Panasonic FP0H Series manuals

FP0H Series
Table of contents
- safety precautions
- Table Of Contents
- Table Of Contents
- Table Of Contents
- Table Of Contents
- Unit Functions and Restrictions on Combination
- Unit Functions and Features
- Restrictions on Communication Functions to be Used
- Overview of Communication Functions
- MEWTOCOL Master / Slave Communication
- MODBUS RTU Master / Slave Communication
- General-Purpose Communication
- Wiring of COM Port
- Installation of an Extension (Communication) Cassette
- Wiring of the COM Port Terminal Block
- Applicable Cable
- Wiring Method
- Wiring of the Control Unit (GT Power Supply, COM0 Port)
- Terminal Layout Diagrams and Wiring Examples
- Wiring of COM Port of a Communication Cassette
- AFP0HCCS2 (RS-232C 2ch Non-Insulated Type)
- AFP0HCCM1 (RS-485 1ch Insulated Type)
- AFP0HCCS1M1 (RS-485 1ch insulated + RS-232C 1ch Non-Insulated Type)
- Setting and Confirmation of Communication
- Setting of Purpose and Communication Conditions
- Communication Conditions Settings
- Settings Using a Program
- PLC link
- Operation of PLC Link MEWNET-W0
- Roles of Link Relays and Link Registers
- Setting Items for PLC Link
- Memory Block No. of Link Relays and Link Registers to be Used
- Link Relay Transmission Start Number and Sending Size
- Link Register Transmission Start Number and Sending Size
- Response Time of PLC Link
- Response Time when There are Units that have not been Added to the Link
- MEWTOCOL Master-Slave Communication
- List of MEWTOCOL Supported Commands
- MEWTOCOL-COM Master Communication (RECV)
- MEWTOCOL-COM Master Communication (SEND)
- MODBUS RTU Master-Slave Communication
- List of MODBUS RTU Supported Commands
- MODBUS RTU Master Communication (RECV)
- MODBUS RTU Master Communication (SEND)
- Overview of Sending Data
- Send Data Area
- Receiving Data from External Devices
- Receive data area
- Flag Operations in Transmission / Reception
- When the Header is Set to "STX" and the Terminator to "ETX"
- Instruction References
- List of Instructions
- Communication Instruction
- F145 SEND] Data Transmission (MEWTOCOL-COM Master)
- F146 RECV] Data Reception (MEWTOCOL-COM Master)
- F145 SEND] Data Transmission (MODBUS Master: Function Code Specification)
- F146 RECV] Data Reception (MODBUS Master: Function Code Specification)
- F145 SEND] data transmission (MODBUS master)
- F146 RECV] Data Reception (MODBUS Master)
- F159 MTRN] Serial Data Send / Receive Instruction
- Character String Instructions
- Troubleshooting
- What to Do If an Error Occurs
- Communication Error (RS-485)
- Specifications
- Communication Function Specifications
- Communication Cassette Specifications
- List of System Data Registers
- List of Special Relays (COM Communication)
- List of Special Data Registers (COM Communication)
- Error Codes Table
- MEWTOCOL-COM Format
- MEWTOCOL-COM Response Format
- MODBUS RTU Format
- MODBUS RTU Response Format

FP0H Series
Table of contents
- Table Of Contents
- Table Of Contents
- Table Of Contents
- Table Of Contents
- Table Of Contents
- Table Of Contents
- Functions of Unit and Restrictions on Combination
- Functions of Unit
- Compatibility Function with FPΣ
- Restrictions on Combinations and Functions
- Comparison of Pulse Output Function
- Comparison of Two Control Modes
- Wiring
- Connections with Servo Motor Amplifier
- Precautions on Connection
- Connection with Stepping Motor Driver
- Power ON and OFF, and Items to Check
- Safety Circuit Design
- Before Turning On the Power
- Procedure for Turning On the Power
- Confirming while the Power is ON
