ABB ACS580-07 manuals

ACS580-07
Table of contents
- List of related manuals
- Table Of Contents
- Table Of Contents
- Contents of this chapter
- Target audience
- Exclusion of liability
- Quick reference guide for implementing a safety system
- Contents this chapter
- Operation principle
- ACS880-17/37 drives, frame R11
- ACS880-07 drives, frames nxDXT + nxR8i
- ACS880-17/37 drives, frames nxR8i + nxR8i
- Fault reaction function
- Hardware settings
- Start-up and acceptance test
- Use of the safety function
- Maintenance
- Intentional misuse
- Safety data
- ACS880-07 drives with a main contactor
- ACS880-17/37 drives with a main contactor
- ACS880-07/17/37 drives with a main circuit breaker
- Safety block diagrams
- Relevant failure modes
- General rules, notes and definitions
- Ambient conditions
- Related standards and directives
- Product and service inquiries

ACS580-07
Table of contents
- Table Of Contents
- Table Of Contents
- Table Of Contents
- Table Of Contents
- Table Of Contents
- Table Of Contents
- Table Of Contents
- Table Of Contents
- Safety instructions
- Start-up
- Electrical safety in installation, start-up and maintenance
- Additional instructions and notes
- Optical components
- Additional instructions for permanent magnet motor drives
- Contents of this chapter
- Categorization by frame size and option code
- Terms and abbreviations
- Single-line circuit diagram of the drive
- General information on the cabinet layout
- Cabinet layout – R8 and R9 (bottom entry and exit of cables)
- Mounting plate – R6 to R9
- Cabinet layout – R10 and R11 (bottom entry and exit of cables)
- Mounting plate
- Cooling air flow
- Door switches and lights
- Control by PC tools
- IP21
- du/dt filter (option +E205)
- Type designation label
- Necessary tools
- Unpacking the transport package
- Lifting the cabinet
- Moving the cabinet after unpacking
- Final placement
- Attaching methods
- Alternative 2 – Using the holes inside the cabinet
- Examining the compatibility of the motor and drive
- Availability of du/dt filter and common mode filter by drive type
- Additional data for calculating the rise time and the peak line-to-line voltage
- Selecting the power cables
- Typical power cable sizes
- Power cable types for limited use
- Selecting the control cables
- Separate control cable ducts
- Protecting the motor and motor cable in short-circuits
- Implementing the emergency stop function
- Supplying power for the auxiliary circuits
- Implementing a bypass connection
- Implementing a motor temperature sensor connection
- Layout of the cable entries (frames R6 to R9)
- Layout of the cable entries (frames R10 and R11)
- Connecting the power cables
- Checking the insulation of the drive
- Connection procedure (IEC, frames R6 to R9)
- Connection procedure (IEC, frames R10 and R11)
- Connecting the control cables
- Grounding the outer shields of the control cables at the cabinet entry
- Routing the control cables inside the cabinet
- Connecting external wiring to the control unit or optional I/O terminal block
- Connecting the emergency stop push buttons (options +Q951 and +Q963)
- Connecting external power supply wires for the cabinet heater (option +G300)
- Connecting a PC
- Wiring the optional modules
- Default I/O connection diagram
- Option +E205 in frames R10 and R11: DI6 internal overtemperature supervision
- Power supply connections for NPN with option +L504
- Changing internal overtemperature supervision from DI6 to another digital input
- NPN configuration for digital inputs (X2 & X3)
- Connection examples of two-wire and three-wire sensors to analog input (AI2)
- AI1 and AI2 as Pt100, Pt1000, Ni1000, KTY83 and KTY84 sensor inputs (X1)
- Technical data
- Recommended annual maintenance actions by the user
- Cleaning the air inlet (door) meshes (IP42 / UL Type 1 Filtered)
- Outlet (roof) filters (IP54 / UL Type 12)
- Fans
- Replacing the cabinet fan (frames R6 to R9)
- Replacing the door fan (frames R10 and R11)
- Replacing the cabinet fan (frames R10 and R11, IP54)
- Replacing the drive module main fans (frames R6 to R8)
- Replacing the drive module main fans (frame R9)
- Replacing the drive module main fans (frames R10 and R11)
- Replacing the auxiliary cooling fan of the drive module (frames R6 to R9)
- Replacing the drive module (frames R6 to R9)
- Replacing the drive module (frames R10 and R11)
- Replacing the drive module (frames R10 and R11, IP54)
- Capacitors
- Replacing AC fuses
- Replacing the battery in the assistant control panel
- NEC ratings
- Definitions
- Drive types ACS580-0414A-4 and ACS580-0430A-4
- Deratings for special settings in the drive control program
