YASKAWA Motoman DX200 manuals

Motoman DX200
Table of contents
- instruction manual
- Table Of Contents
- Table Of Contents
- Table Of Contents
- General
- Safety
- Handling ESD sensitive devices
- Terms
- Installation
- NX100 Installation
- Software configuration
- Manual I/O allocation (FD 134)
- Fieldbus input data map
- Fieldbus status byte
- General installation in IP-based networks
- Anybus IPconfig
- The module is not shown
- Reg.No. ME00107EN-02 Page
- Profibus DPV1 Slave AB3601
- Connectors 9-pin D-sub
- PROFIBUS network setup
- Profibus DPV1 Master AB3602
- Configuration online
- DeviceNet Adapter Slave AB3603
- Connectors
- DeviceNet Scanner Master AB3604
- AnyBus NetTool for DeviceNet
- AS-Interface Master AB3605
- Principle of Input/Outputs in ASI
- Menu Tree Overwiev
- Change settings
- EtherNet/IP Adapter/Modbus TCP Slave AB3606
- Status LEDs
- Network setup
- EtherNet/IP Scanner Master AB3607
- PROFINET-IO Slave AB3609
- FL-Net AB3610
- FIPIO Slave AB3611
- Interbus-S Slave AB3615
- Setup
- CanOpen Slave AB3616
- EtherCAT slave AB3617
- revision history

Motoman DX200
Table of contents
- Table Of Contents
- Table Of Contents
- Table Of Contents
- Table Of Contents
- Introduction
- Seam Finding
- Macro Jobs
- Features
- System Requirements
- Setup and Operation
- Setting the Q1 Focal Length:
- AccuFast II
- Using the Zero Shift Function (If Temperature Variance is a Concern)
- Job Setup
- AutoTeach
- TCH Macro, One Touch (1TCH) Routine
- Limitations
- AutoTeach Mode
- Macro Job Setup
- Interface
- Programming Instructions
- TCH Macro, Two Touch (2TCH) Routine
- EDGE: Edge Finding Routine
- Programming
- AutoTeach 1 (Robot Position 2)
- AutoTeach 2 (Robot Position 3)
- R1 CIRCLE: Circle Touch Routine
- Setup Macro Instruction and Detect Robot Position 1
- Detect Robot Position 2
- Cylinder to Plate
- Programming Suggestions
- AccuFast II Orientation
- Perpendicular Search Paths
- Pattern Type and AutoTeach Descriptions
- AutoTeach 0
- AutoTeach 2
- Pattern Type 2
- Pattern Type 4
- AutoTeach 2, Step Offset 0
- Target for TCP Update for AccuFast or AccuFast II
- Breakdown of Procedure
- Detailed Usage
- Adjust Settings of ACCUFAST - TCP - UPDATER robot job
- Set and Program the AccuFast - TCP - UPDATER Robot Job
- Run the Robot Job in Train Mode
- Appendix B
- Run the Robot Job in Calc Mode
- TCP Detection Mode (Optional)
- Appendix A
- B.1 Value B Variables
- Appendix C
- Appendix D

Motoman DX200
Table of contents
- Table Of Contents
- Overview of DX200 Setup Procedure
- Programming Pendant Setup
- Preparing the CF/USB for Upgrading
- Setting Up the Programming Pendant
- Initialization of System Configuration in Maintenance Mode
- Troubleshooting
- Possible Failure at Setup of the Programming Pendant
- Programming Pendant Flash Rom Format Procedure
- Redisplaying the Touch Calibration Display
- When the Message 'Cannot find YPP (or one of its components).' is Displayed
- Possible Failures at YCP21 Setup
- HW1481993


