ABB ACS 800 Series manuals

ACS 800 Series
Table of contents
- What this Chapter Contains
- Installation and Maintenance Work
- Operation
- Permanent Magnet Motor
- Table Of Contents
- Table Of Contents
- Table Of Contents
- Contents
- Installation and Commissioning Flowchart
- Inquiries
- Type Code
- Product Ordering — Special Note
- Before Installation
- Fastening the Cabinet to the Floor and Wall
- Electric Welding
- Permanent Magnet Synchronous Motor
- Thermal Overload and Short-Circuit Protection
- Emergency Stop Devices
- Prevention of Unexpected Start (ACS800-07/U7 only)
- Selecting the Power Cables
- Power Factor Compensation Capacitors
- Equipment Connected to the Motor Cable
- Disturbances in Case of Inductive Loads
- Selecting the Control Cables
- Connection of a Motor Temperature Sensor to the Drive I/O
- Electrical Installation
- Checking the Insulation of the Assembly
- Example Wiring Diagram
- Power Cable Connection Diagram
- Connecting the Power Cables
- Connecting the Control Cables
- Installation of Optional Modules
- Layout Drawing of Factory Installed Optional Equipment
- RMIO board specifications
- Checklist
- Start-Up Procedure
- Checking and Replacing the Air Filters
- Exhaust Filter for UL Type 12
- Heatsink
- Replacing the Cabinet Fan
- Layout of the Drive Module
- Capacitors
- Replacing the Drive Module
- LEDs
- Free Space Around the Unit
- Input Power Connection
- Cooling
- Materials
- CE Marking
- Equipment Warranty and Liability
- Dimensional Drawings
- ACS800-PC and ACS800-07/U7
- Brake Circuit Commissioning

ACS 800 Series
Table of contents
- ACS800-07 manuals
- What this chapter contains
- Installation and maintenance work
- Grounding
- Operation
- Permanent magnet motor drives
- Table Of Contents
- Table Of Contents
- Table Of Contents
- Table Of Contents
- Table Of Contents
- Table Of Contents
- Table Of Contents
- Table of contents
- Contents
- Installation and commissioning flowchart
- Terms and abbreviations
- Single-line circuit diagram of the drive, example 1
- Single-line circuit diagram of the drive, example 2
- Layout drawing, example 1
- Layout drawing, example 2
- Swing-out frame
- Power connections and control interfaces of the drive
- Controls of the inverter unit (and motor)
- Controls of the supply unit
- Control panel
- Fieldbus
- Type designation
- Moving the unit
- by fork-lift or pallet truck
- Final placement of the unit
- Before installation
- Installation procedure
- Fastening the cabinet to the floor (Non-marine units)
- Holes inside the cabinet
- Fastening the unit to the floor and wall (Marine units)
- Joining the shipping splits
- Connecting the DC busbars and the PE busbar
- DC busbars
- Miscellaneous
- Cooling air intake through bottom of cabinet
- Electric welding
- Protecting the motor insulation and bearings
- Permanent magnet synchronous motor
- Thermal overload and short-circuit protection
- Ground fault protection
- Prevention of unexpected start-up
- Safe torque off
- Selecting the power cables
- Alternative power cable types
- Conduit
- Power factor compensation capacitors
- Before opening an output contactor (in the DTC motor control mode)
- Selecting the control cables
- Connection of a motor temperature sensor to the drive I/O
- Routing the cables
- Electrical installation
- Motor and motor cable
- or main breaker (no option +F253 or +F255)
- Twelve-pulse connection, two DSU modules in parallel
- Connection procedure
- Phase 2 – Installing the cables
- Phase 3 – Replacing the module
- Use of the dual-cable screw lug connector
- or main breaker (option +F253 or +F255)
- Motor connection – Units without common motor terminal cubicle (no option +H359)
- Motor connection – Units with common motor terminal cubicle (option +H359)
- Control connections
- Installation of optional modules and PC
- Connections and tap settings of the auxiliary voltage transformer of the drive
- voltage transformer of the DSU module
- External control connections (non-US)
- External control connections (US)
- RMIO board specifications
- Relay outputs
- Installation checklist
- Start-up procedure
- Connecting voltage to input terminals and auxiliary circuit
- Setting up the supply unit control program
- Redundancy (Reduced run capability)
- Removing an inverter module and selecting the Reduced run feature
- Replacing the PPCS branching unit (APBU-xx) memory backup battery
- Checking and replacing the air filters
- Cooling fans
- Replacing the fan of the inverter and brake module
- Replacing the fans in the auxiliary control cubicle
- Replacing the fan in the incoming cubicle with the main breaker (option +F255)
- Replacing the additional fans in the IP54 / UL type 12 drives (+B055 and +B059)
- Heatsinks
- Safety function checks in the maintenance routine
- Other LEDs of the drive
- Symbols
- ACS800-07 (+V992) frame sizes and power module types
- AC fuses
- DC fuses at inverter module input
- Input power connection
- Motor connection
- Efficiency
- Cooling
- Materials
- Applicable standards
- CE marking
- Second environment (PDS of category C3)
- C-tick" marking
- Second environment
- Cabinet line-ups
- D4 + 2×R8i
- D4 + 4×R8i
- D4 + 6×R8i
- Frame size 1×D4 + 2×R8i
- Frame size 1×D4 + 2×R8i (with a main switch-disconnector +F253)
- Frame size 1×D4 + 2×R8i (with top entry/exit)
- Frame size 2×D4 + 2×R8i
- Frame size 2×D4 + 2×R8i (with a main switch-disconnector +F253)
- Frame size 2×D4 + 3×R8i
- Frame size 2×D4 + 3×R8i (with a main switch-disconnector +F253)
- Frame size 2×D4 + 3×R8i (with a main breaker +F255)
- Frame size 3×D4 + 4×R8i (with a main switch-disconnector +F253)
- Frame size 3×D4 + 4×R8i (with a main breaker +F255)
- Common motor terminal cubicle
- Chopper/Resistor combinations – Technical data
- Verifying the capacity of the braking equipment
- Calculating the maximum braking power (P br )
- Example 3
- Custom resistor installation and wiring
- Brake circuit commissioning
- Product training