- Checking the installation of the external safety circuit
- Checking the Operation of the Near Home Switch and Home Switch
- Settings of Control Unit
- Confirming I/O Allocation
- When Using PWM Output Function
- When Using High-speed Counter Function
- Settings in Configurator PMX
- Setting Parameters
- Creating Positioning Data Table
- Saving Positioning Parameters
- Check on Parameter Data
- Writing Parameters to Unit (2)
- System Register Settings
- Reading Elapsed Values
- Operation Patterns
- Stop Operation
- Characteristics of Stop Operations
- JOG Operation
- Settings and Operations of JOG Operation (Speed Changes)
- Speed Changes in JOG Operation
- Home Return
- Operation Patterns of Home Return
- Settings and Operations of Home Return
- Positioning Control
- E-point Control (First Speed Positioning)
- P-point Control (Second Speed Positioning)
- C-point Control
- J-point Control (JOG Positioning Control)
- J-point Control (JOG Positioning: Speed Changes)
- Programming cautions
- Repeat Operation
- Settings and Operations of Repeat Operation
- Stop Operation During Repeat Operation
- Linear interpolation control
- Settings and Operations of Linear Interpolation
- Operating Characteristics
- Operational Difference Between Parameters
- Operation Patterns and Start Speed Settings
- Other Characteristics
- Instruction References
- Table Setting Mode Control Instruction
- F381 JOGST] JOG operation start instruction
- F382 ORGST] Home return start instruction
- F383 MPOST] Positioning table simultaneous start instruction
- F384 PTBLR] Positioning parameter read instruction
- F385 PTBLW] Positioning parameter write instruction
- FPΣ Compatible Instruction Mode Control Instruction
- F171(SPDH)] Pulse Output (Home Return)
- F172(PSLH)] Pulse Output (JOG Operation)
- F175(SPSH)] Pulse Output (Linear Interpolation)
- Self-diagnostic Function
- Operation Mode When an Error Occurs
- What to Do If an Error Occurs
- What to Do When Positioning Error Occurs
- Motor Does Not Rotate/Move (Output LED Flashes or is ON)
- PWM Output Function
- F173 PWMH] PWM Output Instruction (Frequency Specification)
- F173 PWMH] PWM Output Instruction (Control Code Specification)
- High-speed Counter Function
- Overview of High-speed Counter Function
- Areas Used For High-speed Counter Function
- Input Mode Type
- Minimum Input Pulse Width
- High-speed Counter Instruction
- F1 DMV] Elapsed Value Write / Read Instruction
- Sample Program (Upper Limit Control, Subtraction)
- Interrupt Program Activation
- Interrupt Activation When F165 (CAM0) is Executed
- FPΣ Mode
- Converting Projects for FPΣ to Projects for FP0H (FPΣ Mode)
- Converting Projects for FP0H (FPΣ Mode) to Projects for FP0H (FP0H Mode)
- Differences in Positioning Instructions with FPΣ
- High-speed Counter Instructions F165 (CAM0), F166 (HC1S), F167 HC1R)
- Pulse/PWM Output Control Instructions
- Specifications
- Allocation of Memory Areas
- Positioning Memory
- Common area (Memory Area No. 0)
- Axis Information Area (Memory Area No. 1)

FP0H Series
Table of contents
- Table Of Contents
- Table Of Contents
- Table Of Contents
- Overview of Logging/Trace Function
- For Using Logging/Trace Function
- Selection of SD Memory Cards
- Overview of Functions
- Overview of Trace Function
- Format of Saved Files
- File Format (For Trace Function)
- Data Format
- Configuration of Logging/Trace Function
- Definition of Buffer Memory
- Logging Information Setting
- LOG File Setting Items (For Logging)
- Trace Information Setting
- LOG File Setting Items (For Trace)
- Registration of Device Information
- Operation When Setting Cycle for Logging Trigger
