Vacon NX manuals

NX
Table of contents
- vacon
- Table Of Contents
- Table Of Contents
- SAFETY
- Cautions
- Running the motor
- EU DIRECTIVE
- Environment definitions in product standard EN 61800-3 (2004)
- RECEIPT OF DELIVERY
- Storage
- Warranty
- TECHNICAL DATA
- Power ratings
- Vacon NX_5 – Mains voltage 380—500 V
- Vacon NX_6 – Mains voltage 525—690 V
- Brake resistor ratings
- INSTALLATION
- Cooling
- Standalone units (FR10 to FR11)
- Power losses
- CABLING AND CONNECTIONS
- DC supply and brake resistor cables
- Cable and fuse sizes, NX_6, FR6 to FR9
- Cable and fuse sizes, NX_5, FR10 to FR11
- Understanding the power unit topology
- Changing the EMC protection class
- Mounting of cable accessories
- Frames FR7 and FR8
- Installation instructions
- Stripping lengths of motor and mains cables
- Vacon NX_ frames and installation of cables
- Cable selection and unit installation in accordance with the UL standards
- Cable and motor insulation checks
- Control unit
- Control connections
- Control cables
- Control terminal signals
- Digital input signal inversions
- Jumper selections on the OPTA1 basic board
- CONTROL KEYPAD
- Drive status indications
- Keypad push-buttons
- Navigation on the control keypad
- system menu
- Monitoring menu (M1)
- Parameter menu (M2)
- Keypad control menu (M3)
- Keypad reference
- Active faults menu (M4)
- Fault types
- Fault codes
- Fault time data record
- Fault history menu (M5)
- System menu (M6)
- Language selection
- Copy parameters
- Parameter comparison
- Security
- Keypad settings
- Hardware settings
- System info
- software version
- Expander board menu (M7)
- COMMISSIONING
- FAULT TRACING


NX
Table of contents
- Table Of Contents
- Table Of Contents
- Table Of Contents
- Danger
- Warnings
- Cautions
- Running the motor
- EU DIRECTIVE
- Manufacturer's declaration of conformity
- RECEIPT OF DELIVERY
- Storage and shipping
- TECHNICAL DATA
- Power ratings
- Inverter units
- INSTALLATION
- NX Liquid-Cooled dimensions
- Cooling
- Condensation
- Cooling system connections
- Drive derating
- Input chokes
- Installation of input chokes
- ELECTRICAL CABLING AND CONNECTIONS
- Drive protection – Fuses
- Fuse sizes
- Cable installation instructions
- Supply busbars for inverter units
- Installation space
- Installation of ferrite rings (option) on the motor cable
- Cable and motor insulation checks
- Control unit
- Control board power-up
- Control terminal signals
- Control unit mounting box
- Internal connections
- Connections between power unit ASIC and the control unit
- Connections between mains device and inverter power module
- CONTROL KEYPAD
- Control place indications
- Keypad push-buttons
- Navigation on the control keypad
- Monitoring menu (M1)
- Parameter menu (M2)
- Keypad control menu (M3)
- Active faults menu (M4)
- Fault history menu (M5)
- System menu (M6)
- Expander board menu (M7)
- Further keypad functions
- COMMISSIONING
- Commissioning of the frequency converter
- FAULT TRACING
- Load test with motor
- DC link test (without motor)
- ACTIVE FRONT END (NXA)
- Type designation code
- Active Front End unit technical data
- Liquid Cooled RLC filters
- Power rating and dimensions
- Removing HF capacitors
- Active front end - fuse selection
- Pre-Charcing circuit
- Parelling
- Common pre-charging circuit
- Each Active Front End unit has the pre-charcing circuit
- BRAKE CHOPPER UNIT (NXB)
- NXB topologies and connection
- Brake chopper unit technical data
- BCU power ratings
- Vacon NXB; DC voltage 640–1100 V
- Vacon brake resistors and brake chopper dimensioning
- Braking power and resistance, mains voltage 380–500 Vac/600–800 Vdc
- Braking power and resistance, mains voltage 525–690 Vac/840–1100 Vdc
- Brake chopper unit – Fuse selection
- APPENDICES


