KEB COMBIVERT F5 manuals

COMBIVERT F5
Table of contents
- Table Of Contents
- Safety and Operating Instructions
- Product description
- Technical data
- Dimensions and Terminals
- Installation and Connection
- Connection of Power Circuit
- Mains connection
- Connection of the temperature monitoring
- Connection of a braking resistor with temperature monitoring in accordance with UL
- Incremental encoder input / -emulation X3B
- Control board Servo
- Connection of the control terminal strip
- Operation of the Unit
- Remote control
- Resetting error messages
- Parameter description for F5 servo
- A.1 Overload characteristic
- A.4 Storage
- A.5 Changing the response threshold of the braking transistor
- B.1 CE-Marking
- B.3 Additional Manuals

COMBIVERT F5
Table of contents
- Table Of Contents
- Product Description
- Installation instructions
- Requirements on the coolant
- Operating conditions
- Technical Data of the 400 V Class
- Dimensions and weights
- Heat sink with cooling fan (through-mount version)
- Water-cooled inverter - wall mounted version
- Water-cooled inverter - through-mount version
- Terminal strips of the power circuit
- Motor output
- Other terminals
- Connection accessories
- Technical data filter
- Technical data mains choke
- Technical data motor choke (Uk
- Mains and motor connection
- Selection of the motor cable
- Temperature detection T1, T2
- Use of the temperature input in KTY mode
- Connection of a braking resistor
- protection without GTR7 monitoring (air-cooled inverter)
- Overload Characteristic
- Protection with MCCB in accordance with UL 489 (UL: DIVQ)
- Cooling circuit


COMBIVERT F5
Table of contents
- Table Of Contents
- Preface
- Copyright
- Control
- LED1
- Connection of the control
- Assignment of the terminal strip X2A
- Connection of the digital inputs
- Connection of the analog inputs
- Connection of the analog outputs
- Assignment of the terminal block X2B
- Safety Function STO
- Emergency stop according EN 60204
- Classification of STO according IEC 61508
- Functional Description
- Wiring Examples
- Direct switching off with emergency stop switch and monitoring of the wiring
- Direct switching off by safety module with test pulses
- Wiring SS1
- Certification
- Revision history

COMBIVERT F5
Table of contents
- Table Of Contents
- Safety and Operating Instructions
- Product description
- Technical data
- V class
- Dimensions and Terminals
- Installation and Connection
- Connection of Power Circuit
- Mains connection
- Motor connection
- Connection of a braking resistor with fire prevention
- Control Board Basic
- 3.4.2 Connection of the control terminal strip
- Control board Compact/General/Appli cation without encoder interface
- Connection of the control terminal strip
- Control board Multi/Servo/Application with encoder interface
- Operation of the Unit
- Remote control
- Resetting error messages
- Parameter Descriptions
- Parameter description for Multi and Application with encoder interface
- Parameter description for F5 servo
- A.1 Overload characteristic
- A.4 Storage
- the braking transistor
- B.1 CE-Marking
- B.3 Additional Manuals

COMBIVERT F5
Table of contents
- Table Of Contents
- Preface
- Copyright
- Product Description
- Description of the Hardware
- Software
- Set-addressing with subindex
- Synchron-Modus
- Fieldbus watchdog
- Operator Parameters
- Annex
- DSP402-Parameter
- Integration of the KEB-F5 Powerlink drive in the AutomationStudio of the B&R company
- Display of the KEB parameter address with COMBIVIS
- F5 Operator internal error messages


COMBIVERT F5
Table of contents

COMBIVERT F5
Table of contents
- Preface
- Laws and guidelines
- Table Of Contents
- Table Of Contents
- Basic Safety Instructions
- Electrical connection
- Product Description
- Hardware
- Meaning of the LEDs on the operator
- Diagnostic interface X6B
- Software
- Set addressing with subindex up to software V2.0
- Set-addressing with subindex from software V2.3
- Different coding of the PD mapping subindex
- Synchronous mode
- Figure 4: Operator display: Saut0
- Emergency
- EtherCAT-Watchdog
- Operator parameters
- DSP402-Parameter
- Annex
- Table 3: Operator parameter overview
- Unit desciption by XML files

