ABB IRC5 Compact manuals

IRC5 Compact
Table of contents

IRC5 Compact
Table of contents
- Table Of Contents
- Table Of Contents
- Table Of Contents
- Overview
- Product documentation, M2004
- Safety
- General safety information
- General Information
- Safety risks
- Safety actions
- Safety stops
- What is an emergency stop
- What is a safety stop
- What is safeguarding
- Safety related instructions
- DANGER - Make sure that the main power has been switched off
- WARNING - The unit is sensitive to ESD
- Controller
- CAUTION - Hot components in controller
- Installation and Commissioning, IRC5
- Installation Activities
- Transporting and handling
- On-site Installation
- Connections
- Connecting power supply to the IRC5 Panel Mounted Controller
- Connecting fan unit to IRC5 Panel Mounted Drive Module
- Connecting a FlexPendant
- Connecting a PC to the service port
- Connection to serial channel connector
- The MOTORS ON/MOTORS OFF circuit
- Connection of external safety relay
- Connection of Drive Module Disconnect, by limit switch
- Connecting a Limit switch override push button
- Drive system
- Configuration of the drive system, IRC5
- Memory functions
- Connecting a USB memory to the computer unit
- I/O system
- Installation of add-ons
- Installation of additional Drive Module
- Installation of external operator's panel, IRC5
- Installation of I/O, Gateways and encoder interface units, IRC5
- Maintenance activities, controller IRC5
- Inspection activities
- Changing/replacing activities
- Cleaning activities
- Cleaning the FlexPendant
- Repair activities, controller IRC5
- Replacement of panel board
- Replacement of power supply
- Replacement of customer I/O power supply, IRC5
- Replacement of drive system power supply
- Replacement of I/O units and Gateways
- Replacement of backup energy bank
- Replacement of computer unit DSQC639
- Replacement of motherboard in computer unit DSQC639
- Replacement of DDR SDRAM memory on motherboard in computer unit DSQC639
- Replacement of PCI boards in the computer unit DSQC639
- Replacement of fieldbus adapter in the computer unit DSQC639
- Replacement of fan in computer unit DSQC639
- Replacement of Compact Flash memory in computer unit DSQC639
- Replacement of servo drive units and rectifier
- Replacement of Axis computer
- Replacement of Contactor Interface Board
- Replacement of drive system fans
- Replacement of transformer unit
- Replacement of brake resistor bleeder
- Reference information, IRC5
- Unit conversion
- Screw joints
- Weight specifications
- Standard toolkit, IRC5
- Document references
- Spare Parts
- Manipulator cables
- Position switch cables
- Customer signal, CS/CP and CS
- Customer power-signal
- Circuit Diagram

IRC5 Compact
Table of contents
- Table Of Contents
- Table Of Contents
- Table Of Contents
- Overview
- Product documentation, M2004
- Safety
- General safety information
- General Information
- Safety risks
- Safety actions
- Safety stops
- What is an emergency stop
- What is a safety stop
- What is safeguarding
- Safety related instructions
- DANGER - Make sure that the main power has been switched off
- WARNING - The unit is sensitive to ESD
- CAUTION - Never stand on or use the cabinet as a ladder
- DSQC639
- CAUTION - Close the cabinet door
- CAUTION - Hot components in controller
- Installation and Commissioning, IRC5
- Installation Activities
- Transporting and handling
- Unpacking, IRC5 Controller
- On-site Installation
- Bolting down the controller
- Transportation screws
- Mounting the FlexPendant holder
- Connections
- Connecting a FlexPendant
- Connecting a PC to the service port
- Connection to serial channel connector
- Connecting power supply to the Single Cabinet Controller
- Connecting power supply to the Dual Cabinet Controller
- Connecting the communication cabling for the Dual Cabinet Controller
- Fitting the connector
- Connecting the manipulator to the IRC5 controller
- The MOTORS ON/MOTORS OFF circuit
- Connection of external safety relay
- Connection to MOTORS ON/MOTORS OFF contactor
- Connection of Drive Module Disconnect, by limit switch
- Connection of servo disconnect, by servo power switch
- Connecting a Limit switch override push button
- Drive system
- Configuration of the drive system, IRC5
- Memory functions
- Connecting a USB memory to the computer unit
- I/O system
- Installation of add-ons