NX
Table of contents
- vacon
- Table Of Contents
- INSTALLATION OF THE OPT-AF BOARD
- OPT-AF Board layout
- STO AND SS1 SAFETY FUNCTIONS
- Safe Torque Off (STO) principle
- Safe Stop 1 (SS1) principle
- Technical details
- Safety-related data according to the standard
- Technical data
- Wiring examples
- Example 2: OPT-AF board with reset for Safe Torque Off (STO) or EN 60204-1 stop category 0
- Example 3: OPT-AF board with external safety relay module with or without reset for Safe Torque Off (STO) or EN 60204-1 stop category 0
- Example 4: OPT-AF board with external time delayed safety relay for Safe Stop 1 (SS1) or EN 60204-1 stop category 1
- Commissioning
- Checklist for commissioning the OPT-AF board
- Parametrizing the drive for the Safe Torque Off (STO) safety functions
- Parametrizing the drive and the external time delayed safety relay for Safe Stop (SS1) safety function
- Maintenance
- THERMISTOR FUNCTION (ATEX)
- Hardware and connections
- Short circuit monitoring
- OPT-AF board parameter
- Fault diagnosis of thermistor function

NX
Table of contents
- Table Of Contents
- Introduction
- Programming principle of the digital input signals
- Defining a certain function with NC_Drive programming tool
- Control I/O
- Mechanical Brake Control Application – Parameter lists
- Keypad control (Control keypad: Menu M3)
- Description of parameters
- INPUT SIGNALS
- OUTPUT SIGNALS
- DRIVE CONTROL
- BRAKE CONTROL
- MOTOR CONTROL
- PROTECTIONS
- AUTO RESTART PARAMETERS
- IDENTIFIED PARAMETERS
- KEYPAD CONTROL PARAMETERS
- Control signal logic in Mechanical brake control Application
- Fault tracing

NX
Table of contents
- Table Of Contents
- Table Of Contents
- Table Of Contents
- Safety
- Danger
- Grounding and earth fault protection
- Running the motor
- EU directive
- Explanations of voltage classes
- Manufacturer's declaration of conformity
- Receipt of delivery
- Storage and shipping
- Warranty
- Technical data
- Power ratings
- Inverter units
- Installation
- Cooling
- Condensation
- Cooling system connections
- Drive derating
- Input chokes
- Installation of input chokes
- Electrical cabling and connections
- Drive protection – Fuses
- Cable installation instructions
- Supply busbars for inverter units
- Installation space
- Installation of ferrite rings (option) on the motor cable
- Cable and motor insulation checks
- Control unit
- Control board power-up
- Control terminal signals
- Control unit mounting box
- Internal connections
- Connections between power unit ASIC and the control unit
- Connections between mains device and inverter power module
- Control keypad
- Control place indications
- Keypad push-buttons
- Navigation on the control keypad
- Monitoring menu (M1)
- Parameter menu (M2)
- Keypad control menu (M3)
- Active faults menu (M4)
- Fault history menu (M5)
- System menu (M6)
- Expander board menu (M7)
- Further keypad functions
- Commissioning
- Commissioning of the AC drive
- Fault tracing
- Load test with motor
- DC link test (without motor)
- Active front end (NXA)
- Type designation code
- Active Front End unit technical data
- Liquid-Cooled RLC filters
- Power rating and dimensions
- Removing HF capacitors
- Active front end - fuse selection
- Pre-Charcing circuit
- Parelling
- Common pre-charging circuit
- Each Active Front End unit has the pre-charcing circuit
- Non-regenerative front end
- Installation of the NFE control cables
- Type designation codes
- Non-regenerative Front End unit technical data
- Dimensions
- Chokes
- Non-regenerative front end - fuse selection
- Fuse sizes, Non-regenerative Front End units
- Option board settings
- DC pre-charging circuit
- Paralleling
- Parameters
- CH60 Liquid-cooled NFE protections
- Fault codes
- Brake chopper unit (NXB)
- Brake chopper unit technical data
- BCU power ratings
- VACON® NXB; DC voltage 640–1100 V
- Braking energy and losses
- Braking power and resistance, mains voltage 380–500 Vac/600–800 Vdc
- Braking power and resistance, mains voltage 525–690 Vac/840–1100 Vdc
- Brake chopper unit – Fuse selection
- Appendices

NX
Table of contents
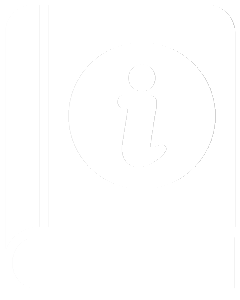
manualsdatabase
Your AI-powered manual search engine