YASKAWA SGMVV manuals

SGMVV
Table of contents
- Outline
- Table Of Contents
- Table Of Contents
- Table Of Contents
- Table Of Contents
- Table Of Contents
- Table Of Contents
- Σ-V Large-Capacity SERVOPACKs and Converters
- Converter Part Names
- Ratings and Specifications
- Basic Specifications
- SERVOPACK and Converter Internal Block Diagrams
- Three-phase 400 V
- Examples of Servo System Configurations
- SERVOPACK Model Designation
- Converter Model Designation
- Combinations of Servomotors, SERVOPACKs, and Converters
- Inspection and Maintenance
- Panel Display
- Chapter 2 Panel Display and Operation of Digital Operator
- Utility Functions (Fn )
- Parameters (Pn )
- Monitor Displays (Un )
- Wiring and Connection
- Main Circuit Wiring
- Main Circuit Wire
- Typical Main Circuit Wiring Examples
- Operation
- Discharging Time of the Main Circuit's Capacitor
- Connecting the Converter to the SERVOPACK
- I/O Signal Connections
- Safety Function Signal (CN8) Names and Functions
- Example of I/O Signal Connections
- I/O Signal Allocations
- Output Signal Allocations
- Examples of Connection to Host Controller
- Sequence Output Circuit
- Wiring Communications Using Command Option Modules
- Encoder Connection
- Selecting and Connecting a Regenerative Resistor Unit
- Connecting a Regenerative Resistor Unit
- Setting Regenerative Resistor Capacity
- Installation Standards
- Selecting and Connecting a Dynamic Brake Unit
- Setting the Dynamic Brake Unit
- Setting the Dynamic Brake Answer Function
- Noise Control and Measures for Harmonic Suppression
- Precautions on Connecting Noise Filter
- Connecting a Reactor for Harmonic Suppression
- Chapter 4 Operation
- Setting Switches S2 and S3 for Option Module Functions
- Basic Functions Settings
- Servomotor Rotation Direction
- Overtravel
- Electronic Gear
- Encoder Output Pulses
- Setting Encoder Output Pulse
- Holding Brakes
- Alarm Occurrence
- Instantaneous Power Interruption Settings
- Setting Motor Overload Detection Level
- Test Without Motor Function
- Motor Position and Speed Responses
- Adjustments
- Digital Operator Displays during Testing without Motor
- Limiting Torque
- External Torque Limit
- Checking Output Torque Limiting during Operation
- Absolute Encoders
- Connecting the Absolute Encoder
- Absolute Data Request (Sensor ON Command)
- Battery Replacement
- Absolute Encoder Setup and Reinitialization
- Absolute Data Reception Sequence
- Multiturn Limit Setting
- Multiturn Limit Disagreement Alarm (A.CC0)
- Other Output Signals
- Rotation Detection Output Signal (/TGON)
- Speed Coincidence Output Signal (/V-CMP)
- Positioning Completed Output Signal (/COIN)
- Positioning Near Output Signal (/NEAR)
- Safety Function
- External Device Monitor (EDM1)
- Application Example of Safety Functions
- Confirming Safety Functions
- Precautions for Safety Functions
- Chapter 5 Adjustments
- Type of Adjustments and Basic Adjustment Procedure
- Basic Adjustment Procedure
- Monitoring Operation during Adjustment
- Safety Precautions on Adjustment of Servo Gains
- Chapter 9 Troubleshooting
- Tuning-less Function
- Tuning-less Levels Setting (Fn200) Procedure
- Related Parameters
- Advanced Autotuning (Fn201)
- Advanced Autotuning Procedure
- Advanced Autotuning by Reference (Fn202)
- Advanced Autotuning by Reference Procedure
- One-parameter Tuning (Fn203)
- One-parameter Tuning Procedure
- One-parameter Tuning Example
- Anti-Resonance Control Adjustment Function (Fn204)
- Anti-Resonance Control Adjustment Function Operating Procedure
- Vibration Suppression Function (Fn205)
- Vibration Suppression Function Operating Procedure
- Additional Adjustment Function
- Manual Adjustment of Friction Compensation
- Current Control Mode Selection Function
- Compatible Adjustment Function
- Mode Switch (P/PI Switching)