COMBIVERT F5
Table of contents
- Table Of Contents
- Table Of Contents
- Preface
- Copyright
- Connection and Operation
- Resetting of error messages
- Description of the diagnostic and parameter interface X6B
- Description of the RS232/485 interface X6C
- Customer Parameters (CP-Mode)
- Factory setting for operating mode „GENERAL
- Password input
- Operating Display
- Basic adjustment of the drive
- Special Adjustments
- Factory setting for operating mode „MULTI
- Factory Settings
- Initial Start-up
- Adjustment speed controller
- Factory setting for operating mode „SERVO
- Drive Mode
- Error Assistance
- Quick Guide
- Quick guide for operating mode „MULTI
- Passwords

COMBIVERT F5
Table of contents
- Preface
- Laws and guidelines
- Table Of Contents
- Table Of Contents
- Table Of Contents
- Table Of Contents
- Table Of Contents
- Glossar
- Standards for drive converters / control cabinets
- basic Safety Instructions
- Installation
- electrical connection
- EMC-compatible installation
- Start-up and operation
- Maintenance
- Disposal
- Product Description
- Specified application
- Part code
- Functional Overview
- Interior ventilation
- Mechanical Installation
- Coolant connections of the drive converter
- Wiring diagram cooling system
- Dimensions of the housing
- Fixing points at the housing
- Assembly aids
- Figure 8: Eyebolts
- Assembly in the control cabinet
- Function of the locking levers
- Assembly of the side guide rails
- Positions of the side guide rails in the control cabinet
- Figure 14: Distances
- Installation of the drive converter in the control cabinet
- Figure 16: Transport
- Figure 17: Connect the drive converter housing V with the control cabinet
- Figure 18: Fix the drive converter housing V in the control cabinet
- Figure 19: Drive converter housing V assembled in the control cabinet
- Disassembly from the control cabinet
- electrical Installation
- connection of the shield connection
- Terminal power unit
- Permissible cable cross-sections and tightening torques of the terminals
- Wiring diagram for the Q4 operation
- connection of the control boards
- Wiring diagram for WRA and WRB with F5 control boards
- Wiring diagram for WRA with F5 control board and WRB with F6 control board
- Mains cable types
- Motor connection
- Selection of the motor cable
- Temperature detection T1A, T2A, T1b and T2b
- Use of the temperature input in KTY mode
- connection braking resistor
- External intrinsically safe braking resistor without temperature monitoring
- External braking resistor with overheat protection
- Technical Data
- Electromagnetic compatibility according to EN 61800-3
- electrical data 690 V mains voltage
- Table 5: Technical Data
- electrical data 4000 V mains voltage
- Start-Up
- Switch-on procedures
- Diagram switch-on procedure
- A Annex - Diagrams
- A.3 Power dissipation of the drive converter
- B Annex - Certification
- c Annex - cooling System
- C.1.3 Requirements on the coolant
- C.1.4 Special requirements for open and half-open cooling systems
- C.1.7 Supply of temper coolant
- C.1.9 Fall of pressure at the liquid cooling unit
- C.1.10 Volume flow depending on total power dissipation and temperature difference
- D Annex - Accessories