ACS 800 Series
Table of contents
- ACS800 Single Drive Manuals
- What this chapter contains
- Installation and maintenance work
- Grounding
- Mechanical installation and maintenance
- Printed circuit boards
- Operation
- Permanent magnet motor
- Table Of Contents
- Table Of Contents
- Table Of Contents
- Table Of Contents
- Table Of Contents
- Table Of Contents
- Contents
- Installation and commissioning flowchart
- Product and service inquiries
- Type code
- Main circuit and control
- Unpacking the unit
- Delivery check
- Free space around the unit
- Mounting the drive on the wall
- Cabinet installation
- Unit above another
- Protecting the motor insulation and bearings
- Requirements table
- Permanent magnet synchronous motor
- Supply connection
- Thermal overload and short-circuit protection
- Protection against short-circuit inside the drive or in the supply cable
- Ground fault protection
- Selecting the power cables
- Alternative power cable types
- Additional US requirements
- Equipment connected to the motor cable
- Protecting the relay output contacts and attenuating disturbances in case of inductive loads
- Selecting the control cables
- Connection of a motor temperature sensor to the drive I/O
- Control cable ducts
- Checking the insulation of the assembly
- Connecting the power cables
- Conductor stripping lengths
- Wall installed units (US version)
- Warning sticker
- Frame size R5
- Frame size R6
- Connecting the control cables
- degrees grounding
- Cabling of I/O and fieldbus modules
- Fastening the control cables and covers
- Circuit diagram
- Dimensional drawing
- AGPS-11C board specifications
- External control connections (non-US)
- External control connections (US)
- RMIO board specifications
- Relay outputs
- Checklist
- Heatsink
- Fan replacement (R4)
- Fan replacement (R5)
- Fan replacement (R6)
- Replacement (R4, R5)
- LEDs
- Symbols
- Derating
- Frame sizes R5 and R6
- Fuse tables for frame sizes R5 and R6
- Ultrarapid (aR) fuses
- Quick guide for selecting between gG and aR fuses
- Cable types
- Cable entries
- NEMA data
- Fuses
- Input power connection
- Cooling
- Materials
- CE marking
- Second environment (drive of category C3)
- C-tick" marking
- UL/CSA markings
- Frame size R2 (IP 21, UL type
- Frame size R6 (IP 21, UL type 1), -205-3 and -255-5 units
- Dimensional drawings (USA)
- Selecting the correct drive/chopper/resistor combination
- Resistor installation and wiring
- Protection of frame sizes R2 to R5 (ACS800-01/U1)
- Brake circuit commissioning
- Connecting +24 V external power supply


ACS 800 Series
Table of contents
- ACS800 Single Drive Manuals
- What this chapter contains
- Installation and maintenance work
- Grounding
- Mechanical installation and maintenance
- Printed circuit boards
- Operation
- Permanent magnet motor
- Table Of Contents
- Table Of Contents
- Table Of Contents
- Table Of Contents
- Table Of Contents
- Table Of Contents
- Contents
- Installation and commissioning flowchart
- Inquiries
- Terms
- AC voltage and current waveforms
- Main circuit and control interfaces diagram
- Fieldbus control of the line-side converter
- Connection diagram of the RMIO board in the line-side converter
- Type code
- Unpacking the unit
- Moving the unit
- Before installation
- Mounting the drive on the wall
- Preventing cooling air recirculation
- Unit above another
- Protecting the motor insulation and bearings
- Requirements table
- Permanent magnet synchronous motor
- Supply connection
- Thermal overload and short-circuit protection
- Short-circuit protection
- Ground fault protection
- Prevention of Unexpected Start
- Selecting the power cables
- Alternative power cable types
- Additional US requirements
- Equipment connected to the motor cable
- Protecting the relay output contacts and attenuating disturbances in case of inductive loads
- Selecting the control cables
- Connection of a motor temperature sensor to the drive I/O
- Control cable ducts
- IT (ungrounded) systems
- Connecting the power cables
- Conductor stripping lengths
- Wall installed units (US version)
- Warning sticker
- Connecting the control cables
- degrees grounding
- Cabling of I/O and fieldbus modules
- Fastening the control cables and covers
- Circuit diagram
- Dimensional drawing
- Note on external power supply
- External control connections (non-US)
- External control connections (US)
- RMIO board specifications
- Relay outputs
- Control panel
- To control the motor-side converter
- Parameters
- ACS800-31/U31 specific parameters in the IGBT Supply Control Program
- AUTOMATIC RESET
- Fixed parameters with the ACS800-31 and ACS800-U31
- Heatsink
- Fan replacement (R5, R6)
- Replacement (R6)
- IEC data
- Symbols
- Mains cable fuses
- Cable types
- NEMA data
- Input cable fuses
- Input power connection
- Motor connection
- Ambient conditions
- Materials
- CE marking
- Second environment (drive of category C3)
- C-tick" marking
- UL/CSA markings
- Dimensional drawings
- Frame size R5 (IP21, UL type open, UL type 1)
- Frame size R6 (IP21, UL type open, UL type 1)
- External brake chopper and resistor(s) for the ACS800-31/U31
- Brake chopper and resistor installation
- Brake circuit commissioning
- Connecting +24 V external power supply
- RMIO board of the line-side converter