- Installation of external operator's panel, IRC5
- Installation of Drive system parts
- Installation of I/O, Gateways and encoder interface units, IRC5
- Installation of PMC-card for Force Control Function
- Installation of extra mass memory in computer unit DSQC623
- Installation of Euromap and SPI
- Upgrading and installation of 2X Euromap interface (Option 671-4)
- Installation of cooling fan harness axis 1 and 2
- Installation of Hot plug
- Installing the EPS board DSQC 646 for Electronic Position Switches
- Installing the SafeMove board DSQC 647
- Installation of Remote Service
- Maintenance activities, controller IRC5
- Inspection activities
- Changing/replacing activities
- Replacement of moist dust filter
- Cleaning activities
- Cleaning moist dust filter
- Cleaning the FlexPendant
- Repair activities, controller IRC5
- Replacement of panel board
- Replacement of power supply
- Replacement of power distribution board
- Replacement of customer I/O power supply, IRC5
- Replacement of customer I/O power supply
- Replacement of drive system power supply
- Replacement of system power supply
- Replacement of Flange disconnect
- Replacement of I/O units and Gateways
- Replacement of backup energy bank
- Replacement of control system fan
- Replacement of heat exchange unit and fan
- Replacement of computer unit DSQC623
- Replacement of computer unit DSQC639
- Replacement of motherboard in computer unit DSQC623
- Replacement of motherboard in computer unit DSQC639
- Replacement of DDR SDRAM memory on motherboard in computer unit DSQC639
- Replacement of PCI cards in the computer unit DSQC623
- Replacement of PCI boards in the computer unit DSQC639
- Replacement of fieldbus adapter in the computer unit DSQC639
- Replacement of fan in computer unit DSQC623
- Replacement of fan in computer unit DSQC639
- Replacement of hard disk or IDE Flash module and cable in computer unit DSQC623
- Replacement of Compact Flash memory in computer unit DSQC639
- Replacement of computer power supply in computer unit DSQC623
- Replacement of servo drive units, rectifierand capacitorunit
- Replacement of Axis computer
- Replacement of EPS board DSQC 646
- Replacement of SafeMove board DSQC 647
- Replacement of Remote Service box
- Replacement of Contactor Interface Board
- Replacement of drive system fans
- Replacement of transformer unit
- Replacement of brake resistor bleeder
- Reference information, IRC5
- Unit conversion
- Screw joints
- Weight specifications
- Standard toolkit, IRC5
- Document references
- Lifting equipment and lifting instructions
- Spare Parts
- Manipulator cables
- Position switch cables
- Fan cables
- CP/CS Harness IRB 6400RF
- CP/CS Harness IRB 6600, 7600, 660, 6620 and 6640
- Customer signal, CS/CP and CS
- Customer power-signal
- External axis cables
- Circuit Diagram

IRC5 Compact
Table of contents
- Table Of Contents
- Table Of Contents
- Overview of this manual
- Product documentation, M2004
- Safety
- Safety in the manipulator system
- Safety risks
- Risks associated with live electric parts
- Safety actions
- Safety stops
- What is an emergency stop
- What is a safety stop
- What is safeguarding
- Safety related instructions
- Safety signals in the manual
- DANGER - Make sure that the main power has been switched off
- WARNING - The unit is sensitive to ESD
- CAUTION - Never stand on or use the cabinet as a ladder
- CAUTION - Make sure that there are no loose screws or turnings
- CAUTION - Close the cabinet door
- CAUTION - Hot components in controller
- Installation and commissioning
- Unpacking the controller
- On-site installation
- Mounting the FlexPendant holder
- Vertical mounting
- Buttons and switches
- Brake release button
- Connections
- Connectors on the IRC5 Compact controller
- Connecting a FlexPendant
- Connecting a PC to the service port
- Connection to serial channel
- Connecting power supply
- Fitting the connector
- Connecting the manipulator to the IRC5 Compact controller
- Descriptions for contacts XS7, XS9, XS10, XS11, XS12 and XS13
- The MOTORS ON/MOTORS OFF circuit
- Emergency stop output
- Opening the IRC5 Compact controller
- Accessing the controller parts
- Drive system
- Connecting a USB memory
- I/O system
- Installation of add-ons
- Installation of external operator's panel
- Installation of I/O, gateways and encoder interface units outside IRC5 Compact
