YASKAWA YRC1000 manuals

YRC1000
Table of contents
- Table Of Contents
- Table Of Contents
- Introduction
- Hand Guiding Function
- System Configuration of Hand Guiding Function
- System Configuration for Using Hand Guiding Device of Handle Type
- System Configuration for Using Hand Guiding Device of Grip Type
- Connection for Hand Guiding Device
- Connection for Presence Detection Sensor
- Speed Limiting Function
- Setup of Hand Guiding Function
- Filter Setting
- Setting of Speed Coefficient
- Setting of Operation Angle Limit
- Setting of Area Limit
- Tool Setting
- Tool Coordinate System and Sensor Coordinate System
- Calculating Setting Value of Sensor Mounting Angle
- Setting Example of Sensor Mounting Angle
- Setting Confirmation of Sensor Mounting Angle
- Hand Guiding Function Execution Procedures
- Job Creation for Hand Guiding Function Execution
- Mode
- Inching Mode
- Translation/Rotation
- Force Sensor/ I/O Input
- Calibration of Force Sensor
- Register Output Function
- Risk Assessment
- Risk Reduction Measures
- User Variables and General I/O Signals to be Used with Hand Guiding Function
- General I/O Signal List
- Ladder Program
- Troubleshooting
- Enabling Force Sensor
- Robot Operating Method When Hand Guiding Device Disconnected
- Alarm List

YRC1000
Table of contents
- Table Of Contents
- Outline
- Hardware Specifications
- J71GF11-T2 Specifications
- Communication Specifications
- Mounting the J71GF11-T2 Board
- Opening the Front Door of the YRC1000
- Mounting the J71GF11-T2 Board on the YRC1000
- Closing Front Door of the YRC1000
- I/O Signal Allocation
- External I/O Setting
- Transmitting Data
- YRC1000 I/O Allocation Example (For Handling)
- YRC1000 I/O Allocation Example (For Except Handling)
- Board Status
- PLC Setting
- IO Confirmation
- Setting of Star/ Line, Ring Connection and create radder program
- Block Data Assurance per Station
- Error Indication

YRC1000
Table of contents
- Contents
- Table Of Contents
- Outline of Arc Welding Diagnosis Function
- Parameter
- Operation Outline
- Data Setting for Arc Welding Diagnosis
- Displaying / Non-displaying Arc Weld Diagnosis Window
- Preparation for Arc Weld Diagnosis Window
- Diagnosis Mode Setting
- Operating Arc Weld Diagnosis Window
- Selection of Bead Number
- Setting of Threshold for Determining Error
- Setting of Error Output Mode and Signal Number
- Setting of Standard Current and Standard Voltage
- Changing of Standard Current and Standard Voltage
- Enable/Disable of Diagnosis
- Saving of Arc Welding Diagnosis Data
- Saving Data
- Setting for Saving of Arc Welding Diagnosis Data (Manual)
- Retry Saving of Data
- AP Parameter
- Alarm / Error / Inform
- HW1485704

YRC1000
Table of contents
- Table Of Contents
- Outline
- Hardware Specifications
- Board Specifications
- Mounting the INpact Board
- Opening the Front Door of the YRC1000
- Mounting the INpact Board on the YRC1000
- Cable Connection
- Closing Front Door of the YRC1000
- I/O Signal Allocation
- Transmission Data
- I/O Allocation Examples for YRC1000 (For Handling)
- I/O Allocation Examples for YRC1000 (Except for Handling)
- The Alarm when Communication Error Occurs Using the Board Status
- Error Indication

YRC1000
Table of contents
- Table Of Contents
- Table Of Contents
- Introduction
- PFL Function
- Speed Monitor Function
- Version YAS2.41 or Later and YRC1000micro System Version
- Escape from Clamping Function
- Relationships among Various Stop Functions
- Direct Teach Function
- External Force Monitor Output
- Configuring Each Function
- Basic Settings for Collaborative Operation
- Configuring the Speed Limit
- Enabling or Disabling Collaborative Operation
- Logic Circuit
- External Sensor Input
- Default Settings of Function Safety General-Purpose I/O Signals
- Enabling or Disabling the PFL function
- Steps for Enabling the PFL Function
- Configuring the Avoidance Function
- Enabling the Avoidance Function
- Setting the Start and End Thresholds
- Checking the Interrupt Job Settings
- Teaching the Manipulator with the Direct Teach Function
- Safety Precautions
- About the Behavior near Singularity
- Settings Related to the Tool
- How to Configure the Tool File
- How to Configure the Tool Change Settings
- Daily Inspection Items
- Monitor
- How to Reconfigure the Torque Sensor Home Position
- Troubleshooting
- Alarm List
- Minor Alarms
- Variable List
- I/O List
- Auxiliary Relay
- General Output
- General Input
- YRC1000
- Control Status Signal
- Register List
- Default Settings of the Functional Safety Condition Files
- Simultaneously