ACS 800 Series
Table of contents
- ACS800 Single Drive Manuals
- What this chapter contains
- Installation and maintenance work
- Grounding
- Operation
- Permanent magnet motor drives
- Table Of Contents
- Table Of Contents
- Table Of Contents
- Table Of Contents
- Table Of Contents
- Table Of Contents
- Installation and commissioning flowchart
- Product and service inquiries
- Terms and abbreviations
- Swing-out frame
- Cabling direction
- Single-line circuit diagram of the drive
- Controls
- Supply unit control electronics
- Reading and setting of values (page 1 of
- Terminal blocks
- Digital input and relay output terminals
- Emergency stop input
- Earth (ground) current function
- Power loss ride-through function
- Motor control
- Type code
- Moving the unit
- by fork-lift or pallet truck
- Final placement of the unit
- Before installation
- Installation procedure
- Fastening the cabinet to the floor (Non-marine units)
- Holes inside the cabinet
- Fastening the unit to the floor and wall (Marine units)
- Joining the shipping splits
- Connecting the DC busbars and the PE busbar
- DC busbars
- Miscellaneous
- Cooling air intake through bottom of cabinet
- Electric welding
- Protecting the motor insulation and bearings
- Requirements table
- Permanent magnet synchronous motor
- Thermal overload protection of the motor
- Emergency stop devices
- Alternative power cable types
- Conduit
- Power factor compensation capacitors
- Relay output contacts and inductive loads
- Selecting the control cables
- Connection of a motor temperature sensor to the drive I/O
- Control cable ducts
- Electrical installation
- IT (ungrounded) systems
- Input power connection – Units without load switch-disconnector or air circuit breaker
- pulse connection, two supply modules in parallel
- Connection procedure
- Use of the dual-cable screw lug connector
- Input power connection – Units with load switch-disconnector or air circuit breaker
- Motor connection – Units without common motor terminal cubicle
- Motor connection – Units with common motor terminal cubicle
- Control connections
- Installation of optional modules and PC
- Connections and tap settings of the auxiliary voltage transformer
- Note on external power supply
- External control connections (non-US)
- External control connections (US)
- RMIO board specifications
- Relay outputs
- Installation checklist
- Start-up procedure
- Starting the supply unit
- Maintenance intervals
- Replacing the PPCS branching unit (APBU-xx) memory backup battery
- Checking and replacing the air filters
- Cooling fans
- Inverter module fan replacement
- Control and I/O cubicle cooling fans
- Air circuit breaker cubicle fans
- Heatsinks
- Other LEDs of the drive
- Symbols
- ACS800-07 frame sizes and power module types
- Internal AC fuses
- DC fuses at inverter module input
- Input power connection
- Motor connection
- Efficiency
- Cooling
- Materials
- CE marking
- Second environment
- C-tick" marking
- Cabinet line-ups
- Frame size 1×D4 + 2×R8i
- Frame size 1×D4 + 2×R8i (with load switch-disconnector)
- Frame size 1×D4 + 2×R8i (with top entry/exit)
- Frame size 2×D4 + 2×R8i
- Frame size 2×D4 + 2×R8i (with load switch-disconnector)
- Frame size 2×D4 + 3×R8i
- Frame size 2×D4 + 3×R8i (with load switch-disconnector)
- Frame size 2×D4 + 3×R8i (with air circuit breaker)
- Frame size 3×D4 + 4×R8i
- Frame size 3×D4 + 4×R8i (with load switch-disconnector)
- Frame size 3×D4 + 4×R8i (with air circuit breaker)
- Common motor terminal cubicle
- Chopper/Resistor combinations – Technical data
- Verifying the capacity of the braking equipment
- Calculating the maximum braking power (P br )
- Example 3
- Custom resistor installation and wiring
- Brake circuit commissioning