- Installation of Remote Service antenna
- Installation of external terminal blocks
- Maintenance
- Changing/replacing activities
- Activities
- Cleaning the FlexPendant
- Repair
- Replacement of safety board
- Replacement of I/O unit
- Replacement of backup energy bank
- Replacement of motherboard
- Replacement of DDR SDRAM memory on motherboard
- Replacement of DeviceNet Lean board
- Replacement of PCI boards
- Replacement of fieldbus adapter
- Replacement of Compact Flash memory
- Replacement of drive unit
- Replacement of axis computer DSQC 668
- Replacement of system fans
- Replacement of brake resistor bleeder
- Replacement of Remote Service box
- Replacement of power supply
- Replacement of power distribution board
- Replacement of system power supply
- Replacement of line filter
- Decommissioning
- Introduction
- Reference information
- Applicable safety standards
- Unit conversion
- Screw joints
- Spare parts
- Manipulator cables
- Circuit diagrams
- Index

IRC5 Compact
Table of contents
- Table Of Contents
- Table Of Contents
- Table Of Contents
- Overview of this manual
- Product documentation
- Network security
- Safety
- Safety data
- Protective stop and emergency stop
- Safety actions
- Make sure that the main power has been switched off
- Enabling device and hold-to-run functionality
- Recover from emergency stops
- Safety during troubleshooting
- Safety risks
- Risks associated with live electric parts
- The unit is sensitive to ESD
- Close the cabinet door
- Hot components in controller
- Make sure that all mode selector keys are kept safe
- Risk of disabling function "Reduced speed 250 mm/s
- Safety signals and symbols
- Safety symbols on controller labels
- Installation and commissioning
- Installation activities
- Transporting and handling
- Unpacking the controller
- On-site installation
- Bolting down the controller
- Transportation screws
- Mounting the FlexPendant holder
- Connections
- Connecting cables to the controller
- Power supply system requirements
- Connecting power supply to the controller
- Connecting the manipulator to the controller
- Connecting safety signals
- Connecting a FlexPendant
- Using the hot plug option
- Connectors on the computer unit
- Connecting a serial channel to the controller
- Programmable stop functions
- The MOTORS ON/MOTORS OFF circuit
- Connection of external safety relay
- Connection to MOTORS ON/MOTORS OFF contactor
- Connection of drive module
- Connection of Drive Module Disconnect, by limit switch
- Connection of servo disconnect, by servo power switch
- Connecting a Limit switch override push button
- Drive system
- Configuration of the drive system
- Memory functions
- Connecting a USB memory
- I/O system
- Local I/O devices
- DeviceNet I/O units
- Installation of add-ons
- Installation of external enabling device
- Installation of Local I/O devices
- Installation of DeviceNet I/O, Gateways and encoder interface units, IRC5
- Installation of cooling fan harness axis 1 and 2
- Installation of the option Hot plug
- Installing the EPS board DSQC 646 for Electronic Position Switches
- Installing the SafeMove board DSQC 647
- Installing the Safety module DSQC1015 for SafeMove
- Installation of DispensePac support
- Installation of additional drive units
- Installation of additional Drive Module
- Process module
- Installation of drive system fans with temperature sensors
- Testing
- Maintenance
- Inspection activities
- Changing/replacing activities
- Cleaning activities
- Cleaning moist dust filter
- Cleaning the FlexPendant
- Function tests
- Function test of emergency stop
- Function test of mode switch
- Function test of three-position enabling device
- Function test of motor contactors K42 and K43
- Function test of brake contactor K44
- Function test of auto stop
- Function test of general stop
- Function test of superior stop
- Function test of limit switch
- Function test of automatic fuse F1
- Function test of reduced speed control
- Repair
- Replacement of panel board
- Replacement of Flange disconnect
- Replacement of I/O units and Gateways
- Replacement of backup energy bank
- Replacement of heat exchange unit and fan
- Replacement of computer unit
- Replacement of PCIexpress boards in the computer unit
- Replacement of expansion board in the computer unit
- Replacement of fieldbus adapter in the computer unit