Motoman DX200
Table of contents
- Table Of Contents
- Table Of Contents
- Table Of Contents
- Overview of the Function
- Configuration of Setting Files
- System Configuration
- Functional Safety I/O Logic Board
- Functional Safety Terminal Block Board
- Wiring Procedure of the Terminal Block
- Functional Safety Universal Input Signal 1-8
- Functional Safety Universal Output Signal 1-8
- Functional Safety Universal Output Feedback Signal 1-8
- Board Arrangement
- System Configuration for Dual-Arm Manipulator
- Common Operation
- Read-Back Operation
- External Memory Device (Saving/Loading)
- Details of Functional Safety Function
- Axis Range Limit Function Window
- AXIS RANGE LIMIT Condition File Setting
- Confirming Method of Each Axis Operating Angle
- Confirmation of Safety Range
- Start AXIS RANGE LIMIT Operation
- AXIS SPEED MONITOR Function
- Axis Speed Monitor Function Window
- AXIS SPEED MONITOR Condition File Setting
- Start AXIS SPEED MONITOR Operation
- Robot Range Limit Function
- Robot Range Limit Function Window
- Robot Range Limit Function Condition File Setting Window
- Confirmation of the Safety Range
- Starting the ROBOT RANGE LIMIT
- Switch the Monitoring Area
- Safety Range and Manipulator Position
- Proximity Warning Buzzer Setting
- Combining Function of Multiple Monitoring Areas
- Speed Limit Function
- Speed Limit Function Window
- Speed Limit Function Condition File Setting Window
- Starting the SPEED LIMIT
- SPEED LIMIT in Teach Mode
- TOOL ANGLE MONITOR Function
- Tool Angle Monitor Function Window
- TOOL ANGLE MONITOR Condition File Setting
- Confirmation of TOOL ANGLE LIMIT MONITOR
- Tool Change Monitor Function
- Tool Change Monitor Function Window
- TOOL CHANGE MONITOR Condition File Setting
- Confirmation of Tool Change Monitor
- When Using the Tool Change Monitor Function
- Common Setting Item for the Condition File
- Safety Signal
- Safety Fieldbus Signal Allocation
- Safety Function Condition File Setting
- File Switching to Valid/Invalid by the Safety Signal
- Safety Signal Output Value
- Common Settings
- Specific Output Signal
- Restrictions while Function Disable Mode Function is Valid
- Security Level Setting for Function Disable Mode
- External Axis Coasting Value Setting
- Tool File Setting
- Tool Interference File Setting
- Security Level Setting for Tool File and Tool Interference Files
- Data Protection
- FLASH Data Reset
- LED Indication
- LED Indication during Start-up Process
- Functional Safety Board Replacing Procedure
- Restriction
- Functions Conditionally Used Concurrently with Functional Safety Function
- Restriction of Operation
- Tool Calibration

Motoman DX200
Table of contents
- Table Of Contents
- Table Of Contents
- Functional Overview
- Setup
- Setting and Confirmation of Hardware Configuration
- Connection of Welding Power Source and DX200
- System Configuration
- Setting of Optional Function "Network Function"
- Setting of Optional Function "WELDCOM Function"
- Detailed Setting of Welding Power Source
- I/O Module Setting Check after Adding Virtual EW Module
- Loading of MotoPlus Application (When Welder is FroniusTPSi)
- Setting of Parameter (When Welder is FroniusTPSi)
- Optional Parameters for FroniusTPS
- Optional Parameter for FroniusTPSi
- Operation of Welding Condition File Edit Window
- MOTOWELD Type: Operation of Top Window
- MOTOWELD Type: Operation of Weld type Window
- MOTOWELD Type: Operation of Customize Window
- MOTOWELD Type: Operation of Maintenance Window
- MOTOWELD Type: Operation of Welder Parameter Window
- FroniusTPS Type: Operation of Top Window
- FroniusTPS Type: Operation of Program No. setting Window
- FroniusTPS Type: Operation of Param. setting Window
- FroniusTPSi Type: Operation of Top Window
- FroniusTPSi Type: Operation of Select Synergic Window
- FroniusTPSi Type: Operation of Weld Parameter Setting Window
- Job Preparation for Welding
- Alarm and Error
- Error