ACS 800 Series
Table of contents
- ACS800 Single Drive Manuals
- What this chapter contains
- Installation and maintenance work
- Grounding
- Mechanical installation and maintenance
- Printed circuit boards
- Operation
- Permanent magnet motor
- Table Of Contents
- Table Of Contents
- Table Of Contents
- Table Of Contents
- Table Of Contents
- Table Of Contents
- Installation and commissioning flowchart
- Product and service inquiries
- Enclosure extension
- Main circuit and control
- Protecting the motor insulation and bearings
- Requirements table
- Permanent magnet synchronous motor
- Supply connection
- Thermal overload and short-circuit protection
- Protection against short-circuit inside the drive or in the supply cable
- Ground fault protection
- Power-loss ride-through function
- Prevention of Unexpected Start
- Selecting the power cables
- Alternative power cable types
- Additional US requirements
- Equipment connected to the motor cable
- Protecting the relay output contacts and attenuating disturbances in case of inductive loads
- Selecting the control cables
- Connection of a motor temperature sensor to the drive I/O
- Control cable ducts
- Before installation
- Requirements for the installation site
- IT (ungrounded) systems
- Power cable connection diagram
- Installation procedure
- Mounting orientation c (lifting from above)
- Mounting orientation d (optional enclosure extension included)
- Connecting the power cables
- Enclosure extension layout
- Main wiring diagram
- Routing the control/signal cables inside the cubicle
- Units with enclosure extension
- Connecting the control cables
- Settings of the cooling fan transformer
- Pulse encoder module cabling
- Fill-in user connections diagram
- Wiring diagram template
- Note on external power supply
- External control connections (non-US)
- External control connections (US)
- RMIO board specifications
- Relay outputs
- Checklist
- Layout
- Heatsink
- Replacing the fan(s) of the enclosure extension
- Replacing the fan (R7)
- Replacing the fan (R8)
- Capacitors
- Replacing the capacitor pack (R8)
- Module replacement of units with the enclosure extension
- LEDs
- Symbols
- Fuses
- Fuse tables
- gG fuses
- Quick guide for selecting between gG and aR fuses
- Cable types
- Cable entries
- NEMA data
- Input power connection
- Cooling
- Materials
- CE marking
- Second environment (drive of category C3)
- C-tick" marking
- UL/CSA markings
- Dimensional drawings
- Frame size R7
- Frame size R8
- Frame size R7 with enclosure extension – bottom entry
- Frame size R7 with enclosure extension – top entry
- Frame size R8 with enclosure extension – bottom entry
- Frame size R8 with enclosure extension – top entry
- Optional brake chopper and resistor(s) for the ACS800-01/U1
- ACS800-07/U7
- Resistor installation and wiring

ACS 800 Series
Table of contents
- Table Of Contents
- Table Of Contents
- Chapter overview
- Related publications
- How to build the program
- How to connect the program to the drive application
- Parameter value as an integer input
- Constant as an integer input
- Parameter value as a boolean input
- Constant as a boolean input
- Function blocks
- BITWISE
- COUNT
- DPOT
- MASK-SET
- MULDIV
- PI-BAL
- PI-BIPOLAR
- SWITCH-B
- SWITCH-I
- TRIGG
- Parameters

ACS 800 Series
Table of contents
- ACS800 Single Drive Manuals
- What this chapter contains
- Installation and maintenance work
- Grounding
- Mechanical installation and maintenance
- Operation
- Permanent magnet motor
- Table Of Contents
- Table Of Contents
- Table Of Contents
- Table Of Contents
- Table Of Contents
- Table Of Contents
- Contents
- Installation and commissioning flowchart
- Product and service inquiries
- Terms and abbreviations
- Type code
- Main circuit and control
- Free space around the unit
- Cooling and degrees of protection
- Preventing the recirculation of hot air
- Inside the cabinet
- Cabinet heaters
- Control panel mounting platform kit (RPMP)
- Unpacking the unit
- Delivery check
- Installation procedure
- Flange mounting
- Protecting the motor insulation and bearings
- Requirements table
- Permanent magnet synchronous motor
- EEA / Europe
- Thermal overload protection of the motor
- Ground fault protection
- Prevention of Unexpected Start
- Selecting the power cables
- Alternative power cable types
- Additional US requirements
- Power factor compensation capacitors
- Before opening a contactor (DTC control mode selected)
- Selecting the control cables
- Connection of a motor temperature sensor to the drive I/O
- Control cable ducts
- IT (ungrounded) systems
- Power cable connection
- Grounding the motor cable shield at the motor end
- Frame sizes R2 to R4
- Power cable protection
- Frame size R6
- Connecting the control cables
- degrees grounding
- Cabling of I/O and fieldbus modules
- Installation of optional modules and PC
- Prevention of Unexpected Start, AGPS board
- External control connections (non-US)
- External control connections (US)
- RMIO board specifications
- Relay outputs
- Checklist
- Fan replacement (R2, R3)
- Fan replacement (R4)
- Fan replacement (R5)
- Fan replacement (R6)
- Replacement (R4, R5)
- Symbols
- Derating
- Fuses
- Frame sizes R5 and R6
- Calculation example
- gG fuses
- Ultrarapid (aR) fuses
- Quick guide for selecting between gG and aR fuses
- Cable types
- Cable entries
- NEMA data
- Motor connection
- AGPS-11C
- Materials
- CE marking
- Second environment (drive of category C3)
- C-tick" marking
- UL/CSA markings
- Product protection in the US
- Frame size R2 (with optional control panel)
- Frame size R3 (with optional control panel)
- Frame size R4 (with optional control panel)
- Frame size R5 (with optional control panel)
- Frame size R6 (with optional control panel)
- Flange mounting kits
- Flange mounting kit for frame size R2
- Flange mounting kit for frame size R3
- Flange mounting kit for frame size R4
- Flange mounting kit for frame size R5
- Flange mounting kit for frame size R6
- AGPS board
- Optional brake chopper and resistor(s)
- Resistor installation and wiring
- Protection of frame sizes R2 to R5
- Protection of frame size R6

ACS 800 Series
Table of contents
- ACS800 Single Drive Manuals
- Table Of Contents
- Table of contents
- What this chapter contains
- Mechanical installation and service
- Filter selection
- Filter selection table
- Maximum values table
- Free space around the filter
- Tightening torques
- Electrical installation
- Connections to input terminals U1. V1, W1
- Ambient conditions
- Dimensional drawings
- FOCH0260-70
- FOCH0320-50 and FOCH0610-70

