ABB ACS800-U7 manuals

ACS800-U7
Table of contents
- Table Of Contents
- Table Of Contents
- Table Of Contents
- Table Of Contents
- Table Of Contents
- Table Of Contents
- Chapter overview
- Product and service inquiries
- How to perform the ID Run
- Control panel
- Panel operation mode keys and displays
- Drive control with the panel
- How to set speed reference
- Actual signal display mode
- How to display the full name of the actual signals
- How to display and reset an active fault
- Parameter mode
- How to adjust a source selection (pointer) parameter
- Function mode
- How to download data from the panel to a drive
- Drive selection mode
- Reading and entering packed boolean values on the display
- External control
- Block diagram: start, stop, direction source for EXT1
- Reference types and processing
- Programmable analog inputs
- Programmable analog outputs
- Programmable digital inputs
- Programmable relay outputs
- Actual signals
- Motor identification
- Automatic Start
- Flux Braking
- Flux Optimization
- Speed controller tuning
- Speed control performance figures
- Programmable protection functions
- Settings
- Ground Fault Protection
- Preprogrammed Faults
- Overfrequency
- Motor temperature measurement through the standard I/O
- Motor temperature measurement through the analog I/O extension
- Adaptive Programming using the function blocks
- General
- Checklist for a quick start-up
- Installation
- Master/Follower link specification
- Default control connections
- Tension macro
- OPEN LP TORQ
- Lead-Winder macro
- Torque Follower macro
- User macros
- REFERENCE SELECT
- CONSTANT SPEEDS
- ANALOG INPUTS
- RELAY OUTPUTS
- ANALOG OUTPUTS
- SYS CTRL INPUTS
- LIMITS
- START/STOP
- ACCEL/DECEL
- SPEED CONTROL
- TORQ REF CTRL
- FLUX CONTROL
- FAULT FUNCTIONS
- SUPERVISION
- INFORMATION
- MTR TEMP MEAS
- PULSE ENCODER
- FIELDBUS DATA
- CORE SPEED MATCH
- DANCER CONTROLS
- TENSION CONTROLS
- INERTIA CONTROL
- DIA CALC CONTROL
- TORQUE MEM CTRL
- LEAD CTRL
- ADAPT PROG CTRL
- ADAPTIVE PROGRAM
- USER CONSTANTS
- DATASET INPUT SEL
- DATASET OUTPUT SEL
- OPTION MODULES
- START-UP DATA
- Redundant fieldbus control
- Setting up communication through a fieldbus adapter module
- Setting up communication through the Standard Modbus Link
- Modbus addressing
- Setting up communication through Advant controller
- Table 1 Setting up communication
- The fieldbus control interface
- The Control Word and the Status Word
- Communication profiles
- Table 4 DataSet 1 Word 3 - Fieldbus Aux Cmd Wd (Actual Signal 06.03)
- Table 5 Main Status Word (Actual Signal 02.26)
- Table 6 Auxiliary Status Word 4 (Actual Signal 02.28)
- Table 8 Pack Status Bits (Actual Signal 03.15)
- Table 9 Alarm Word 1 (Actual Signal 02.15)
- Table 11 Alarm Word 3 (Actual Signal 02.17)
- Table 13 Fault Word 2 (Actual Signal 02.19)
- Table 15 System Fault Word (Actual Signal 02.21)
- Table 16 INT Fault Info Word (Actual Signal 02.22)
- Table 17 Limit Word 1 (Actual Signal 02.23)
- Table 19 Limit Word Inv (Actual Signal 02.41)
- Warning messages generated by the drive
- Warning messages generated by the control panel
- Fault messages generated by the drive
- Parameters
- Appendix A1: Motor Rotor Inertia, US
- Appendix A2: Motor Rotor Inertia, IEC
- Figure B-1 Diameter Calculator
- Figure B-2 Dancer Control
- Figure B-3 Tension Control
- Figure B-4 Torque Control
- Figure B-5 SPD/TQ Chain 1

ACS800-U7
Table of contents
- List of related manuals
- What this chapter contains
- Installation and maintenance work
- Grounding
- Mechanical installation and maintenance
- Operation