Motoman DX200
Table of contents
- Table Of Contents
- Table Of Contents
- Table Of Contents
- General
- Target group
- Improper use
- About this manual
- Safety
- For your security
- YASKAWA manual list
- Safety during installation and wiring
- Manufacturer
- Supply
- Position type plate
- Transportation
- Using a forklift
- Assembly and installation
- Ambient conditions and installation location
- Installation example
- Wiring
- Notes on cable junctions
- Installing residual current circuit breakers (optional)
- Installation of primary power supply breaker
- Cable connections
- Connection of the robot controller
- Technical data
- Programming pendant specifications
- Maintenance and inspection
- Cooling fan inspections
- Inspection of the enabling switch
- Check battery unit
- Open Phase Check
- Description of Units and Circuit Boards
- Power ON unit
- Axes control circuit board
- External axes control circuit board
- CPU unit configuration
- Unit and circuit board in the CPU unit
- Machine safety I/O logic circuit board
- Connection for tool shock sensor (SHOCK)
- Machine safety terminal block circuit board (JANCD-YFC22-E)
- External emergency stop signal
- Installation of safety plug
- External enable switch
- Full speed test
- Slow speed mode
- External SERVO-ON
- SYSRUN Signal Output
- External axes overrun
- SERVO-ON enable input
- Emergency stop button output
- Universal safety input
- Universal safety output
- Direct-in (SERVO) 1 to 6
- Universal input (SERVO)
- Universal I/O circuit board (JANCD-YIO22-E)
- Brake control circuit board (JANCD-YBK21-3E)
- Converter (SRDA-COA30A21B-E)
- Capacitor module (SRDA-CUA AA)
- Amplifier module (SDRA-SDA A01A-E)
- Assignment of general I/O signal
- ARC welding
- Handling
- Spot welding
- JANCD-YEW01-E circuit board (Standard)
- The list of the Equipment configuration by model
- Robot controller specification
- Specification list
- Function list
- Programming Pendant
- Device configuration
- Recommended spare parts list

Motoman DX200
Table of contents
- 165303-1CD
- Table Of Contents
- Outline
- Ethernet Cable Connections
- Ethernet Function Settings
- Ethernet Communication Settings
- Description of setting items (Network function setting window)
- IP ADDRESS SETTING
- DNS SETTING
- SERVER (HOST PC)
- Settings confirmation
- Specifications
- Cable Specifications
- Restrictions
- Troubleshooting
- Connection Check with Lower Protocol
- Connection Check with MOTOCOM
- HW1481821

Motoman DX200
Table of contents
- Table Of Contents
- Table Of Contents
- Introductions
- Message Communication
- Board Specifications
- How to Connect Communication Cable
- Operating the Front Door of the DX200 (Controller)
- Mounting the EtherNet/IP (CPU board) to DX200
- Closing the Front Door of the DX200
- EtherNet/IP Function Setting
- Window Composition
- Setup Procedure
- Setting the Device Information List
- General Setup for the EtherNet/IP (CPU board)
- Adaptor Setting
- Scanner Setting
- IO Module Re-configuration
- External I/O Setup
- Reset Safety Circuit Board FLASH Data
- IO Assignment Example
- Communication Data
- DX200 IO Data Allocation (For the Handling Purpose)
- DX200 IO Data Allocation (For other than Handling Purpose)
- Communication Status
- Managing Setting Data
- How to Load Data
- Creating an EDS File
- Details on Commands for Message Communication Using CIP
- Related Parameters

