
- Switching the motor power supply from drive to direct-on-line
- Connecting a motor temperature sensor to the drive I/O
- Installation
- Safety
- Moving and unpacking the unit
- Checking the delivery
- Brake resistor and resistor cable
- Connecting the power cables
- Input cable connection procedure
- Motor cable connection procedure
- DC connection
- Mounting the drive module into the cabinet
- Assembly drawing of fastening the drive module to the cabinet
- Removing the protective covering from the module air outlet
- Removing the cover assembly of the external control unit
- Fastening the control cable clamp plate
- Mounting the external control unit
- Mounting the external control unit vertically on a DIN rail
- Installing optional modules
- Connecting the control cables to the terminals of the control unit
- Default I/O connection diagram
- Jumpers
- External power supply for the JCU Control Unit (XPOW)
- Drive-to-drive link (XD2D)
- Safe torque off (XSTO)
- Connecting a PC
- Cabinet
- Heatsink
- Fans
- Replacing the main cooling fans
- Replacing the drive module
- Capacitors
- Ambient temperature derating
- Dimensions, weights and free space requirements
- Units with optional common mode filter(+E208)
- Electrical power network specification
- Control unit (JCU-11) connection data
- Efficiency
- Materials
- CE marking
- Category C4
- Drive module dimensions
- Drive module dimensions with optional cabling panels (+H381)
- Cabling panels (option +H381) installed into a Rittal TS 8 cabinet
- Example circuit diagram
- Placing the brake resistors
- Protecting the system in fault situations
- Maximum cable length
- Technical data
- Dimensions and weights
- Product and service inquiries

ACS850-04 series
Table of contents
- What this chapter contains
- Installation and maintenance work
- Start-up and operation
- Table Of Contents
- Table Of Contents
- Table Of Contents
- Table Of Contents
- Table Of Contents
- Table of contents
- Contents
- Installation and commissioning flowchart
- Terms and abbreviations
- Product and service inquiries
- Power connections and control interfaces
- Main circuit and operation
- Type code
- Free space requirements
- Cooling and degrees of protection
- Preventing the recirculation of hot air
- Cabinet heaters
- Contents of the package
- Before installation
- Supply disconnecting device
- Operating time of the fuses and circuit breakers
- Safe Torque Off
- Selecting the power cables
- Alternative power cable types
- Protecting the relay output contacts and attenuating disturbances in case of inductive loads
- Relay cable
- Control cable ducts
- Electrical installation
- Checking the insulation of the assembly
- Connection to an IT (ungrounded) power system
- Frame size E: Disconnection of internal EMC filtering (option +E202 included)
- Power cable connection
- Procedure
- Grounding the motor cable shield at the motor end
- DC connection
- Installation of optional modules
- Connecting the control cables
- Jumpers
- DI6 (XDI:6) as a thermistor input
- Drive-to-drive link (XD2D)
- Grounding and routing the control cables
- Mounting the clamp plate
- Routing the control cables
- Checklist
- Heatsink
- Fan replacement (frame E)
- Additional cooling fan replacement (frame E0)
- Other maintenance actions
- Derating
- Dimensions, weights, noise
- AC input (supply) connection
- Efficiency
- Ambient conditions
- Materials
- CE marking
- Compliance with EN 61800-3 (2004), category C3
- UL marking
- Drive module, frame size E0
- Drive module, frame size E
- Chopper data / Resistor selection table
- Resistor installation and wiring
- Braking circuit commissioning
- Filter types
- Technical data

ACS850-04 series
Table of contents
- List of related manuals
- Table Of Contents
- Contents of this chapter
- Safety instructions
- Commissioning the drive for a motor in a hazardous area
- Exclusion of liability
- Two-channel connection to drive STO terminals
- Parameter settings
- Connection diagram
- Thermal motor protection with two-channel connection
- Connection diagram (two-channel connection)
- Wiring
- Markings of the drive/inverter module
- ATEX certificates
- Declaration of Conformity
- Product and service inquiries