- Permanent magnet synchronous motor
- Table Of Contents
- Table Of Contents
- Table Of Contents
- Table Of Contents
- Table Of Contents
- Table Of Contents
- Contents
- Installation and commissioning flowchart
- Terms and abbreviations
- Type designation key
- Main circuit and control
- Diagram
- Printed circuit boards
- Before installation
- Cooling air flow
- Fastening the cabinet to the floor and wall (non-marine units)
- Fastening the cabinet with the outside brackets
- Fastening the cabinet through the holes inside the cabinet
- Fastening the cabinet to the floor and roof/wall (marine units)
- Electric welding
- Protecting the motor insulation and bearings
- Requirements table
- Additional requirements for explosion-safe (EX) motors
- Additional requirements for non-ABB high-output and IP23 motors
- Additional data for calculating the rise time and the peak line-to-line voltage
- Thermal overload and short-circuit protection
- Protection against short-circuit inside the drive or in the supply cable
- Ground fault protection
- Prevention of unexpected start-up
- Safe torque off (STO)
- Selecting the power cables
- Alternative power cable types
- Additional US requirements
- Equipment connected to the motor cable
- Protecting the relay output contacts and attenuating disturbances in case of inductive loads
- Selecting the control cables
- Connection of a motor temperature sensor to the drive I/O
- Control cable ducts
- Electrical installation
- Brake resistor assembly
- Example wiring diagram
- Power cable connection diagram
- Connecting the power cables
- Additional instructions for frame size R6
- Connecting the control cables
- Routing the cables (frame sizes R7 and R8)
- degrees EMC grounding at the cable entry
- Special for top entry
- Connecting the cables to the I/O terminals
- Settings of the cooling fan transformer
- Pulse encoder module cabling
- Layout drawing of factory installed optional equipment
- Frame size R7 and R8
- Note on external power supply
- External control connections (non-US)
- External control connections (US)
- RMIO board specifications
- Relay outputs
- Start-up procedure
- Required tools for maintenance
- Cabinet layout
- Frame sizes R7 and R8 without du/dt filter
- Frame sizes R7 and R8 with du/dt filter
- Designations
- Layout of the drive module
- Checking and replacing the air filters
- Replacing the drive module fan (R5 and R6)
- Replacing the drive module fan (R7)
- Replacing the drive module fan (R8)
- Replacing the cabinet fans (R5 and R6)
- Replacing the cabinet fans (frame size R8 only)
- Replacing the IP54 (UL type 12) fan in frame size R6 (option +B055 and +B059)
- Replacing the IP54 (UL type 12) fan in frame sizes R7 and R8 (option +B055 and +B059)
- Capacitors
- Replacing the capacitor pack (R8)
- Replacing the drive module (R5 and R6)
- Replacing the drive module (R7 and R8)
- LEDs
- Symbols
- Fuses
- Notes concerning the fuse tables
- Ultrarapid (aR) fuses
- Optional gG fuses
- Quick guide for selecting between gG and aR fuses
- Cable types
- Cable entries
- NEMA data
- Free space around the unit
- Input power connection
- Cooling
- Materials
- CE marking
- Second environment (drive of category C3)
- C-tick" marking
- UL/CSA markings
- Dimensional drawings
- Frame sizes R5 and R6
- Frame sizes R7 and R8
- IP54 and IP54R units of frame sizes R7 and R8
- Optional brake chopper and resistor(s)
- Resistor installation and wiring
- Protection of frame sizes R6, R7 and R8
- Product and service inquiries
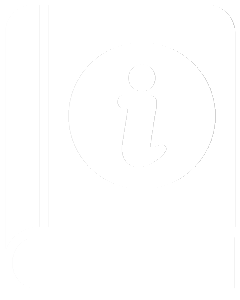
manualsdatabase
Your AI-powered manual search engine