Motoman DX200
Table of contents
- Table Of Contents
- Table Of Contents
- Outline
- Hardware Specifications
- Board Specifications
- Attaching of the Board
- Operating the Front Door of DX200 (Controller)
- Attaching the CP1616 to the DX200
- Closing the Front Door of the DX200
- Setting of the Board
- IO Controller Settings
- IO Device Settings
- CP1616 (IO Device) Settings with IO Controller
- Coupling Settings
- Calling Up the CP1616 Setting Window
- IO Module Settings
- External IO Settings
- GSD File Creation
- Allocating I/O Signals
- I/O Allocation Examples for DX200 (Except for Handling)
- Board Status
- Management of Setting Data
- Procedures for Loading
- Additional Functions for IO Controller
- Message Communication Function
- Supplementary Note
- Alarm History Displaying Function
- Error Indication
- Trouble Shooting

Motoman DX200
Table of contents
- Table Of Contents
- Table Of Contents
- Introduction
- System Outline
- System Configuration
- Transmission Procedure
- Socket Connection
- Response to Command
- Command Details
- Read/Data Access System Command
- System Control Function
- Start-Up System Command
- Editing System Commands
- Job Selection System Command
- I/O Read/Write Function
- Write-in of I/O Signal Status
- Transmission Examples
- Write-In of I/O Signals for the DX200
- Continuous Execution of Multiple Commands
- Function Checkout Procedure
- Connection Check with Lower Protocol
- Connection Check with telnet
- Restrictions
- Restrictions on the Number of Sockets
- HW1481823

Motoman DX200
Table of contents
- Table Of Contents
- Table Of Contents
- Sensor Function
- Search Function
- Wiring
- Direct-in Signal Connection
- Real-time Path Correction Function
- Correction Amount
- Correction Direction
- Forward Direction
- Monitoring of Sensor Input Voltage
- Display of Sensor Monitor Condition File
- Instructions for the Real-time Path Correction Function
- Registration of the ACORON Instruction
- ACOROF and SACOROF Instructions
- ACORCH and SACORCH Instructions
- Registration of the ACORCH Instruction
- Real-time Speed Correction Function
- Override Ratio
- Instructions for the Real-time Speed Correction Function
- Registration of the AOVRON Instruction
- AOVROF Instruction
- Shift Amount Creation Function
- GETSFT Instruction
- Registration of the GETSFT Instruction
- Detection Results
- ASRCH Instruction
- Registration of the ASRCH Instruction
- Calibration
- Registration of the SCALIB Instruction
- Entering an Offset Value
- Alarm List

Motoman DX200
Table of contents
- Table Of Contents
- Table Of Contents
- Outline
- XFB01B Board in Master Mode
- Hardware Specifications
- Communication Specifications
- Setting Functions
- Setting Switches
- Function Setting Terminals
- Setting Terminals
- Mounting XFB01B Board
- Opening Front Door of the DX200
- Connecting Each Cable
- Closing the Front Door of the DX200
- Allocating I/O Signals
- Transmission Data
- DX200 I/O Allocation example (For Handling)
- DX200 I/O Allocation example (For Except Handling)
- DeviceNet Slave Allocation (Only in Master Mode)
- Management of DeviceNet Slave Allocation (Only in Master Mode)
- Loading from External Memory
- Network Specifications
- Precautions for Wiring DeviceNet Cables
- Connections for DeviceNet Communications
- Location of Power Supply
- How to Decide the Location of the Power Supply
- Grounding
- Error Indication
- NS Lamp
- HW1481973

Motoman DX200
Table of contents
- Table Of Contents
- Table Of Contents
- Overview
- Specification
- Setting and Operation for Data Measurement
- Main Screen Configuration
- Main Screen (In-measurement Mode)
- Setting Measurement Conditions
- CH Display Setting Panel
- TimeScale Setting Panel
- Trigger Setting Panel
- Starting and Ending Measurement
- Trigger Mode
- Termination and Minimization of Pendant Oscilloscope Function
- Saving and Loading the Measurement Data
- CSV File
- Load Panel
- Other Functions
- During Execution of Zoom Function
- Cursor Measurement Function
- Cursor Measurement Parameters
- Job Step No. Saving Function
- Channel Setting
- Operation Function by Dedicated Input
- Dedicated Output Signal
- Supplementary Explanation
- Reference Unit
- Error Messages