- Replacement of fan in computer unit
- Replacement of SD-card memory in computer unit
- Replacement of drive units
- Replacement of Axis computer
- Replacement of EPS board DSQC 646 for Electronic Position Switches
- Replacement of SafeMove board DSQC 647
- Replacement of Safety module DSQC1015 for SafeMove
- Replacement of Remote Service box
- Replacement of Contactor Interface Board
- Replacement of drive system fans
- Replacement of sensors for the drive system fans
- Replacement of transformer unit
- Replacement of brake resistor bleeder
- Replacement of Process Interface Board
- Replacement of Ethernet switch
- Replacement of power supply
- Replacement of customer I/O power supply
- Replacement of system power supply
- Decommissioning
- Environmental information
- Reference information
- Applicable standards
- Unit conversion
- Screw joints
- Weight specifications
- Standard toolkit, IRC5
- Lifting accessories and lifting instructions
- Spare parts
- FlexPendant parts
- Manipulator cables
- Fan cables
- CP/CS Harness
- Cables customer power/customer signal
- Other customer cables
- Additional cables
- Circuit diagrams
- Index

IRC5 Compact
Table of contents
- Table Of Contents
- Table Of Contents
- Description
- Principle layout
- Terms and concepts
- Safety instructions
- Unpacking and handling safety
- Commissioning safety
- Technical specifications and requirements
- Dimensions
- Width and height measurements
- Technical requirements for the robot
- Variants and options
- Zone division
- Ordering list
- Unpacking and handling
- Mechanical installation
- Maintenance intervals
- Maintenance instructions

IRC5 Compact
Table of contents
- Table Of Contents
- Table Of Contents
- Table Of Contents
- Table Of Contents
- Overview of this manual
- Product documentation, M2000/M2000A
- Product documentation, IRC5
- How to read the product manual
- Safety
- Protective stop and emergency stop
- Safety actions
- Emergency release of the robot axes
- Make sure that the main power has been switched off
- Safety risks
- Moving robots are potentially lethal
- First test run may cause injury or damage
- Work inside the working range of the robot
- Enabling device and hold-to-run functionality
- Risks associated with live electric parts
- The unit is sensitive to ESD
- Hot parts may cause burns
- Safety risks related to pneumatic/hydraulic systems
- Brake testing
- Safety risks during handling of batteries
- Safety risks during work with gearbox lubricants (oil or grease)
- Safety signals and symbols
- Safety symbols on product labels
- Installation and commissioning
- Unpacking
- Working range and type of motion
- Risk of tipping/stability
- On-site installation
- Lifting robot with roundslings
- Lifting robot with lifting slings
- Manually releasing the brakes
- Lifting the base plate
- Securing the base plate
- Orienting and securing the robot
- Fitting equipment on robot
- Signal lamp (option)
- Installation of base spacers (option)
- Installation of cooling fan for motors (option)
- Installation of Foundry Plus Cable guard (option no. 908-1)
- Loads fitted to the robot, stopping time and braking distances
- Restricting the working range
- Mechanically restricting the working range of axis 1
- Extended working range, axis 1 (option 561-1)
- Mechanically restricting the working range of axis 2
- Mechanically restricting the working range of axis 3
- Installation of position switches (option)
- electrical connections
- Start of robot in cold environments
- Maintenance
- Maintenance schedule and expected component life
- Maintenance schedule
- Expected component life
- Inspection activities
- Inspecting the oil level in axis-1 gearbox
- Inspecting the oil level in axis-2 gearbox
- Inspecting the oil level in axis-3 gearbox
- Inspecting the oil level in axis-4 gearbox
- Inspecting the oil level in axis-5 gearbox
- Inspecting the oil level in axis-6 gearbox
- Inspecting the balancing device
- Inspecting the cable harness
- Inspecting the information labels
- Inspecting the axis-1 mechanical stop pin
- Inspecting the additional mechanical stops
- Inspecting the damper on axes 2-5
- Inspection, position switch axes 1, 2 and 3
- Inspecting, signal lamp
- Replacement/changing activities
- Changing oil, axis-1 gearbox
- Changing oil, axis-2 gearbox
- Changing oil, axis-3 gearbox
- Changing oil, axis-4 gearbox