ACS850-04 series
Table of contents
- ACS850 drive manuals
- Table Of Contents
- Table Of Contents
- Table Of Contents
- Table Of Contents
- Table Of Contents
- What this chapter contains
- Contents
- Installation
- Layout
- Status line
- Operating instructions
- List of tasks
- Help and panel version – Any mode
- Basic operations – Any mode
- Output mode
- Parameters
- Assistants
- Changed Parameters
- Fault Logger
- Time & Date
- Parameter Backup
- I/O Settings
- Reference Edit
- Drive Info
- Parameter Change Log
- Local control vs. external control
- External control
- Application macros
- Constant speeds
- Undervoltage control
- Brake chopper
- Emergency stop
- Fieldbus control
- Load analyzer
- Maintenance counters
- Mechanical brake control
- Process PID control
- Programmable analog inputs
- Programmable analog outputs
- External fault (parameter 30.01)
- Scalar motor control
- Thermal motor protection
- Settings
- User-definable load curve
- Factory macro
- Default control connections for the Factory macro
- Hand/Auto macro
- Default control connections for the Hand/Auto macro
- PID control macro
- Default control connections for the PID control macro
- Torque control macro
- Default control connections for the Torque control macro
- Sequential control macro
- Default control connections for the Sequential control macro
- Parameter listing
- I/O values
- Control values
- Appl values
- Drive status
- Alarms & faults
- System info
- Start/stop
- Start/stop mode
- Operating mode
- Analogue inputs
- Digital I/O
- Analogue outputs
- System
- Speed calculation
- Limits
- Speed ref
- Speed ref ramp
- Speed ctrl
- Torque ref
- Critical speed
- Process PID
- Fault functions
- Mot therm prot
- Automatic reset
- Supervision
- User load curve
- Process variable
- Timed functions
- Flux ref
- Motor control
- Mech brake ctrl
- Maintenance
- Energy optimising
- Voltage ctrl
- Data storage
- Fieldbus
- FBA settings
- FBA data out
- D2D communication
- Enc module sel
- Absol enc conf
- Resolver conf
- Hw configuration
- User motor par
- Start-up data
- Fieldbus addresses
- bit integer bit pointers
- Parameter groups 1...9
- Parameter groups 10...99
- How to reset
- Fault messages generated by the drive
- System overview
- Setting up communication through a fieldbus adapter module
- Drive control parameters
- The fieldbus control interface
- The Control Word and the Status Word
- Fieldbus references
- State diagram
- Product and service inquiries

ACS850-04 series
Table of contents
- List of related manuals
- Table Of Contents
- Table Of Contents
- Table Of Contents
- Table Of Contents
- Table Of Contents
- Table Of Contents
- Table Of Contents
- Table of contents
- What this chapter contains
- Safety in installation and maintenance
- Grounding
- Permanent magnet motor drives
- General safety
- Fiber optic cables
- Printed circuit boards
- Categorization by frame size and option code
- Terms and abbreviations
- Layout
- Power connections and control interfaces
- External control unit connection cables
- Type designation label
- Type designation key
- Layout examples, door closed
- Arranging the grounding inside the cabinet
- Planning the cabinet placement on a cable channel
- Planning the grounding of the cable shields at the cabinet lead-through
- Preventing the recirculation of hot air
- Required free space
- Planning the placement of the control panel
- Protecting the motor insulation and bearings
- Requirements table
- Additional requirements for explosion-safe (EX) motors
- Additional requirements for non-ABB high-output and IP23 motors
- Additional data for calculating the rise time and the peak line-to-line voltage
- Selecting the power cables
- Typical power cable sizes
- Alternative power cable types
- Additional US requirements
- Signals in separate cables
- Separate control cable ducts
- Continuous motor cable shield or enclosure for equipment in the motor cable
- Protecting the drive and the input power and motor cables against thermal overload
- Implementing the Emergency stop function
- Implementing a safety switch between the drive and motor
- Implementing a bypass connection
- Switching the motor power supply from drive to direct-on-line
- Connecting a motor temperature sensor to the drive I/O
- Safety
- Moving and unpacking the unit
- Checking the delivery
- Motor and motor cable
- Overall flowchart of the installation process
- Installing the mechanical accessories into the cabinet
- Assembly drawing (frame G1)
- Assembly drawing (frame G2)
- Assembly drawing (air baffles)
- Connecting the power cables
- Power cable connection procedure
- DC connection
- Mounting the drive module into the cabinet
- Mounting procedure
- Assembly drawing of installing the drive module to the cabinet (frame G1)
- Assembly drawing of installing the drive module to the cabinet (frame G2)
- Removing the protective covering from the module air outlet
- Removing the cover assembly of the external control unit
- Fastening the control cable clamp plate
- Mounting the external control unit
- Mounting the external control unit vertically on a DIN rail
- Installing optional modules
- Connecting the control cables to the terminals of the control unit
- Default I/O connection diagram
- Jumpers
- External power supply for the JCU control unit (XPOW)
- Drive-to-drive link (XD2D)
- Safe torque off (XSTO)
- Cabinet
- Heatsink
- Fans
- Replacing the main cooling fans
- Replacing the drive module
- Capacitors
- Derating
- Fuses (IEC)
- Dimensions, weights and free space requirements
- Losses, cooling data and noise
- Units without optional cabling panels (no +H381 or +H383)
- DC connection data
- Efficiency
- Ambient conditions
- Materials
- CE marking
- Category C3
- UL marking
- Disclaimer
- Frame G1 – Drive module dimensions
- Frame G1 – Drive module dimensions with optional cabling panels (+H381)
- Frame G1 – Cabling panels (+H383) installed into a Rittal TS 8 cabinet
- Frame G2 – Drive module dimensions
- Frame G2 – Drive module dimensions with optional cabling panels (+H381)
- Frame G2 – Cabling panels (+H383) installed into a Rittal TS 8 cabinet
- Frames G1 and G2 – Bottom plate
- Frames G1 and G2 – Air baffles
- Example circuit diagram
- Placing the brake resistors
- Protecting the system in fault situations
- Maximum cable length
- Technical data
- Dimensions and weights
- Product and service inquiries