ACS 800 Series
Table of contents
- Overview
- Table Of Contents
- Table Of Contents
- Table Of Contents
- Table of contents
- What this chapter contains
- Motor cable length
- ACS800-01 and sine filters
- ACS800-02 and sine filters
- Motor cabling
- Rating table for ACS800-02 drives with a sine filter
- ACS800-04 and sine filters
- ACS800-07 and sine filters
- ACS800-11 and sine filters
- ACS800-17 and sine filters
- ACS800-31 and sine filters
- ACS800-37 and sine filters
- Cable type
- Transformer dimensioning
- Secondary side
- Example
- Transformer specification sheet
- Parameter settings before use
- NSIN0006-5...NSIN0140-5, NSIN0011-7...NSIN0120-7
- IP23
- Photographs
- IP23, cover removed (example)
- NSIN0210-6, NSIN0315-6, NSIN0485-6 for ACS800-02/04
- Dimensional drawing – choke module
- Installation example
- NSIN0900-6, NSIN1380-6 for ACS800-02/04
- Cooling fan wiring
- Dimensional drawing – choke module (NSIN0900-6)
- Dimensional drawing – choke module (NSIN1380-6)
- Installation example (NSIN0900-6)
- Installation example (NSIN1380-6)
- ACS800-07 with NSIN0210-6 or NSIN0315-6
- ACS800-07 with NSIN0315-6 and EMC filter +E202
- ACS800-07 with NSIN0485-6
- ACS800-07 with NSIN0485-6 and EMC filter +E202
- ACS800-07 with NSIN0900-6 or NSIN1380-6
- ACS800-07 with NSIN0900-6 and EMC filter +E202

ACS 800 Series
Table of contents
- Table Of Contents
- Table Of Contents
- Table Of Contents
- Table Of Contents
- Table Of Contents
- Table Of Contents
- What this chapter contains
- Related publications
- Terms and abbreviations
- Inverter module hardware
- Cabinet layout
- Frames R6i and R7i
- Frame R8i and multiples
- Module layout
- Control interfaces
- Type code
- Frame R2i to R5i
- Layout examples
- Installation without mounting plate 64138375
- Single R8i module in a Rittal TS 8 cubicle
- Two R8i modules in a Rittal TS 8 cubicle
- Three R8i modules in a Rittal TS 8 cabinet
- Three R8i modules side by side
- Checking the insulation of the assembly
- Power connections – Frame R2i to R5i
- Conductor stripping lengths
- Frame R2i to R4i power connections
- Frame R5i power connections
- Power connections – Frames R6i and R7i
- DC and motor connections
- Installation of common mode filters
- Power connections – Frame R8i and multiples
- Charging circuit
- Direct motor cabling
- Common motor terminal cubicle
- Control connections
- Frame R5i
- Frame R6i, R7i, R8i and multiples
- R6i/R7i connectors
- R8i connectors
- degrees grounding of I/O cables
- Cabling of I/O and fieldbus modules
- Installation of optional modules and PC
- Installation of NLMD-01 LED Monitoring Display
- Wiring
- Earthing
- Connecting +24 V external power supply
- Checklist
- External control connections (non-US)
- External control connections (US)
- RMIO board specifications
- Relay outputs
- Maintenance intervals
- Cooling fans
- Fan replacement (R5i)
- Fan replacement (R8i)
- Power connections (R8i)
- Frame size R8i and multiples
- DC fuses and fuse bases; DC switch fuses
- Inclined mounting plates for R2i to R5i modules
- Installation parts for R8i modules
- DC busbar kits
- Upper and lower guides
- Cabinet ventilation kits
- PPCS branching units for n×R8i inverter units
- Symbols
- Dimensions, noise, DC capacitance
- Power loss and cooling characteristics
- Cable terminals
- Efficiency
- Materials
- Auxiliary power consumptions
- R4i – Block diagram
- R5i – Block diagram
- Example – Three frame R2i to R5i inverter units
- Frame R6i and R7i
- R6i – Charging circuit
- R7i – Charging circuit
- I/O and control
- Cooling fan control (inverter modules without optional speed-controlled fan)
- Example – Emergency stop (Category 1)
- Example – Prevention of unexpected start
- Frame R2i
- Mounting plate (vertical)
- Airflow guide for vertical mounting
- Mounting plate (inclined)
- Frame R3i
- Frame R4i
- Main dimensions and clearances of module (including fan)
- Cooling fan dimensions
- Mounting plate (Kit #64138375)
- Combined mounting plate/air baffle
- Frame R8i
- Quick connector chassis socket kits
- Kit #68239435
- Kit #68242231
- Module guiding parts
- Rear upper guide
- Lower guide
- Crossmembers
- Front crossmember, 3 modules side by side (included in kit #68259541)
- Rear crossmember, 3 modules side by side (included in kit #68259541)
- Fuse/Fuse switch mounting plates
- Mounting plate, two R8i modules in a Rittal TS 8 cubicle (included in kit #68283035)
- Air baffles
- Air baffle, two R8i modules in a Rittal TS 8 cubicle (included in kit #68283035)
- Module extraction/insertion ramp
- Control electronics
- NPBU-42C branching unit
- APBU-44C branching unit
- Fuse bases
- OFASA3
- Switch fuses, charging control units
- OESL 630/32D02
- OESL 630/32D04
- OESL 630/32D06
- ASFC-21C switch fuse controller
- NCHM-11/21 charging control unit
- Diverse