YRC1000
Table of contents
- Table Of Contents
- Table Of Contents
- Simplified Teaching and Playback
- Teaching Procedure
- Path Confirmation
- Correcting a Job
- Changing the Position Data
- Playback
- Example for General Purpose Application
- Confirmation of Cutting Operation (Speed Limitation Drive)
- Operation for Tool Control
- Tool Control Settings
- Work Instructions
- CALL Instruction
- WVON Instruction
- Weaving Operation
- Cases that Require the Registration of Reference Points
- WVON
- Explanation
- Registering the WVON Instruction
- WVOF Instruction
- Registering the WVOF Instruction
- WEAVING CONDITION Window
- Displaying the Weaving File
- Editing the Condition Data
- Prohibiting Weaving
- Method to Prohibit Weaving during a "TEST RUN" or FWD Operation
- Table of Work Instructions
- Handling Application
- HAND Instruction
- Instruction and Additional Items
- HSEN (Gripper Sensor) Instruction
- Examples
- Handling Window
- Shock Sensor Function
- Registering Instructions
- HSEN Instruction

YRC1000
Table of contents
- Table Of Contents
- Table Of Contents
- System Overview of Spot Welding System Using an Air Gun
- Function Keys
- Teaching
- Welding On/Off
- Resetting Alarms
- Registering Work Instructions
- GUNCL Instruction
- SPOT Instruction
- STROKE Instruction
- STRWAIT Instruction
- Setting Welding Conditions (for Air Gun)
- Spot Welder Condition Data Setting
- Spot Gun Condition Data File
- Spot Welding Diagnosis
- Tip Hit Count Clear
- Spot Gun Motion Control
- C Type Gun
- Process Timing
- OPERATION MODE = 1 (SHORT OPEN → WELDING → SHORT OPEN)
- OPERATION MODE = 2 (SHORT OPEN → WELDING → FULL OPEN)
- OPERATION MODE = 3 (FULL OPEN → WELDING → SHORT OPEN)
- OPERATION MODE = 4 (FULL OPEN → WELDING → FULL OPEN)
- Stroke Change Control Method
- I/O Allocation
- Output Allocation Window
- Pseudo Input Signal Window
- Allocation Signal Meanings
- Monitor Function for Spot Welding Equipment
- Spot Welding Exclusive Signal Allocation List
- Instruction List

YRC1000
Table of contents
- Table Of Contents
- Editing Ladder Programs
- Editing by Mnemonic and Editing Program
- Ladder Editor Window
- Editing Operation of Ladder View Window
- Cut (Copy) and Paste Rungs
- Editing Operation of Ladder Editing Window
- Delete Instructions
- Insert Columns
- Insert Rows
- Delete Columns
- Delete Rows
- Undo and Redo
- Clear Rungs
- Save Edited Ladders
- Compile
- Search
- Go to Rung
- Find Value
- Find Forward
- Find Output Relays
- Other Functions
- Instruction Use Table
- Relay Use Table
- Register Specification List
- Mnemonic Display
- Open Relay Label File
- Input Name
- Ladder Monitoring Function

YRC1000
Table of contents
- Table Of Contents
- Table Of Contents
- Table Of Contents
- Table Of Contents
- System Overview (Motor Gun)
- Function Keys
- Setting of Motor Gun
- Posture of Motor Gun
- Tentative Setting of Torque to Pressure Conversion Data
- Register the Base Position for Wear Detection (Fixed Side)
- Execution of Motor Gun Auto Tuning Function
- Confirmation of Motor Gun Auto Tuning Operation Status
- Clearance of MOTOR GUN AUTO TUNING Setting
- Setting of Torque to Pressure Conversion Data
- Alarm
- System Setting (Motor Gun)
- Entering Pulse to Stroke Conversion Data
- I/O Signals for a Motor Gun
- Welding I/F File
- I/O Allocation
- PSEUDO INPUT SIGNAL Window
- Registering the Operation Tool
- When Using a Double Arm Move Gun
- Setting the Software Limit Value
- Setting the Lost-tip Detection Value
- Gun Detail Setting File
- Application Condition Setting
- Before Teaching
- Open/Close of Motor Gun
- Creation of Job
- Registering Steps
- Playback (Motor Gun)
- Welding Instruction (SVSPOT Instruction)
- Setting of Gun Pressure
- Welding Current and Welding Time Settings
- Setting the Gun Stroke Motion Speed
- Dry Spot (Motor Gun)
- Dry Spot Pressure Setting
- Workpiece Transfer Function Using a Motor Gun
- Instruction for Grasping/Releasing Workpieces
- Manual Operation for Grasping/Releasing Workpieces
- Manual Pressure
- Clearance Move Instruction (SVSPOTMOV Instruction)
- Setting the Teaching Type
- Setting the Clearance Files
- Operations for Teaching Welding Points
- Clearance Move Instruction
- Clearance Move
- Press Teaching Function
- Procedure for Registering the Position
- Setting the Gun Pushing Coefficient
- Work Search Function
- Parameter
- Tip Dressing Instruction (SVDRESMOV Instruction)
- Teaching Type Setting
- Dressing Position Teaching Operation
- Tip Dress Instruction
- Tip Dress Instruction (SVDRESMOV) Flow
- Suspend and Restart of the Tip Dress Operation
- Wear Detection with Tip Dressing Instruction
- Dry Tip Dressing Operation
- Tip Dress Supervision
- Wear Detection and Wear Compensation Operation Flow Chart
- Wear Detection
- Movable Side Tip Detection
- Example of Wear Detection
- Spot Supervision Window Setting
- Wear Compensation
- Tip Wear Compensation for Fixed Gun
- User Coordinate Number Setting
- Example of Compensation
- Teaching Positions with a Worn Tip
- Wear Amount Loading
- Tip Mounting Position Error Detection
- Tip Mounting Position Error Detection Flow Chart
- Job Examples
- Importing the Tip Mounting Position Error
- Monitoring the Failure of Mounting Tips
- Motor Gun Stroke
- Registering the current position
- Moving to Full-open/Short-open Position
- Gun Change
- Gun Change Job
- Gun Changing Timing
- Touch Teaching Function
- Registering and Confirming Positions by Touch Teaching
- Signal Dry Spot
- Gun Pressure Compensation Function
- Overview
- Setting the Pressure Compensation Value
- Setting the Gun Arm Bend Compensation Coefficient
- Compensation Example
- Disabling Gun Arm Bend Compensation
- Welding Conditions Group Output Function
- Setting the Group Output Tag
- Group Output
- Workpiece Thickness Detection Function
- Instruction
- Operation Procedures
- Related Functions
- Notes
- Automatic Tool Number Select Function for Guns
- Loading the DX100 Motor Gun Condition File
- The Instruction List (Motor Gun)