- Changing oil, axis-5 gearbox
- Changing oil, axis-6 gearbox
- Replacing the SMB battery
- Lubrication activities
- Cleaning activities
- Service Information System, M2000
- Description of Service Information System (SIS)
- SIS system parameters
- Setting the SIS parameters
- Reading the SIS output logs
- Exporting the SIS data
- Repair
- General procedures
- Mounting instructions for bearings
- Mounting instructions for seals
- Cut the paint or surface on the robot before replacing parts
- The brake release buttons may be jammed after service work
- Complete robot
- Replacement of cable harness, axes 1-4
- Replacement of cable harness, axes 5-6
- Replacement of cabling, axis 5 motor
- Replacement of complete arm system
- Upper and lower arm
- Replacement of complete wrist unit
- Replacement of upper arm
- Replacement of complete lower arm
- Replacement of lower arm shaft
- Securing the lower arm
- Frame and base
- Replacing the brake release board
- Replacement of spherical roller bearing, balancing device
- Replacement of balancing device
- Unloading the balancing device using hydraulic press tool
- Restoring the balancing device using a hydraulic press tool
- Motors
- Replacement of motor axis 2
- Replacement of motor, axis 3
- Replacement of motor, axis 4
- Replacement of motor, axis 5
- Replacement of motor, axis 6
- Gearboxes
- Replacement of gearbox axis 2
- Replacement of gearbox, axis 3
- Replacement of gearbox, axis 6
- Calibration
- Calibration methods
- When to calibrate
- Synchronization marks and axis movement directions
- Calibration movement directions for all axes
- Updating revolution counters
- Calibrating with Axis Calibration method
- Calibration tools for Axis Calibration
- Installation locations for the calibration tools
- Axis Calibration - Running the calibration procedure
- Calibrating with Calibration Pendulum method
- Verifying the calibration
- Checking the synchronization position
- Decommissioning
- Scrapping of robot
- Decommissioning of balancing device
- Robot description
- Spare part lists
- Reference information
- Applicable standards
- Unit conversion
- Screw joints
- Weight specifications
- Standard tools
- Special tools
- Lifting accessories and lifting instructions
- Circuit diagram
- Circuit diagram 3HAC 025744-001
- Circuit diagram 3HAC 13347-1
- Index

IRC5 Compact
Table of contents
- Table Of Contents
- Table Of Contents
- Table Of Contents
- Overview of this manual
- HAC052852
- Product documentation
- How to read the product manual
- Safety
- Protective stop and emergency stop
- Safety actions
- Emergency release of the robot axes
- Make sure that the main power has been switched off
- Safety risks
- Moving robots are potentially lethal
- First test run may cause injury or damage
- Work inside the working range of the robot
- Enabling device and hold-to-run functionality
- Risks associated with live electric parts
- The unit is sensitive to ESD
- Hot parts may cause burns
- Safety risks related to pneumatic/hydraulic systems
- Brake testing
- Safety risks during handling of batteries
- Safety risks during work with gearbox lubricants (oil or grease)
- Safety signals and symbols
- Safety symbols on product labels
- Installation and commissioning
- Unpacking
- Working range
- Risk of tipping/stability
- Main dimensions
- On-site installation
- Attaching the robot and removing the fork lift accessory set
- Lifting the base plate
- Securing the base plate
- Lifting the robot with roundslings
- Returning of the ABB pallet
- Manually releasing the brakes
- Orienting and securing the robot
- Loads fitted to the robot, stopping time and braking distances
- Fitting equipment
- Restricting the working range
- Mechanically restricting the working range of axis 1
- electrical connections
- Installation of options
- Installing the motor cooling fans
- Start of robot in cold environments
- Maintenance
- Maintenance schedule and expected component life
- Maintenance schedule
- Expected component life
- Inspection activities
- Product manual - IRB
- Inspecting the oil level in axis-2 and 3 gearboxes
- Inspecting the oil level in axis-4 primary gearbox
- Inspecting the oil level in axis-4 secondary gearbox
- Inspecting the oil level in axis-5 gearbox
- Inspecting the oil level in axis-6 gearbox
- Inspecting the transparent plugs
- Inspecting the balancing devices