Motoman DX200
Table of contents
- Table Of Contents
- Table Of Contents
- Table Of Contents
- Product Confirmation
- Order Number Confirmation
- Transport
- Using a Crane
- Shipping Bolts and Brackets
- Installation
- Safeguarding Installation
- Mounting Example
- Location
- Wiring
- Cable Connection
- Basic Specifications
- Part Names and Working Axes
- Dimensions and T-Point Maximum Envelope
- Stopping Angles and Times for S-, L-, and U-Axes
- Position 66%
- Position 33%
- Stop Category 1: Stopping Angles and Times
- Alterable Operating Range
- Components for Altering Operating Range
- Notes on the Mechanical Stopper Installation
- Adjustment of the Soft Limit of the S-Axis Pulse
- Allowable Load for Wrist Axis and Wrist Flange
- Wrist Flange
- System Application
- Internal User I/O Wiring Harness and Air Line
- Electrical Equipment Specification
- Setting of Operation Range
- Internal Connections
- Maintenance and Inspection
- Notes on Maintenance Procedures
- Grease Replenishment/Exchange
- Grease Replenishment/Exchange for S-Axis Speed Reducer and Gear
- Grease Exchange
- Grease Replenishment/Exchange for L-Axis Speed Reducer
- Grease Replenishment/Exchange for U-Axis Speed Reducer
- Grease Replenishment/Exchange for U-Arm
- Grease Replenishment for R-, B-, T-Axes Gears in the Casing
- Grease Replenishment for R-Axis Speed Reducer
- Grease Replenishment for B-Axis Speed Reducer
- Grease Replenishment for T-Axis Speed Reducer
- Grease Exchange for R-, B-, T-Axes Gears in the Casing
- Grease Exchange for R-Axis Speed Reducer
- Grease Exchange for B-Axis Speed Reducer
- Grease Exchange for T-Axis Speed Reducer
- Grease Replenishment for Balancer Connection Part
- Notes for Maintenance
- Recommended Spare Parts
- parts list
- L-Axis Unit
- U-, R-, B-, T-Axes Unit
- U-Arm Unit
- Wrist Unit
- Balancer Unit

Motoman DX200
Table of contents
- Table Of Contents
- Table Of Contents
- Table Of Contents
- Conveyor Synchronized Function with Shift Functions
- Start Shift Function
- WORK ID Shift Function
- WORK IN/NOT Shift Function
- Precautions on Using Conveyor Synchronized Function with Shift Functions
- Conveyor Condition File
- Editing Conveyor Condition File
- Setting Conveyor Resolution
- Detection Function for BROKEN LINE DETECT Status (Conveyor Pulse)
- Conveyor Supplemental Condition File
- Start Shift Condition File
- Editing the Start Shift Condition File
- WORK ID SHIFT Condition File
- Editing the WORK ID SHIFT Condition File
- WORK IN/NOT SHIFT Condition File
- Editing the WORK IN/NOT SHIFT Condition File
- Teaching
- Instruction List
- SYEND Instruction
- CVQUE Instruction
- Interpolation Mode for Conveyor Synchronized Motion
- Manipulator Motion Speed
- Teaching After Interruption of Synchronized Motion in Playback Operation
- Notes on Operation
- Job Examples
- Job Example when Using the Start Shift Function
- Manual Setting Function for Conveyor Position
- Manual Setting Procedure for the Conveyor Position
- Test Run without Moving the Conveyor
- Manual Setting Function for Pseudo ON of the Conveyor Home-position Limit Switch
- Playback
- Accuracy
- Restarting Synchronization After Manipulator Stops
- Detection of the Position beyond the Specified Maximum-workpiece-position
- Conveyor Monitoring Displays for the Shift Functions
- CV (SYNCHRONIZATION) MONITOR Display
- Switching the Reference Workpiece for Synchronization
- Deleting a Data of Conveyor Synchronized Section
- CV START SHIFT STATUS Display
- Deleting a Conveyor Start Shift Data
- CV WORK ID SHIFT STATUS Display
- Deleting a Conveyor WORK ID Shift Data
- CV WORK IN/NOT SHIFT STATUS Display
- Deleting a Conveyor WORK IN/NOT Shift Data
- CV SHIFT MONITOR display
- Deleting a Data of Conveyor Shift Section
- Alarm List
- Specific I/O Signals
- Conveyor Parameters
- Sensor Parameters (SxE)