YRC1000
Table of contents
- Table Of Contents
- Form Cutting Motion
- Patterns for Cutting
- Teaching
- Tool Position and Cutting Pattern
- Cutting Width Correction Function
- Example of Form Cutting Function
- Example of a Motion Path
- Motion Example 1
- Motion Example 2
- Form Cutting Start Motion Instruction
- Registering Instructions
- Registering in Variables
- Form Cutting Instruction
- Form Cut Setting File
- Settings
- Details of File Settings
- Specifying the ROTATION DIRECTION
- Examples of File Setting for Each Pattern
- Rectangle Including Squares
- Ellipse
- Pentagon
- Hexagon
- Displaying and Editing File
- Alarm Message List

YRC1000
Table of contents
- Table Of Contents
- Table Of Contents
- Functional Overview
- Setup
- Setting and Confirmation of Hardware Configuration
- Connection of Welding Power Source and YRC1000
- Digital Interfaces and also Other Devices with Data Transmission Function using Ethernet Function
- System Configuration
- I/O Module Setting Check after Changing EW Board Station Number Setting
- Setting of Optional Function "Network Function"
- Setting of Optional Function "WELDCOM Function"
- Detailed Setting of Welding Power Source
- I/O Module Setting Check after Adding Virtual EW Module
- Loading of MotoPlus Application (When Welder is FroniusTPSi)
- Setting of Parameter (When Welder is MOTOWELD)
- Setting of Parameter (When Welder is FroniusTPS)
- Setting of Parameter (When Welder is FroniusTPSi)
- Optional Parameters for Fronius TPS
- Operation of Welding Condition File Edit Window
- MOTOWELD Type: Operation of Top Window
- MOTOWELD Type: Operation of Weld type Window
- MOTOWELD Type: Operation of Customize Window
- MOTOWELD Type: Operation of Maintenance Window
- MOTOWELD Type: Operation of Welder Parameter Window
- FroniusTPS Type: Operation of Top Window
- FroniusTPS Type: Operation of Program No. setting Window
- FroniusTPS Type: Operation of Param. setting Window
- FroniusTPSi Type: Operation of Top Window
- FroniusTPSi Type: Operation of Select Synergic Window
- Job Preparation for Welding
- Synchro-welding Function [Compatible Welder : MOTOWELD-X350]
- Setting of "Synchro-welding"
- Alarm and Error
- Error

YRC1000
Table of contents
- Table Of Contents
- What is the Interrupt Job Function?
- Setting of the Interrupt Job Function
- Setting of Interruption Table
- Setting of Job Names
- Setting of Interruption Levels
- Registration of Instructions
- DI (Disable Interruption) Instruction
- Execution of an Interrupt Job
- Output Signal of "Interrupt Job in Execution"
- Application Examples
- Interruption During Move Instruction with NWAIT
- Interruption During Circular Interpolation Move Instruction (MOVC)
- System with Independent Control
- Instruction List
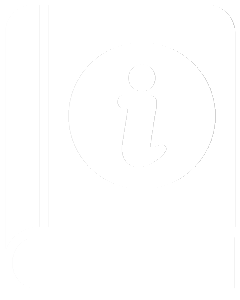
manualsdatabase
Your AI-powered manual search engine