- Inspecting the cable harness
- Inspecting the information labels
- Inspecting the axis-1 mechanical stop pin
- Inspecting the additional mechanical stops
- Inspecting the fork lift accessories
- Inspecting the signal lamp (option)
- Inspecting dampers
- Replacement/changing activities
- Changing oil, axis-1 gearbox
- Changing oil in axis-2 and axis-3 gearbox
- Changing oil, axis-4 primary gearbox
- Changing oil, axis-4 secondary gearbox
- Changing oil, axis-5 gearbox
- Changing oil, axis-6 gearbox
- Replacing the SMB battery
- Lubrication activities
- Lubricating the cross roller bearing
- Cleaning activities
- Repair
- General procedures
- Mounting instructions for bearings
- Mounting instructions for seals
- Cut the paint or surface on the robot before replacing parts
- The brake release buttons may be jammed after service work
- Attaching lifting accessories
- Attaching lifting accessories to the wrist
- Cable harness
- Refitting the cable harness
- Replacing the SMB
- Replacing the brake release unit
- Upper and lower arms
- Replacing the wrist
- Replacing the axis-6 unit
- Replacing the turning disc
- Replacing the process turning disc
- Replacing the complete lower arm
- Replacing the parallel arm
- Frame and base
- Replacing the mechanical stop pin
- Replacing the parallel rod
- Unloading and restoring the balancing device
- Replacing the balancing devices
- Motors
- Replacing the axis-2 and axis-3 motors
- Replacing the axis-4 motor
- Replacing the axis-5 motor
- Replacing the axis-6 motor
- Gearboxes
- Replacing the axis-1 gearbox
- Replacing the axis-2 gearbox
- Replacing the axis-3 gearbox
- Replacing the axis-4 primary gearbox
- Replacing the axis-6 gearbox
- Calibration
- Calibration methods
- When to calibrate
- Synchronization marks and axis movement directions
- Calibration movement directions for all axes
- Updating revolution counters
- Calibrating with Axis Calibration method
- Calibration tools for Axis Calibration
- Installation locations for the calibration tools
- Axis Calibration - Running the calibration procedure
- Verifying the calibration
- Checking the synchronization position
- Decommissioning
- Scrapping of robot
- Decommissioning of balancing device
- Reference information
- Applicable standards
- Unit conversion
- Screw joints
- Weight specifications
- Standard toolkit
- Special tools
- Lifting accessories and lifting instructions
- Spare parts
- Circuit diagrams
- Index

IRC5 Compact
Table of contents
- Table Of Contents
- Table Of Contents
- Table Of Contents
- Overview of this manual
- Product documentation
- Network security
- Safety
- Safety data
- Protective stop and emergency stop
- Safety actions
- Make sure that the main power has been switched off
- Enabling device and hold-to-run functionality
- Recover from emergency stops
- Safety risks
- Risks associated with live electric parts
- The unit is sensitive to ESD
- Close the cabinet door
- Hot components in controller
- Make sure that all mode selector keys are kept safe
- Risk of disabling function "Reduced speed 250 mm/s
- Safety signals and symbols
- Safety symbols on controller labels
- Installation and commissioning
- Installation activities
- Transporting and handling
- On-site installation
- Installation, IRC5 Panel Mounted Controller
- Connections
- Connecting power supply to PMC small
- Connecting power supply to PMC large
- Connecting power supply to the control module
- Connecting communication cables between IRC5 Panel Mounted Drive Module and control module
- Connecting fan unit to IRC5 Panel Mounted Drive Module
- Connecting a FlexPendant
- Connectors on the computer unit
- Connecting a serial channel to the controller
- The MOTORS ON/MOTORS OFF circuit
- Programmable stop functions
- Connection of external safety relay
- Connection of Drive Module Disconnect, by limit switch
- Connecting a Limit switch override push button
- Drive system
- Memory functions
- Connecting a USB memory
- I/O system
- DeviceNet I/O units
- Installation of add-ons
- Installation of external operator's panel, IRC5
- Installation of external enabling device
- Installation of DeviceNet I/O, Gateways and encoder interface units, IRC5
- Installing the EPS board DSQC 646 for Electronic Position Switches
- Installing the SafeMove board DSQC 647
- Testing
- Maintenance
- Inspection activities