Motoman DX200
Table of contents
- Table Of Contents
- Table Of Contents
- Table Of Contents
- Table Of Contents
- Conveyor Synchronized Function
- Conveyor Synchronized Operation
- Conveyor Home-position Limit Switch
- Conveyor
- Definition of Conveyor Moving Direction
- Hardware Specifications
- Connecting Conveyor Home-Position Signals to DX200
- Applicable Encoder and Connection Specification
- Connection Example of One Conveyor
- Connector Connection
- Sensor Cable Connection
- Closing the Front Door
- Settings for Conveyor Condition File
- Editing Conveyor Condition File
- Editing "CORRECTION"
- Editing "VIRTUAL ENCODER INPUT"
- Setting Conveyor Positional Resolution
- Verifying and Adjusting Conveyor Positional Resolution
- Teaching
- Instruction List
- SYEND Instruction
- SYMOV¨ Instruction
- Interpolation Mode for Conveyor Synchronized Operation
- Motion Speed
- Wrist Posture in Synchronization
- Circular Interpolation Steps
- Teaching After Interruption of Playback in Synchronized Operation
- When Performing Another Teaching (for Other Workpiece)
- Notes on Operation
- Job Example
- Playback
- Accuracy
- Restarting Synchronization After Manipulator Stops
- Conveyor Monitoring Windows
- Conveyor Position Window
- Conveyor Speed Window
- Conveyor Tracking Status Window
- Virtual Encoder Mode
- Turntable Synchronized Function
- Calibration between Manipulator and Turntable
- Operating Calibration
- Modifying Instructions
- Manual Conveyor Function
- Settings for Manual Conveyor Function
- Manual Setting Function for Conveyor Home-Position Limit Switch
- Alarm List
- Specific I/O Signals
- Conveyor Parameters
- Sensor Parameters (SxE)


Motoman DX200
Table of contents
- Table Of Contents
- What is the Interrupt Job Function?
- Setting of the Interrupt Job Function
- Setting of Interruption Table
- Setting of Job Names
- Setting of Interruption Levels
- Registration of Instructions
- DI (Disable Interruption) Instruction
- Execution of an Interrupt Job
- Output Signal of "Interrupt Job in Execution"
- Application Examples
- Interruption During Move Instruction with NWAIT
- Interruption During Circular Interpolation Move Instruction (MOVC)
- System with Independent Control
- Instruction List
- HW1481811

Motoman DX200
Table of contents
- Table Of Contents
- About I/O Output Timing Control Function
- Setup of I/O Output Timing Control Function
- Configuration of +DOUT Instruction
- Registration of +DOUT Instruction
- Configuration of +PULSE Instruction
- Registration of +PULSE Instruction
- Device Response Delay Time Compensate Parameter
- The Examples of the I/O Output Timing Specifying Function
- HW1481819

Motoman DX200
Table of contents
- Table Of Contents
- Features of System with the XFB03 Board
- Board External View
- Communication Specifications
- Connector
- Function Setting Switches
- Switch Setting Method
- Opening Front Door of the DX200
- Connecting Each Cable
- Closing the Front Door of the DX200
- I/O Module Setting
- Transmitting Data
- DX200 I/O Allocation Example (For Except Handling)
- LED Indicators
- Corrective Actions
- HW1486969