- Torque Reference Filter
- Chapter 6 Utility Functions (Fn )
- List of Utility Functions
- Alarm History Display (Fn000)
- JOG Operation (Fn002)
- Origin Search (Fn003)
- Program JOG Operation (Fn004)
- Initializing Parameter Settings (Fn005)
- Clearing Alarm History (Fn006)
- Offset Adjustment of Analog Monitor Output (Fn00C)
- Gain Adjustment of Analog Monitor Output (Fn00D)
- Signal (Fn00E)
- Write Prohibited Setting (Fn010)
- Servomotor Model Display (Fn011)
- Software Version Display (Fn012)
- Resetting Configuration Errors in Option Modules (Fn014)
- Vibration Detection Level Initialization (Fn01B)
- Display of SERVOPACK and Servomotor ID (Fn01E)
- Fully-closed Loop Control
- Origin Setting (Fn020)
- Software Reset (Fn030)
- EasyFFT (Fn206)
- Online Vibration Monitor (Fn207)
- Chapter 7 Monitor Displays (Un )
- List of Monitor Displays
- Viewing Monitor Displays
- Monitoring Input Signals
- Input Signal Display Example
- Monitoring Output Signals
- Monitoring Safety Input Signals
- Chapter 8 Fully-closed Loop Control
- with Fully-closed Loop Control
- Internal Block Diagram of Fully-closed Loop Control
- Serial Converter Unit
- Example of Connections to External Encoders
- by Renishaw plc
- Precautions When Using an External Incremental Encoder by Magnescale
- SERVOPACK and Converter Startup Procedure
- Parameter Settings for Fully-closed Loop Control
- Motor Rotation Direction
- Sine Wave Pitch (Frequency) for an External Encoder
- External Absolute Encoder Data Reception Sequence
- Alarm Detection
- Analog Monitor Signal
- Troubleshooting
- Troubleshooting of Alarms
- Warning Displays
- the Servomotor
- Chapter 10 Appendix
- Parameters
- Parameter Recording Table
- Index

SGMVV
Table of contents
- Outline
- Table Of Contents
- Table Of Contents
- Table Of Contents
- Table Of Contents
- Table Of Contents
- Table Of Contents
- and Converters
- Part Names
- SERVOPACK Part Names
- Converter Part Names
- Ratings and Specifications of a Multi-Winding Drive System
- Basic Specifications
- Speed/Position/Torque Control
- Internal Block Diagrams
- Model Designations
- SERVOPACK Model Designation
- Combinations for Multi-Winding Drive Systems
- Chapter 2 Panel Operator
- Overview
- Status Display
- Utility Functions (Fn)
- Parameters (Pn)
- Setting Parameters
- Monitor Displays (Un)
- Wiring and Connection
- Main Circuit Wiring
- Main Circuit Wire
- Typical Main Circuit Wiring Examples
- General Precautions for Wiring
- Discharging Time of the Main Circuit's Capacitor
- Connecting the Converter to the SERVOPACK
- I/O Signal Connections
- SERVOPACK Safety Function Signal (CN8) Names and Functions
- Example of I/O Signal Connections in Speed Control
- Example of I/O Signal Connections in Position Control
- Example of I/O Signal Connections in Torque Control
- I/O Signal Allocations
- Output Signal Allocations
- Examples of Connection to Host Controller
- Sequence Input Circuit
- Sequence Output Circuit
- Local Communications Cable Connections
- Encoder Connection
- Selecting and Connecting a Regenerative Resistor Unit
- Connecting a Regenerative Resistor Unit
- Installation Standards
- Selecting and Connecting a Dynamic Brake Unit
- Setting the Dynamic Brake Unit
- Setting the Dynamic Brake Answer Function
- Noise Control and Measures for Harmonic Suppression
- Precautions on Connecting Noise Filter
- Connecting a Reactor for Harmonic Suppression
- Trial Operation
- Operation
- Trial Operation for Servomotor without Load from Host Reference
- Inspecting Connection and Status of Input Signals
- Adjustments
- Trial Operation under Position Control from the Host Controller with the Multi-Winding Drive Unit Used for Speed Control
- Trial Operation with the Servomotor Connected to the Machine
- Trial Operation of Servomotor with Brakes