- Cleaning activities
- Cleaning the FlexPendant
- Function tests
- Function test of mode switch
- Function test of three-position enabling device
- Function test of motor contactors K42 and K43
- Function test of brake contactor K44
- Function test of auto stop
- Function test of general stop
- Function test of superior stop
- Function test of limit switch
- Function test of reduced speed control
- Repair
- Replacement of panel board
- Replacement of I/O units and Gateways
- Replacement of backup energy bank
- Replacement of computer unit
- Replacement of PCIexpress boards in the computer unit
- Replacement of expansion board in the computer unit
- Replacement of fieldbus adapter in the computer unit
- Replacement of fan in computer unit
- Replacement of SD-card memory in computer unit
- Replacement of drive unit for PMC small
- Replacement of Main Drive Unit for PMC large
- Replacement of Axis computer
- Replacement of EPS board DSQC 646 for Electronic Position Switches
- Replacement of SafeMove board DSQC 647
- Replacement of Contactor Interface Board
- Replacement of drive system fans
- Replacement of transformer unit
- Replacement of brake resistor bleeder for PMC small
- Replacement of brake resistor bleeder for PMC large
- Replacement of power supply
- Replacement of control power supply
- Replacement of drive system power supply
- Decommissioning
- Environmental information
- Reference information
- Applicable standards
- Unit conversion
- Screw joints
- Weight specifications
- Standard toolkit, IRC5
- Lifting accessories and lifting instructions
- Spare parts
- FlexPendant parts
- Manipulator cables
- Fan cables
- CP/CS Harness
- Cables customer power/customer signal
- Other customer cables
- Additional cables
- Circuit diagrams
- Index

IRC5 Compact
Table of contents
- Table Of Contents
- Table Of Contents
- Table Of Contents
- Table Of Contents
- Overview of this manual
- Circuit diagram
- Spare part lists
- Product manual, spare parts - IRB
- Product documentation, M2000/M2000A
- Product documentation, IRC5
- How to read the product manual
- Safety
- Protective stop and emergency stop
- Safety actions
- Emergency release of the robot axes
- Make sure that the main power has been switched off
- Safety risks
- Moving robots are potentially lethal
- First test run may cause injury or damage
- Work inside the working range of the robot
- Enabling device and hold-to-run functionality
- Risks associated with live electric parts
- The unit is sensitive to ESD
- Hot parts may cause burns
- Safety risks related to pneumatic/hydraulic systems
- Brake testing
- Safety risks during handling of batteries
- Safety risks during work with gearbox lubricants (oil or grease)
- Safety signals and symbols
- Safety symbols on product labels
- Installation and commissioning
- Robot transportation precautions
- Securing the robot with a transport support
- Unpacking
- Working range, IRB 7600 - 150/3.5
- Working range, IRB 7600 - 340/2.8
- Working range, IRB 7600 - 400/2.55, IRB 7600 - 500/2.55
- Working range, IRB 7600 - 500/2.3
- Risk of tipping/stability
- On-site installation
- Lifting robot with lifting slings
- Lifting robot with roundslings
- Manually releasing the brakes
- Lifting the base plate
- Securing the base plate
- Orienting and securing the robot
- Fitting equipment on robot
- Installation of base spacers (option)
- Extended working range, axis 1 (option 561-1)
- Installation of cooling fan for motors (option)
- Installation of Foundry Plus Cable guard (option no. 908-1)
- Loads fitted to the robot, stopping time and braking distances
- Signal lamp (option)
- Restricting the working range
- Mechanically restricting the working range of axis 1
- Mechanically restricting the working range of axis 2
- Mechanically restricting the working range of axis 3
- Installation of position switches (option)
- Electrical connections
- Start of robot in cold environments
- Maintenance
- Maintenance schedule and expected life
- Maintenance schedule
- Expected component life
- Inspection activities
- Inspecting the oil level in axis-1 gearbox
- Inspecting the oil level in axis-2 gearbox
- Inspecting the oil level in axis-3 gearbox
- Inspecting the oil level in axis-4 gearbox
- Inspecting the oil level in axis-5 gearbox
- Inspecting the oil level in axis-6 gearbox
- Inspecting the balancing device