ACS 800 Series
Table of contents
- Table Of Contents
- Table Of Contents
- Table Of Contents
- Table Of Contents
- Table Of Contents
- Table Of Contents
- Chapter overview
- Product and service inquiries
- How to perform the ID Run
- Control panel
- Panel operation mode keys and displays
- Drive control with the panel
- How to set speed reference
- Actual signal display mode
- How to display the full name of the actual signals
- How to display and reset an active fault
- Parameter mode
- How to adjust a source selection (pointer) parameter
- Function mode
- How to download data from the panel to a drive
- Drive selection mode
- Reading and entering packed boolean values on the display
- External control
- Block diagram: start, stop, direction source for EXT1
- Reference types and processing
- Programmable analog inputs
- Programmable analog outputs
- Programmable digital inputs
- Programmable relay outputs
- Actual signals
- Motor identification
- Automatic Start
- Flux Braking
- Flux Optimization
- Speed controller tuning
- Speed control performance figures
- Programmable protection functions
- Settings
- Ground Fault Protection
- Preprogrammed Faults
- Overfrequency
- Motor temperature measurement through the standard I/O
- Motor temperature measurement through the analog I/O extension
- Adaptive Programming using the function blocks
- General
- Checklist for a quick start-up
- Installation
- Master/Follower link specification
- Default control connections
- Tension macro
- OPEN LP TORQ
- Lead-Winder macro
- Torque Follower macro
- User macros
- REFERENCE SELECT
- CONSTANT SPEEDS
- ANALOG INPUTS
- RELAY OUTPUTS
- ANALOG OUTPUTS
- SYS CTRL INPUTS
- LIMITS
- START/STOP
- ACCEL/DECEL
- SPEED CONTROL
- TORQ REF CTRL
- FLUX CONTROL
- FAULT FUNCTIONS
- SUPERVISION
- INFORMATION
- MTR TEMP MEAS
- PULSE ENCODER
- FIELDBUS DATA
- CORE SPEED MATCH
- DANCER CONTROLS
- TENSION CONTROLS
- INERTIA CONTROL
- DIA CALC CONTROL
- TORQUE MEM CTRL
- LEAD CTRL
- ADAPT PROG CTRL
- ADAPTIVE PROGRAM
- USER CONSTANTS
- DATASET INPUT SEL
- DATASET OUTPUT SEL
- OPTION MODULES
- START-UP DATA
- Redundant fieldbus control
- Setting up communication through a fieldbus adapter module
- Setting up communication through the Standard Modbus Link
- Modbus addressing
- Setting up communication through Advant controller
- Table 1 Setting up communication
- The fieldbus control interface
- The Control Word and the Status Word
- Communication profiles
- Table 4 DataSet 1 Word 3 - Fieldbus Aux Cmd Wd (Actual Signal 06.03)
- Table 5 Main Status Word (Actual Signal 02.26)
- Table 6 Auxiliary Status Word 4 (Actual Signal 02.28)
- Table 8 Pack Status Bits (Actual Signal 03.15)
- Table 9 Alarm Word 1 (Actual Signal 02.15)
- Table 11 Alarm Word 3 (Actual Signal 02.17)
- Table 13 Fault Word 2 (Actual Signal 02.19)
- Table 15 System Fault Word (Actual Signal 02.21)
- Table 16 INT Fault Info Word (Actual Signal 02.22)
- Table 17 Limit Word 1 (Actual Signal 02.23)
- Table 19 Limit Word Inv (Actual Signal 02.41)
- Warning messages generated by the drive
- Warning messages generated by the control panel
- Fault messages generated by the drive
- Parameters
- Appendix A1: Motor Rotor Inertia, US
- Appendix A2: Motor Rotor Inertia, IEC
- Figure B-1 Diameter Calculator
- Figure B-2 Dancer Control
- Figure B-3 Tension Control
- Figure B-4 Torque Control
- Figure B-5 SPD/TQ Chain 1

ACS 800 Series
Table of contents
- Contents of this chapter
- Installation and maintenance work
- Grounding
- Fibre optic cables
- Table Of Contents
- Table Of Contents
- Table Of Contents
- Table Of Contents
- Table Of Contents
- Table of contents
- Installation and commissioning flowchart
- Terms and abbreviations
- Grid-side and rotor-side converters
- Voltage and current waveforms
- Distortion
- Mechanical construction
- Single line diagram
- Cabinet layout
- Grid supply and stator connections
- Grid-side converter supply
- Functional description
- Control boards and optional modules
- RAIO-01
- Modules
- ALCL filter module
- BLCL filter module
- Heating and cooling
- Crowbar resistor
- Interboard connection diagram
- Cooling and heating logic
- Type code
- Moving the unit
- on rollers
- Before installation
- Installation procedure
- Miscellaneous
- Electric welding
- Grid connection
- DC fuses
- Restarting after an emergency stop
- Supply line cable connection for low power supply
- Cable bus system
- Rotor cable connection
- Conduit
- Relay output contacts and inductive loads
- Selecting the control cables
- Connection of a generator temperature sensor to the converter I/O
- Control cable ducts
- Checking the insulation of the assembly
- DC and AC busbars
- Grid and rotor connections
- Grid supply connection
- Connection procedure
- Control connections
- Control unit NDCU-33Cx/RDCU-12C
- Voltage and Current Measurement Unit NUIM-61C
- Checklist
- Connecting voltage to grid terminals and auxiliary circuit
- Control program set-up
- Maintenance intervals
- Rear ventilation filters
- Power connections
- Converter module fan replacement
- Frame R8i – Circuit board compartment fan
- Power cabinet cooling fan replacement
- BLCL filter fan replacement
- Heating heater replacement
- Heatsinks
- Symbols
- AC fuses
- Breaker settings
- Cable terminals
- Ambient conditions
- Compliance with the Machinery Directive
- Product and service inquiries