- Chapter 5 Operation
- Control Method Selection
- Basic Functions Settings
- Servomotor Rotation Direction
- Overtravel
- Holding Brakes
- Stopping Servomotors after /S-ON Turned OFF or Alarm Occurrence
- Instantaneous Power Interruption Settings
- Setting Motor Overload Detection Level
- Speed Control
- Reference Offset Adjustment
- Soft Start
- Zero Clamp Function
- Encoder Output Pulses
- Setting Encoder Output Pulse
- Setting Speed Coincidence Signal
- Position Control
- Basic Settings for Position Control
- Clear Signal Setting
- Reference Pulse Input Multiplication Switching Function
- Electronic Gear
- Smoothing
- Positioning Completed Signal
- Positioning Near Signal
- Reference Pulse Inhibit Function
- Torque Control
- Torque Reference Filter
- Internal Set Speed Control
- Example of Operating with Internal Set Speeds
- Combination of Control Methods
- Switching Other Than Internal Set Speed Control (Pn000.1 = 7, 8 or 9)
- Limiting Torque
- External Torque Limit
- Torque Limiting Using an Analog Voltage Reference
- Torque Limiting Using an External Torque Limit and Analog Voltage Reference
- Checking Output Torque Limiting during Operation
- Absolute Encoders
- Connecting the Absolute Encoder
- Absolute Data Request Signal (SEN)
- Battery Replacement
- Absolute Encoder Setup and Reinitialization
- Absolute Data Reception Sequence
- Multiturn Limit Setting
- Multiturn Limit Disagreement Alarm (A.CC0)
- Other Output Signals
- Warning Output Signal (/WARN)
- Rotation Detection Output Signal (/TGON)
- Safety Function
- External Device Monitor (EDM1)
- Application Example of Safety Functions
- Confirming Safety Functions
- Chapter 6 Adjustments
- Type of Adjustments and Basic Adjustment Procedure
- Basic Adjustment Procedure
- Monitoring Operation during Adjustment
- Safety Precautions on Adjustment of Servo Gains
- Advanced Autotuning (Fn201)
- Procedure for Calculating the Moment of Inertia
- One-parameter Tuning (Fn203)
- One-parameter Tuning Procedure
- One-parameter Tuning Example
- Related Parameters
- Anti-Resonance Control Adjustment Function (Fn204)
- Anti-Resonance Control Adjustment Function Operating Procedure
- Vibration Suppression Function (Fn205)
- Vibration Suppression Function Operating Procedure
- Additional Adjustment Function
- Manual Adjustment of Friction Compensation
- Current Control Mode Selection Function
- Position Integral
- Compatible Adjustment Function
- Speed Feedforward
- Proportional Control
- Mode Switch (P/PI Switching)
- List of Utility Functions
- Alarm History Display (Fn000)
- JOG Operation (Fn002)
- Origin Search (Fn003)
- Program JOG Operation (Fn004)
- Initializing Parameter Settings (Fn005)
- Clearing Alarm History (Fn006)
- Offset Adjustment of Analog Monitor Output (Fn00C)
- Gain Adjustment of Analog Monitor Output (Fn00D)
- Write Prohibited Setting (Fn010)
- Servomotor Model Display (Fn011)
- Software Version Display (Fn012)
- Vibration Detection Level Initialization (Fn01B)
- Display of Multi-Winding Drive Unit and Servomotor ID (Fn01E)
- EasyFFT (Fn206)
- Online Vibration Monitor (Fn207)
- List of Monitor Displays
- Viewing Monitor Displays
- Reading 32-bit Data in Decimal Displays
- Monitoring Input Signals
- Input Signal Display Example
- Monitoring Output Signals
- Output Signal Display Example
- Monitoring Safety Input Signals
- Safety Input Signal Display Example
- Troubleshooting
- Troubleshooting of Alarms
- Warning Displays
- the Servomotor
- Chapter 10 Appendix
- Connection to Host Controller
- Connection to MP920 Servo Module SVA-01A
- Connection to OMRON's Motion Control Unit
- Connection to OMRON's Position Control Unit
- List of Parameters
- Parameters
- Parameter Recording Table
- Index
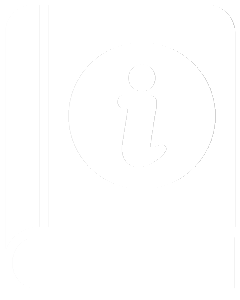
manualsdatabase
Your AI-powered manual search engine