- Fuses (IEC)
- Fuses for branch circuit protection
- Dimensions and weights
- Maximum allowed plinth height for the extraction/installation ramp
- Losses, cooling data and noise
- Terminal and entry data for the power cables
- US – With option +E205
- Connection drawings
- Terminal and connection data for auxiliary control circuits
- Electrical power network specification
- Protection classes
- Ambient conditions
- Auxiliary circuit power consumption
- Applicable standards
- Compliance with the European Low Voltage Directive
- Declaration of Conformity
- Compliance with the EN 61800-3:2004
- UL marking
- RCM marking
- Disclaimers
- 13 Dimension drawings
- Frames R6 and R7 (IP21, UL Type 1)
- Frames R6 and R7 (+B054: IP42, UL Type 1)
- Frames R6 and R7 (+B055: IP54, UL Type 12)
- Frames R6 and R7 (+H351 and +H353: top entry and exit)
- Frames R6 and R7 (+F289)
- Frames R6 and R7 (+F289, +H351, +H353)
- Frames R8 and R9 (IP21)
- Frames R8 and R9 (+B054: IP42, UL Type 1)
- Frames R8 and R9 (+B055: IP54, UL Type 12)
- Frames R8 and R9 (+H351 and +H353: top entry and exit)
- Frames R8 and R9 (+F289)
- Frames R8 and R9 (+F289, +H351, +H353)
- Frames R10 and R11 (IP21)
- Frames R10 and R11 (+B054: IP42, UL Type 1)
- Frames R10 and R11 (+B055: IP54, UL Type 12)
- Frames R10 and R11 (+F289)
- Frames R10 and R11 (+H351, +H353)
- Frames R10 and R11 (+B054: IP42, UL type 1, +H351, +H353)
- Frames R10 and R11 (+B055: IP54, UL type 12, +H351, +H353)
- Compliance with the European Machinery Directive
- Grounding of protective shields
- Single-channel connection
- Single drive (external +24 V DC power supply)
- Multiple drives (internal power supply)
- Multiple drives (external power supply)
- Start-up including acceptance test
- Maintenance
- Competence
- Abbreviations
- Layout
- Electrical installation
- General cabling instructions
- Diagnostics
- CMOD-01 multifunction extension module (external 24 V AC/DC and digital I/O)
- Mechanical installation
- CMOD-02 multifunction extension module (external 24 V AC/DC and isolated PTC interface)
- CPTC-02 ATEX-certified thermistor protection module (external 24 V AC/DC and isolated PTC interface

ACS580-07
Table of contents
- Table Of Contents
- Table Of Contents
- Table Of Contents
- Table Of Contents
- Table Of Contents
- Table Of Contents
- Table Of Contents
- Table Of Contents
- Table Of Contents
- Safety instructions
- General safety in installation, start-up and maintenance
- General safety in operation
- Electrical safety in installation, start-up and maintenance
- Additional instructions and notes
- Optical components
- Additional instructions for permanent magnet motor drives
- Contents of this chapter
- Categorization by frame size and option code
- Terms and abbreviations
- Single-line circuit diagram of the drive
- General information on the cabinet layout
- Cabinet layout – R8 and R9 (bottom entry and exit of cables)
- Mounting plate – R6 to R9
- Cabinet layout – R10 and R11 (bottom entry and exit of cables)
- Mounting plate
- Cooling air flow
- Overview of power and control connections
- Door switches and lights
- Control by PC tools
- IP21
- Molded case circuit breaker (MCCB, option +F289)
- Type designation label
- Necessary tools
- Moving and unpacking the drive
- Unpacking the transport package
- Lifting the cabinet
- Moving the cabinet after unpacking
- Final placement
- Attaching methods
- Alternative 2 – Using the holes inside the cabinet
- Examining the compatibility of the motor and drive
- Availability of du/dt filter and common mode filter by drive or inverter type
- Additional data for calculating the rise time and the peak line-to-line voltage
- Additional note for common mode filters
- Typical power cable sizes
- Power cable types
- Not allowed power cable types
- Metal conduit
- Signals in separate cables
- Routing the cables
- General guidelines – North America
- Continuous motor cable shield/conduit or enclosure for equipment on the motor cable
- Protecting the motor against thermal overload
- Using power factor compensation capacitors with the drive
- Implementing a bypass connection
- Connecting motor temperature sensor to the drive via an option module
- Protecting the drive against ground faults
- Implementing the Power-loss ride-through function
- Using a contactor between the drive and the motor
- Implementing a motor temperature sensor connection
- Layout of the cable entries (frames R6 to R9)
- Layout of the cable entries (frames R10 and R11)
- Connecting the power cables
- Checking the insulation of the drive system
- Guidelines for installing the drive to a TT system