ACS 800 Series
Table of contents
- List of related manuals
- Table Of Contents
- Table Of Contents
- Table Of Contents
- Table Of Contents
- Introduction
- Target audience
- Contents of the manual
- Cybersecurity disclaimer
- Drive configuration
- Configuring ACS355 drives
- Starting ACS355 drives for PROFINET
- ACS355 Minimum required parameter settings for PROFINET
- ACS355 More parameters written from PLC to drive (optional)
- ACS380 Minimum required parameter settings PROFIBUS DS
- Starting ACS380 drives for PROFINET
- ACS380 More parameters read from drive to PLC (optional)
- Configuring ACS550 drives
- Starting ACS550 drives for PROFINET
- ACS550 More actual values or parameters to be read from drive to PLC (optional)
- Configuring ACS580 drives
- ACS580 Minimum required parameter settings for PROFIBUS DP
- Starting ACS580 drives for PROFINET
- ACS580 Minimum required parameter settings for PROFINET
- ACS580 More parameters read from drive to PLC (optional)
- ACS800 Minimum required parameter settings for PROFIBUS DP
- Starting ACS800 drives for PROFINET
- ACS800 Minimum required parameter settings for PROFINET
- ACS800 More parameters read from drive to PLC (optional)
- ACS850 Minimum required parameter settings for PROFIBUS DP
- ACS850 Minimum required parameter settings for PROFINET
- ACS850 More parameters read from drive to PLC
- ACS880 Minimum required parameter settings for PROFIBUS DP
- Starting ACS880 drives for PROFINET
- ACS880 Minimum required parameter settings for PROFINET
- ACS880 More parameters written from PLC to drive (optional)
- ACSM1 Minimum required parameter settings for PROFIBUS DP
- Starting ACSM1 drives for PROFINET
- ACSM1 Minimum required parameter settings for PROFINET
- ACSM1 More parameters read from drive to PLC (optional)
- SIMATIC Manager
- Setting PG/PC interface
- Hardware configuration
- Adding Rack and CPU to the hardware
- Installing GSD files for ABB drives
- Adding drives to PROFINET
- Downloading Hardware configuration
- PLC libraries for S7-300
- Symbol Editor
- FB500 ABB_DRIVE_CONTROL_FB
- Block variables and data types
- Setting the drive in standby mode
- Setting the drive in run mode
- Downloading a program and setting PLC in run mode
- VAT table
- FC501 ACS_DRIVE_PZD (optional)
- Block variable and data types for FC501
- Scalable variables and data types
- FC500 ACS_DRIVE_PARA (optional)
- TIA portal
- Configuring S7-300 PLC
- Installing GSD and GSDML file for S7-300 PLC
- Adding ABB drives to PROFINET
- Downloading configuration to PLC
- Copying ABB drive libraries to S7-300 project
- Adding PLC tags to S7-300
- Adding watch and force tables
- FC501 ACS_DRIVE_PZD
- FC500 ACS_DRIVE_PARA
- Error codes for FB500 and FC500
- Configuring S7-1200 and S7-1500 PLC
- Installing GSD file for S7-1200 PLC
- PLC libraries for S7-1200
- Downloading configuration to S7-1200 PLC
- Copying ABB drive libraries to S7-1200 project
- Adding PLC tags to S7-1200
- Block variables and data types for FB500
- FB501 ACS_DRIVE_PARA
- Block variables and data types for FB501
- FB502 ACS_DRIVE_PZD
- Block variables and data types for FB502
- Further information
- Contact us