- Inspecting the cable harness
- Inspecting the axis-1 mechanical stop pin
- Inspecting the mechanical stops on axes 1, 2, and 3
- Inspecting the damper on axes 2 to 5
- Inspecting the position switch on axes 1, 2, and 3
- Inspecting the information labels
- Inspecting the UL lamp
- Changing/replacement activities
- Changing oil, axis-1 gearbox
- Changing oil, axis-2 gearbox
- Changing oil, axis-3 gearbox
- Changing oil, axis-4 gearbox
- Changing oil, axis-5 gearbox
- Changing oil, axis-6 gearbox
- Replacing the SMB battery
- Lubrication activities
- Cleaning activities
- Cleaning the IRB 7600
- Service Information System, M2000
- Description of Service Information System (SIS)
- SIS system parameters
- Setting the SIS parameters
- Reading the SIS output logs
- Exporting the SIS data
- Repair
- General procedures
- Mounting instructions for bearings
- Product manual - IRB
- Mounting instructions for seals
- Cut the paint or surface on the robot before replacing parts
- The brake release buttons may be jammed after service work
- Complete robot
- Replacement of cable harness, axes 5-6
- Replacement of complete arm system
- Upper and lower arm
- Replacement of complete wrist unit
- Replacement of complete upper arm
- Replacement of complete lower arm
- Replacement of lower arm shaft
- Frame and base
- Replacement of brake release board
- Replacement of spherical roller bearing, balancing device
- Replacement of balancing device
- Unloading the balancing device using hydraulic press tool
- Restoring the balancing device using a hydraulic press tool
- Motors
- Replacement of motor axis 2
- Replacement of motor, axis 3
- Replacement of motor, axis 4
- Replacement of motor, axis 5
- Replacement of motor, axis 6
- Gearboxes
- Replacement of gearbox, axis 2
- Replacement of gearbox, axis 3
- Replacement of gearbox, axis 4
- Replacement of gearbox, axis 5
- Replacement of gearbox, axis 6
- Calibration
- Calibration methods
- When to calibrate
- Synchronization marks and axis movement directions
- Calibration movement directions for all axes
- Updating revolution counters
- Calibrating with Axis Calibration method
- Calibration tools for Axis Calibration
- Installation locations for the calibration tools
- Axis Calibration - Running the calibration procedure
- Calibrating with Calibration Pendulum method
- Verifying the calibration
- Checking the synchronization position
- Decommissioning
- Scrapping of robot
- Decommissioning of balancing device

IRC5 Compact
Table of contents
- Table Of Contents
- Table Of Contents
- Overview of this manual
- Safety
- Safety symbols on product labels
- Safety symbols on controller labels
- Safety during troubleshooting
- Applicable standards
- Safety tools
- Safe troubleshooting
- Live voltage inside Drive Module
- Hot parts may cause burns
- Introduction to troubleshooting
- Standard toolkit
- Tips and tricks while troubleshooting
- Work systematically
- Keeping track of history
- Filing an error report
- Troubleshooting by fault symptoms
- Controller not responding
- Low controller performance
- All LEDs are off at controller
- No voltage in service outlet
- Problem starting the FlexPendant
- Problem connecting FlexPendant to the controller
- Erratic event messages on FlexPendant
- Problem jogging the robot
- Reflashing firmware failure
- Inconsistent path accuracy
- Mechanical noise or dissonance
- Manipulator crashes on power down
- Problem releasing Robot brakes
- Intermittent errors
- Force starting of Boot Application
- Troubleshooting by unit
- Troubleshooting the FlexPendant
- Troubleshooting communications
- Troubleshooting fieldbuses and I/O units
- Troubleshooting the computer unit
- Troubleshooting the panel board
- Troubleshooting the drive system
- Troubleshooting the axis computer
- Troubleshooting the system power supply
- Troubleshooting the power distribution board
- Troubleshooting the contactor interface board
- Troubleshooting the customer I/O power supply
- xxxx
Related products
COM600 seriesCOMMANDER 300COM600 series 5.0Busch-ComfortTouch 9Busch-ComfortTouch 12.1ControlNet FCNA-01CP1485CP1486CP1484CP3484ABB categories
Industrial Equipment
DC Drives
Controller
Relays
Measuring Instruments
Circuit breakers
Battery Charger
Industrial Electrical
Transformer
Switch
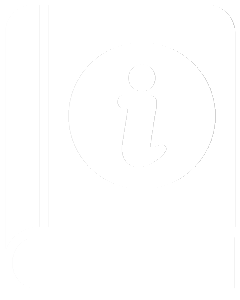
manualsdatabase
Your AI-powered manual search engine