ACS850-04 series
Table of contents
- List of related manuals
- What this chapter contains
- Installation and maintenance work
- Start-up and operation
- Table Of Contents
- Table Of Contents
- Table Of Contents
- Table Of Contents
- Table Of Contents
- Table Of Contents
- Installation and commissioning flowchart
- Terms and abbreviations
- Motor control
- Layout
- Power connections and control interfaces
- Type designation label
- Type designation key
- Main dimensions and free space requirements
- Cooling and degrees of protection
- Preventing the recirculation of hot air
- Cabinets with multiple modules
- Cabinet heaters
- Contents of the package
- Delivery check and drive module identification
- Installation procedure
- Mains choke installation
- Thermal overload and short circuit protection
- Motor thermal protection
- Safe torque off function
- Alternative power cable types
- Motor cable shield
- Considering the PELV requirements at sites above 2000 m (6562 ft)
- Selecting the control cables
- Control cable ducts
- Checking the insulation of the assembly
- Power cable connection
- Procedure
- Grounding the motor cable shield at the motor end
- Installation of power cable clamp plates
- Power cable connection – frame size A
- Power cable connection – frame size B
- Power cable connection – frame sizes C and D (connector covers removed)
- DC connection
- Installation of optional modules
- Connecting the control cables
- Jumpers
- DI6 (XDI:6) as a thermistor input
- Drive-to-drive link (XD2D)
- Safe torque off (XSTO)
- Heatsink
- Cooling fan
- Fan replacement (Frames C and D)
- Reforming the capacitors
- Nominal ratings with 400 V AC supply
- Nominal ratings with 500 V AC supply
- Ambient temperature derating
- Deratings with 400 V AC supply in low motor noise mode
- Deratings with 500 V AC supply in low motor noise mode
- Cooling characteristics, noise levels
- Supply cable fuses
- AC input (supply) connection
- Motor connection
- Efficiency
- Ambient conditions
- Applicable standards
- CE marking
- Compliance with EN 61800-3:2004
- Second environment (drive of category C3)
- UL marking
- Installation guidelines
- Selection table
- JFI-A1/JFI-B1 (Frame A/B, category C3) installation
- Mounting procedures
- JFI-B1
- JFI-0x (Frames A...D, category C2) installation
- Additional requirements for the braking applications
- Technical data
- Chopper data table
- Resistor selection table
- Resistor installation and wiring
- Frame size A
- Frame size B
- Frame size C
- Frame size D
- Mains chokes (type CHK-0x)
- EMC filters (type JFI-x1)
- EMC filters (type JFI-0x)
- Brake resistors (type JBR-xx)
- Product and service inquiries
Related products
ACS850 seriesACSM1-04 SeriesACL30-04 SeriesACS880 SeriesACS880-01 SeriesACSM1 SeriesACS580 SeriesACS380 SeriesACH550 seriesACS 800 SeriesABB categories
Industrial Equipment
DC Drives
Controller
Relays
Measuring Instruments
Circuit breakers
Battery Charger
Industrial Electrical
Transformer
Switch
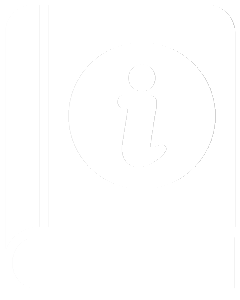
manualsdatabase
Your AI-powered manual search engine