Motoman DX200
Table of contents
- Table Of Contents
- Form Cutting Motion
- Patterns for Cutting
- Teaching
- Tool Position and Cutting Pattern
- Cutting Width Correction Function
- Example of Form Cutting Function
- Example of a Motion Path
- Motion Example 1
- Motion Example 2
- Form Cutting Start Motion Instruction
- Registering Instructions
- Registering in Variables
- Form Cutting Instruction
- Form Cut Setting File
- Settings
- Details of File Settings
- Specifying the ROTATION DIRECTION
- Examples of File Setting for Each Pattern
- Rectangle Including Squares
- Ellipse
- Pentagon
- Hexagon
- Displaying and Editing File
- Alarm Message List
- HW1481987

Motoman DX200
Table of contents

Motoman DX200
Table of contents
- Table Of Contents
- Table Of Contents
- Introduction
- Hand Guiding Function
- System Configuration of Hand Guiding Function
- System Configuration for Using Hand Guiding Device of Handle Type
- System Configuration for Using Hand Guiding Device of Grip Type
- Connection for Hand Guiding Device
- Connection for Presence Detection Sensor
- Speed Limiting Function
- Setup of Hand Guiding Function
- Filter Setting
- Setting of Speed Coefficient
- Setting of Operation Angle Limit
- Setting of Area Limit
- Tool Setting
- Tool Coordinate System and Sensor Coordinate System
- Calculating Setting Value of Sensor Mounting Angle
- Setting Example of Sensor Mounting Angle
- Setting Confirmation of Sensor Mounting Angle
- Hand Guiding Function Execution Procedures
- Job Creation for Hand Guiding Function Execution
- Mode
- Inching Mode
- Translation/Rotation
- Force Sensor/ I/O Input
- Calibration of Force Sensor
- Register Output Function
- Risk Assessment
- Risk Reduction Measures
- User Variables and General I/O Signals to be Used with Hand Guiding Function
- General I/O Signal List
- Ladder Program
- Troubleshooting
- Enabling Force Sensor
- Robot Operating Method When Hand Guiding Device Disconnected
- Alarm List

Motoman DX200
Table of contents
- Table Of Contents
- Table Of Contents
- Outline of Function
- Automatic Adjustment Function of Force Control Parameter
- Adjustment Method
- MotoFit Teach Guidance Function
- Function for Calculation of Force Detection Threshold
- Interface Panel
- Operation Procedure
- Setting the IP address
- Operation for Creating Fitting JOB
- Detailed Operation Step
- Setting Force Condition File
- Automatic Adjustment of Force Control Parameter
- TOUCH Command Teach
- FIT Command Teach
- INSERT Command Teach
- Creating MotoFit JOB
- Chage of Unit Scale (only for the FS100)
- Teach of Force Sense Basic Command
- Threshold Setting by Data Logging
- Operation Check
- Monitor Information
- Operation Condition Data
- Adjustment Condition Data
- MotoFit Command Argument Data
- Backup of Teach Data
- Data for Setting Detection Threshold
- Error of Automatic Adjustment Function of Force Control Parameter
- Alarm List of FSE-Tools
- How to Check the Version
- Precautions