- Identifying different types of electrical power systems
- Disconnecting the EMC filter and ground-to-phase varistor (R6 to R9)
- Connecting the motor cable at the motor end
- Connection procedure (IEC, frames R10 and R11)
- Connecting the control cables
- Grounding the outer shields of the control cables at the cabinet entry
- Routing the control cables inside the cabinet
- Connecting external wiring to the control unit or optional I/O terminal block
- Connecting the emergency stop push buttons (options +Q951 and +Q963)
- Connecting external power supply wires for the cabinet heater (option +G300)
- Setting the voltage range of the auxiliary control voltage transformer (T21)
- Installing option modules
- Option slot 1 (fieldbus adapter modules)
- Default I/O connection diagram
- Option +E205 in frames R10 and R11: DI6 internal overtemperature supervision
- Power supply connections for NPN with option +L504
- Changing internal overtemperature supervision from DI6 to another digital input
- NPN configuration for digital inputs (X2 & X3)
- Connection examples of two-wire and three-wire sensors to analog input (AI2)
- AI1 and AI2 as Pt100, Pt1000, Ni1000, KTY83 and KTY84 sensor inputs (X1)
- Technical data
- Recommended annual maintenance actions by the user
- Cleaning the air inlet (door) meshes (IP42 / UL Type 1 Filtered)
- Outlet (roof) filters (IP54 / UL Type 12)
- Fans
- Replacing the cabinet fan (frames R6 to R9)
- Replacing the door fan (frames R10 and R11)
- Replacing the cabinet fan (frames R10 and R11, IP54)
- Replacing the drive module main fans (frames R6 to R8)
- Replacing the drive module main fans (frame R9)
- Replacing the drive module main fans (frames R10 and R11)
- Replacing the auxiliary cooling fan of the drive module (frames R6 to R9)
- Replacing the drive module (frames R6 to R9)
- Replacing the drive module (frames R10 and R11)
- Replacing the drive module (frames R10 and R11, IP54)
- Capacitors
- Replacing AC fuses
- Control panel
- NEC ratings
- Definitions
- Drive types ACS580-0414A-4 and ACS580-0430A-4
- Deratings for special settings in the drive control program
- Fuses (IEC)
- Fuses (UL)
- Fuses for branch circuit protection
- Dimensions and weights
- Maximum allowed plinth height for the extraction/installation ramp
- Losses, cooling data and noise
- Terminal and entry data for the power cables
- US – With option +E205
- Connection drawings
- Terminal and connection data for auxiliary control circuits
- Electrical power network specification
- Protection classes
- Ambient conditions
- Materials
- Applicable standards
- Markings
- Declaration of Conformity
- Compliance with the EN 61800-3:2004
- UL marking
- Disclaimers
- 13 Dimension drawings
- Frames R6 and R7 (IP21, UL Type 1)
- Frames R6 and R7 (+B054: IP42, UL Type 1)
- Frames R6 and R7 (+B055: IP54, UL Type 12)
- Frames R6 and R7 (+H351 and +H353: top entry and exit)
- Frames R6 and R7 (+F289)
- Frames R6 and R7 (+F289, +H351, +H353)
- Frames R8 and R9 (IP21)
- Frames R8 and R9 (+B054: IP42, UL Type 1)
- Frames R8 and R9 (+B055: IP54, UL Type 12)
- Frames R8 and R9 (+H351 and +H353: top entry and exit)
- Frames R8 and R9 (+F289)
- Frames R8 and R9 (+F289, +H351, +H353)
- Frames R10 and R11 (IP21)
- Frames R10 and R11 (+B054: IP42, UL Type 1)
- Frames R10 and R11 (+B055: IP54, UL Type 12)
- Frames R10 and R11 (+F289)
- Frames R10 and R11 (+H351, +H353)
- Frames R10 and R11 (+B054: IP42, UL type 1, +H351, +H353)
- Frames R10 and R11 (+B055: IP54, UL type 12, +H351, +H353)
- Compliance with the European Machinery Directive
- Wiring
- Connection with external power supply
- Wiring with external power supply
- Grounding of protective shields
- Operation principle
- Start-up including acceptance test
- Maintenance
- Fault tracing
- Safety data
- TÜV certificate
- Layout
- Electrical installation
- Start-up
- CHDI-01 115/230 V digital input extension module
- Installing the module
- General cabling instructions
- Diagnostics
- CMOD-01 multifunction extension module (external 24 V AC/DC and digital I/O)
- Mechanical installation
- CMOD-02 multifunction extension module (external 24 V AC/DC and isolated PTC interface)
- CPTC-02 ATEX-certified thermistor protection module (external 24 V AC/DC and isolated PTC interface)
Related products
ACS580-04ACS580-07-0715A-4ACS580-07-0810A-4ACS580-07-0640A-4ACS580-07-0495A-4ACS580-07-0870A-4ACS580-07-0575A-4ACH580-07ACQ580-07ACS880-07ABB categories
Industrial Equipment
DC Drives
Controller
Relays
Measuring Instruments
Circuit breakers
Battery Charger
Industrial Electrical
Transformer
Switch
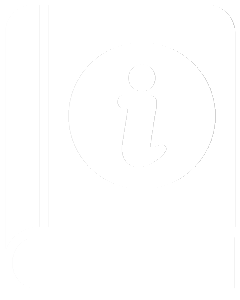
manualsdatabase
Your AI-powered manual search engine