ABB IRB 14000 manuals

IRB 14000
Table of contents
- Table Of Contents
- Table Of Contents
- Table Of Contents
- Overview of this manual
- Product documentation, IRC5
- How to read the product manual
- Network security
- Safety
- General safety information
- Safety in the robot system
- Safety in collaborative operation
- Safety risks
- CAUTION - Hot parts may cause burns
- Safety risks related to tools/work pieces
- Safety risks related to pneumatic systems
- Safety risks with pressure relief valve
- Safety risks during operational disturbances
- Risks associated with live electric parts
- Safety risks for collaborative robots
- Safety actions
- Emergency release of the robot arm
- Manually stopping or overriding the arm
- Brake testing
- Risk of disabling function "Reduced speed 250 mm/s
- Handling of the FlexPendant
- Work inside the working range of the robot
- Signal lamp (optional)
- Safety stops
- What is a safety stop or protective stop
- What is Cartesian speed supervision
- Safety signals and symbols
- Safety symbols on product labels
- Safety related instructions
- DANGER - First test run may cause injury or damage
- DANGER - Make sure that the main power has been switched off
- WARNING - The unit is sensitive to ESD
- WARNING - Safety risks during handling of batteries
- WARNING - Safety risks during work with gearbox lubricants (oil or grease)
- Installation and commissioning
- Unpacking
- Dimensions
- Working range
- Risk of tipping/stability
- On-site installation
- Lifting the robot by two persons
- Orienting and securing the robot
- Manually releasing the brakes
- Loads fitted to the robot
- Installing the signal lamp
- Electrical connections
- Controller
- Connecting power and the FlexPendant
- Connecting a PC and Ethernet based options
- Connectors on the computer unit
- Connecting I/O signals
- Connecting fieldbuses
- Connecting safety signals
- Memory functions
- Connecting an USB memory
- Maintenance
- Maintenance schedule
- Inspection activities
- Inspecting, signal lamp
- Inspecting, cable harness
- Inspecting, plastic and padding
- Replacement/changing activities
- Cleaning activities
- Repair
- General procedures
- Arm and arm covers
- Replacing the encapsulation and covers
- Motors
- Replacing the axis-2 motor
- Replacing the axis-7 motor
- Replacing the axis-3 motor
- Replacing the axis-4 motor
- Replacing the axis-5 motor
- Replacing the axis-6 motor
- Hall sensors
- Replacing the axis-2 hall sensor
- Replacing the axis-7 hall sensor
- Replacing the axis-3 hall sensor
- Replacing the axis-4 hall sensor
- Mechanical stops
- Replacing the axis-2 mechanical stop
- Replacing the axis-7 mechanical stop
- Replacing the axis-3 mechanical stop
- Product manual - IRB
- Replacing the controller fan
- Replacing the capacitor bank
- Replacing the power supply
- Replacing the power distribution board
- Replacing the external power distribution board
- Replacing the axis computer
- Replacing the left arm's drive board
- Replacing the right arm's drive board
- Replacing the I/O board
- Replacing the SMB boards
- Replacing the EtherNet switch
- Replacing the mass memory card
- Replacing the expansion board complete
- Replacing the DeviceNet master
- Replacing the fieldbus adapter
- Brake release harness
- Calibration
- Calibration method
- Calibration scale and correct axis position
- Calibrating the robot
- Updating revolution counters
- Calibration movement directions for all axes
- Verifying the calibration position
- Decommissioning
- Environmental information
- Scrapping of robot
- Reference information
- Applicable safety standards
- Unit conversion
- Specification of screws
- Screw joints
- Weight specifications
- Standard toolkit
- Special tools
- Lifting accessories and lifting instructions
- Index

IRB 14000
Table of contents
- Table Of Contents
- Overview of this manual
- Limit avoidance distance
- Product documentation
- Safety
- Applicable safety standards
- Safety actions
- Recover from emergency stops
- Extinguishing fires
- Working in a safe manner
- About the manual mode
- About the automatic mode
- Safety terminology
- Protective stop and emergency stop
- Introduction to the IRB 14000 robot system
- What is a FlexPendant
- What is RobotWare
- What is RobotStudio
- What is RobotStudio Online
- Using the IRB 14000
- Jogging
- Motion modes
- Coordinated jogging
- Lead-through
- Operating modes
- Collision avoidance
- Collision
- Programming and testing
- I/O signals
- User authorization
- Calibration
- Calibration scale and correct axis position
- Updating revolution counters
- Verifying the calibration position
- System parameters
- Topic I/O System
- Connection Timeout Multiplier
- Topic Motion
- Global Speed Limit
- Arm Check Point Speed Limit
- Arm-Angle Definition

IRB 14000
Table of contents
- Table Of Contents
- Table Of Contents
- Overview of this manual
- Installing the gripper on
- Product manual - IRB
- Product documentation
- Safety
- General safety risks
- Safety risks related to tools/work pieces
- Risks associated with live electric parts
- Installation and commissioning
- Unpacking
- Requirements
- Technical data
- Servo module
- Vacuum module
- Vision module
- Fingers
- On-site installation
- Recommended standard tightening torque
- Mounting the gripper
- Mounting the fingers
- Mounting tools to the vacuum module
- IRB 14000 gripper FlexPendant application
- Installing IRB 14000 gripper FlexPendant application
- Updating IRB 14000 gripper FlexPendant application
- IRB 14000 gripper FlexPendant application GUI
- Commissioning
- Firmware update
- System commissioning
- Maintenance
- Repair
- Replacing the filter and suction cup
- Product manual - IRB 14000 gripper
- Replacing the fingers
- Replacing the shell
- Replacing the pneumatic block
- Replacing the camera
- Replacing the servo base
- RAPID references
- Instructions
- g_JogIn - Jog the gripper to move inward
- g_JogOut - Jog the gripper to move outward
- g_MoveTo - Move the gripper to a target position
- Error handling
- g_GripIn - Jog the gripper to grip inward
- g_GripOut - Jog the gripper to grip outward
- g_Calibrate - Calibrate the gripper
- g_Stop - Stop the gripper
- g_SetMaxSpd - Set the maximum speed
- g_SetForce - Set the gripping force
- RAPID instructions for pneumatic modules
- g_BlowOff1 - Turn off blowing channel 1
- g_BlowOn2 - Turn on blowing channel 2
- g_BlowOff2 - Turn off blowing channel 2
- g_VacuumOn1 - Turn on vacuum channel 1
- g_VacuumOff1 - Turn off vacuum channel 1
- g_VacuumOn2 - Turn on vacuum channel 2
- g_VacuumOff2 - Turn off vacuum channel 2
- Functions
- g_GetPos - Get current gripper position
- g_GetSpd - Get current gripper speed
- g_GetState - Get current gripper status
- g_GetErrID - Get current gripper error ID
- RAPID functions for pneumatic module
- g_GetPressure2 - Get vacuum pressure 2
- RAPID functions for camera module
- Decommissioning
- Reference information
- Unit conversion
- Standard toolkit
- Spare parts
- Spare part lists and illustrations
- Description of spare part versions
- Index
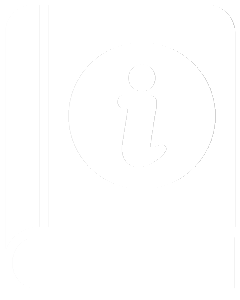
manualsdatabase
Your AI-powered manual search engine