Motoman DX200
Table of contents
- Table Of Contents
- Table Of Contents
- Table Of Contents
- Table Of Contents
- Features
- Hardware Lock Key
- Basic Concept and Operation Flow
- Basic Windows
- Selecting a Job
- Opening Multiple Jobs at One Time
- Filtering by Job Folder
- Creating a Job
- Selecting Options when Creating a Job
- Copying a Job
- Deleting a Job
- When No Job is Provided
- Closing a File
- Saving a File
- Printing
- Exit
- Change into Standard Mode
- Adding an Instruction
- Deleting an Instruction
- Selecting Multiple Lines
- Copying an Instruction
- Pasting an Instruction
- Reverse
- Modifying an Instruction
- Changing Numeral Values (2)
- Changing Characters
- Changing the Motion Type
- Using an Alias
- Editing in the Detail Edit Window
- Adding an Item
- Deleting an Item
- Searching
- Changing the Speed
- Edit Lock
- Clear the Edit Lock Status
- Comment
- Clear the Comment Status
- Clear the All Comment Status
- Adding Comments
- Edit the Job Folder Name
- of Local Variables Used
- Displaying Step Nos., I/O Names or Variable Names
- Opening a Call Job
- Editing an Expression
- Using a Macro Command
- Change into Text Mode
- Showing the header part
- Hiding the header part
- Checking the job
- Saving the Job File
- Checking Alias
- Defining Control Groups
- Changing a Combination
- Deleting a Combination
- Defining Position Variables
- Increasing the Instruction Types to be Used
- Changing a Condition File
- Changing a Variable Name File (VARNAME.DAT)
- Changing the Font
- Changing the Color
- Changing the Background Color
- Changing the Comment Color
- Changing the Color of Each Instruction or Tab
- Adding Private Setting
- Changing Private Settings
- Deleting Private Settings
- Changing Color Definition
- Adding Color Definition
- Deleting Color Definition
- Changing the Language
- Batch-Change the Job Folder Name
- Changing the Default Mode
- Frequently-asked questions

Motoman DX200
Table of contents
- Table Of Contents
- Outline
- Hardware Specification
- Board Specification
- Settings and Installation of the Board
- Mounting the Board
- Mounting the AB3607 Board to the DX200
- Closing the DX200 Front Door
- Allocating I/O Signals
- When Setting with Only the Maintenance Mode
- Device Information List Setting
- AB3607 Setting
- Ethernet Setting
- Scanner Setting
- Terminal Output Function
- Terminal Output Setting
- When Setting with the PC Tool and the Maintenance Mode
- Communication Setting of the AB3607
- Transmitting Data
- Communication Status
- I/O Allocation
- I/O Allocation Examples of the AB3607 for DX200 (Except for Handling)
- Convenient Function
- Error Indication
- HW1486011

Motoman DX200
Table of contents
- Table Of Contents
- Table Of Contents
- Outline of Function
- Automatic Adjustment Function of Force Control Parameter
- Adjustment Method
- MotoFit Teach Guidance Function
- Force Sense Basic Command
- System Configuration
- Version
- Operation Procedure
- MotoFit Teach Operation
- Detailed Operation Step
- Setting Force Condition File
- Automatic Adjustment of Force Control Parameter
- TOUCH Command Teach
- FIT Command Teach
- INSERT Command Teach
- Creating MotoFit JOB
- Teach of Force Sense Basic Command
- Threshold Setting by Data Logging
- Operation Check
- Monitor Information
- Operation Condition Data
- Adjustment Condition Data
- MotoFit Command Argument Data
- Backup of Teach Data
- Data for Setting Detection Threshold
- General Output and Variables
- Error of Automatic Adjustment Function of Force Control Parameter
- Alarm List of FSE-Tools
- Precautions
Related products
MOTOMAN DX100Motoman MLX200MOTOMAN-NX100motoman NX100MOTOMAN FS100Motoman NXC100MOTOMAN SeriesMP2200MP3200MP2000 SeriesYASKAWA categories
Controller
DC Drives
Servo Drives
Inverter
Touch Panel
Robotics
Control Unit
Industrial Equipment
Media Converter
Industrial Electrical
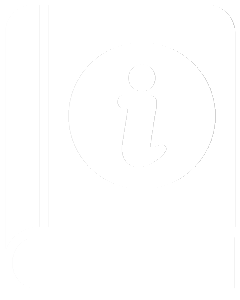
manualsdatabase
Your AI-powered manual search engine