- Downloading Setting Data to Control Unit
- Logging/Trace Start, Stop and Monitor
- Start and Stop of Logging/Trace Operation
- Start and Stop by Instructions
- Operation Check Using Logging/Trace Monitor
- Special Internal Relays Relating to Logging/Trace Operation
- Special Data Registers Relating to Logging/Trace Operation
- Checking Logging Speed (When Selecting Logging For Application)
- Logging Operation
- Flow of Logging Operation
- Operation When Logging is Selected for Application
- Operation When the Battery Cover of Control Unit is Open
- Operation When the Number of Determination Files Reaches the Maximum Number of Generations
- System Management Information Relating to Logging Function
- Trace Operation and Time Chart
- Flow of Trace Operation
- Operation When Trace is Selected for Application
- Trace Monitor (Time Chart)
- Explanation of Time Chart Monitor
- Settings for Time Chart Display Area
- Register Device
- Sampling Condition Setting
- Logging/Trace Troubleshooting
- Operations When Errors Occur
- Operations When Inserting/Removing SD Memory Card During Logging/Trace
- Troubleshooting
- Errors When Operation was Executed Using LOGST, LOGED or LOGSMPL Instruction
- Sampling Trace Function
- How to Use Sampling Trace

FP0H Series
Table of contents
- safety precautions
- Table Of Contents
- Table Of Contents
- Table Of Contents
- Table Of Contents
- FP0H EtherNet/IP Function
- What is EtherNet/IP?
- Names and Functions of Parts
- LED Displays When PLC Operates
- Restrictions
- Cyclic Communication
- Cyclic Communication Function
- Operation of Cyclic Communication
- Data Refresh of Cyclic Communication
- Data Area Specifications Using Tag/Instance
- Cyclic Communication of FP0H
- Connection Using FP0H as Target
- Example of Configuration When FP0H is Originator and Target
- Setting Procedure
- Overview of Settings
- Initial Setting of Ethernet /IP
- Starting EtherNet/IP Setting Screen
- EtherNet/IP Basic Configuration
- Items of Ethernet /IP Basic Configuration
- Settings of Connection Using FP0H as Originator
- Registering EDS File of Target Device
- Adding Target in Scan List
- Setting IP Address of Target
- Setting Tag/Instance
- Specifying Data Area Corresponding to Tag/Instance
- Reference: Setting of Target [FP0H(B)]
- Settings of Connection Using FP0H as Target
- Adding I/O Map to Scan List
- Registering Tag Name/Instance ID
- Registering Data Area Corresponding to Tag/Instance
- Reference: Setting of Originator [FP7]
- Confirmation of Load Factor Calculation
- Saving EtherNet/IP Settings
- Writing EtherNet/IP Settings to FP0H
- Tool Operation
- Scan List Window
- Operations in Scan List Window
- Device List Window
- Operations from EDS File Menu
- Various Setting Screens
- Operations in Connection Setting Screen
- Operations in I/O Map Setting Screen
- Display Contents of Calculate Load Factor Screen
- Display Contents of Device Property Screen
- Switching Tabs in Each Setting Screen
- Startup and Operation
- Startup Operation of Cyclic Communication
- When FP0H is Target
- Checking EtherNet/IP Communication State
- RUN/IDLE Bit
- Judgement and Operation of Abnormality
- Delay Time of Communication Data
- Delay Time of Reception Data
- Instruction References
- High-level Instructions Used for EtherNet/IP Control
- flag operation
- Reference Information
- Calculation Method of Load Factor
- Cyclic Communication: List of Abnormal Statuses
- PLC Link and Ethernet Switch
- Appendix
- Supported Data Types
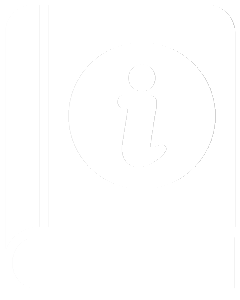
manualsdatabase
Your AI-powered manual search engine