ACS 800 Series
Table of contents
- Table Of Contents
- Table Of Contents
- Table Of Contents
- Table Of Contents
- Table Of Contents
- Table Of Contents
- Table Of Contents
- Table Of Contents
- Table Of Contents
- Table Of Contents
- Chapter overview
- Contents
- How to perform the limited start-up (covers only the basic settings)
- How to control the drive through the I/O interface
- How to perform the ID run
- Checklist for controlling the drive from the joystick
- Checklist for controlling the drive using Step reference
- Safety Control configuration
- Brake control configuration
- Shaft synchronisation configuration
- Load speed control configuration
- Panel operation mode keys and displays
- Status row – How to read the drive status at a glance
- Drive control with the panel
- How to set speed reference
- Actual signal display mode
- How to display the full name of the actual signals
- How to display and reset an active fault
- Parameter mode
- How to adjust a source selection (pointer) parameter
- Function mode
- How to download data from the panel to a drive
- How to set the contrast of the display
- Drive selection mode
- Reading and entering packed boolean values on the display
- Local control
- External control
- Settings
- Block diagram: reference source for EXT1
- Zero position of the joystick
- Reference types and processing
- Programmable analogue inputs
- Programmable analogue outputs
- Programmable digital inputs
- Additional information for Digital Inputs and Pointers PTR
- Programmable relay outputs
- Actual signals
- Motor identification
- Flux braking
- Flux optimisation
- Acceleration and deceleration ramps
- Step referencing
- Speed controller tuning
- Speed control performance figures
- Scalar control
- Hexagonal motor flux
- Motor thermal protection
- Stall protection
- Earth fault protection
- Preprogrammed faults
- Drive temperature
- Input phase loss
- Parameter lock
- Motor temperature measurement through an analogue I/O extension
- External speed limitation
- Speed monitor (internal overspeed protection)
- Speed matching (internal overload protection)
- Power ON acknowledge and internal fault reset
- Actual position configuration based on a motor encoder signal
- Master/Follower use of several drives (Only in EXT2 Control)
- Master/Follower interlock words
- Speed reference scaling between the Master and the Follower
- Settings and Diagnostics
- Shaft synchro (Only in EXT2 Control)
- Defining the basic data for speed correction
- External speed correction
- Synchro error blocking
- Service counter
- Examples of crane functionalities created with DriveAP
- Control of a mechanical brake
- Operation time scheme
- State shifts
- High-end and Low-end limits
- Start high logic
- Inverter limit
- Load speed control
- Control locations and control modes
- Default control connections
- User macros
- Control schemes
- RDIO-01 digital I/O extension
- Control using motorized potentiometer
- RDIO-01 digital I/O extension module -1
- Control using fieldbus
- Parameters
- REFERENCE SELECT
- ANALOGUE INPUTS
- RELAY OUTPUTS
- ANALOGUE OUTPUTS
- SYST CTRL INPUTS
- LIMITS
- START/STOP
- ACCEL/DECEL
- SPEED CTRL
- TORQUE CTRL
- MOTOR CONTROL
- BRAKE CHOPPER
- INFORMATION
- MOT TEMP MEAS
- BRAKE CONTROL
- ENCODER MODULE
- COMM MODULE DATA
- DDCS CONTROL
- SPEED MATCHING
- LOAD SPEED CTRL
- SHAFT SYNCRO
- ADAPTIVE PROGRAM
- USER CONSTANTS
- HARDWARE SPECIF
- EXTERNAL AO
- MOTOR MODEL
- OPTION MODULES
- START-UP DATA
- Redundant fieldbus control
- Setting up communication through a fieldbus adapter module
- Setting up communication through the Standard Modbus Link
- Modbus addressing
- Setting up communication through Advant controller
- Drive control parameters
- The fieldbus control interface
- The Control Word and the Status Word
- Actual Values
- Communication profiles
- MAIN CONTROL WORD
- MAIN STATUS WORD
- State Machine for the ABB Drives communication profile
- Fieldbus reference scaling
- Start/Stop sequence using communication bits
- Flow chart for Main Control Command Bit sequence
- Fieldbus references in a Master/Follower configuration
- Generic Drive communication profile
- Drive commands supported by the Generic Drive communication profile
- CSA 2.8/3.0 communication profile
- Diverse control, status, fault, alarm and limit words
- LIMIT WORD 1
- FAULT WORD 2
- SYSTEM FAULT WORD
- ALARM WORD 2
- AUXILIARY STATUS WORD 3
- ALARM WORD 4
- ALARM WORD 5
- Warning codes
- LIMIT WORD INV
- ALARM WORD 6
- CRANE FAULT WORD
- FCW WITH POS
- INT SC INFO
- Warning messages generated by the drive
- Warning messages generated by the control panel
- Fault messages generated by the drive
- Brake match
- Redundancy in Master/Follower crane control
- Scaling actual encoder position signal (mm) to analogue output as mA
- Slack rope torque detection
- Conical rotor motors
- Parameter settings: bipolar input in basic speed control
- Parameter settings: bipolar input in joystick mode
- DriveWindow
- Control block diagrams
- Product and service inquiries

ACS 800 Series
Table of contents
- Table Of Contents
- Table Of Contents
- Introduction
- Fieldbus grounding
- Drives with embedded fieldbus
- Fieldbus modules for ABB drives
- ABB cable TK505
- AC500 COM1 – Master at the bus line end
- AC500‐eCo COM2 – Master at the bus line end
- Drive configuration
- Starting up ACS310 drives with embedded Modbus RTU
- Starting up ACS355 drives with FMBA‐01 Modbus RTU adapter
- Starting up ACS800 drives with RMBA‐01 Modbus RTU adapter
- Starting up ACS850, ACQ810 drives with embedded Modbus RTU
- Starting up ACS880 drives with FSCA‐01 Modbus RTU adapter
- Starting up ACSM1 drives with FSCA‐01 Modbus RTU adapter
- Install drives library
- Control Builder Plus for PLC and Drives
- IP configuration of CPU (for Ethernet connection between PC and PLC)
- CODESYS
- Library Manager
- PLC logic
- Download program to PLC
- Create boot project
- Test the program
- Read and write more data between PLC and drive (optional)
- Visualizations
- Add more drives (optional)
- Actualization rate
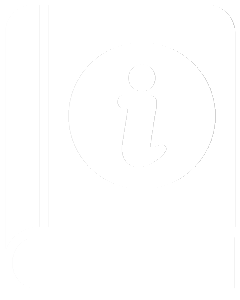
manualsdatabase
Your AI-powered manual search engine