COMBIVERT F5
Table of contents
- Preface
- Laws and guidelines
- Table Of Contents
- Table Of Contents
- Table Of Contents
- Table Of Contents
- Table Of Contents
- Table Of Contents
- Glossar
- basic Safety Instructions
- Installation
- Electrical connection
- EMC-compatible installation
- Start-up and operation
- Maintenance
- Disposal
- Product Description
- Residual risks
- Type code cabinet system
- Functional overview
- representation of the electrical power unit with higher-level control
- representation of the electrical power unit with braking option
- Structure of the higher-level control
- Structure of the liquid distribution
- Structure of the cabinet air conditioning
- General specifications
- Switching frequency
- Emergency stop function
- Overcurrent and short-circuit protection
- c6 HMI program functionalities
- Data logger
- Overview cabinet system
- System variations
- Cabinet system without sine-wave filter at the output
- Dimensions
- Cabinet system with sine-wave filter at the output
- Mechanical Installation
- check the scope of delivery
- Installation of the cabinet system
- Installation location requirements
- Attach the cabinet system
- Hole distances
- Mounting on the wall
- Installation of the coolant connection
- Electrical Installation
- Shield connection
- Mains connection
- Connection to circuit breaker
- Instructions for installation
- Selection installation of the motor cable
- Selection of the motor cable
- Connection of the motor cable
- connection motor temperature monitoring
- Temperature detection T1B, T2B
- Using the temperature input in the KTY mode
- connection braking resistor
- connection „Safe torque off (STO)
- Technical Data
- Electromagnetic compatibility according to EN 61800-3
- Electrical data 690 V mains voltage
- Start-up
- Structure liquid distribution
- Position stopcock
- Power unit
- Arrangement of the control boards
- Procedure for initial start-up
- Switch-on procedures
- Switch-on procedure diagram
- A Annex - Graphs
- A.3 Power dissipation of the cabinet system
- B Annex - Certification
- c Annex - cooling System
- C.1.2 Requirements on the coolant
- C.1.4 Special requirements for open and half-open cooling systems
- C.1.7 Supply of temper coolant
- C.1.8 Pressure drop of the cabinet system
- C.1.9 Volume flow depending on total power dissipation and temperature difference

COMBIVERT F5
Table of contents
- Table Of Contents
- Introduction
- List of literature
- Diagnostic interface X6B (COMBIVIS)
- Technical data
- Software
- Parameter addressing with 16-Bit PNU plus 16 Bit Subindex (PROFIdrive)
- Set-addressing with subindex
- Error codes of the acyclic communication
- Process data communication (general)
- Process data communication (normal mode)
- Process data mapping
- PROFINET-Name (DCP-Set)
- Diagnosis
- Project Design and Device Description with GSDML File
- Operator Parameters
- Parameter description
- Instructions for F5 PROFINET operator at Simatic S7
- Additional project design for synchronous communication according PROFINET IO-IRT
- Step7 Software
- Cyclic communication (process data)
- Examples for the setting of PD mappings
- Annex


COMBIVERT F5
Table of contents
- Table Of Contents
- Table Of Contents
- Table Of Contents
- General
- Summary of Changes
- Model number information
- Mounting instructions
- Electrical connections
- Disconnect switch
- Line Chokes
- Motor Thermal Protection
- High Voltage Connections
- Technical Data
- Storage of the Unit
- Dimensions and weight
- Summary of the power circuit terminals
- Connection of the power circuit
- Time dependent overload curve
- Low Speed Overload
- Installation and Connection
- Connection of the control signals
- Voltage Input / External Power Supply
- Encoder Connections
- X3A TTL Inc. Enc. In Screw Terminals
- X3A Hiperface Encoder
- X3A EnDat Encoder
- X3A SIN/COS-SSI Encoder
- X3B Incremental Encoder Output
- Operation of the unit
- Parameter Identifi cation
- Changing Parameter Values
- Saving Parameter Values
- Initial Start-up
- Setting The Control Type
- Induction Motor Data
- PM Synchronous Motors
- Auto-Tuning PM motors
- Machine Data
- Encoder Feedback
- Other encoder adjustments
- Speed and Profi le Settings
- Absolute Encoder Setup (no ropes)
- Absolute Encoder Setup (with ropes)
- Absolute Encoder Position Verifi cation
- Encoder Synchronization
- High Speed Tuning
- Feed Forward Torque Control, FFTC
- Synthetic Pre-Torque
- Parameter Description
- Other US parameters
- LF-Elevator Parameters
- Drive confi guration
- Selected motor
- Electronic motor overload protection
- Electronic motor overload current
- Rated motor power
- Rated motor speed
- Rated motor voltage
- Field weakening speed
- Rated motor torque
- PM motor resistance
- Contract speed
- Roping ratio
- Encoder interface
- Encoder pulse number
- Encoder sample time
- Control Mode
- Kp speed accel
- Ki speed
- Max. torque emergency oper
- Open loop torque boost
- Leveling speed, S
- Intermediate Speed 1
- Starting jerk
- Acceleration jerk
- Recommended Profi le Settings
- Speed following error
- Emergency operation mode
- External Load Weigher
- Speed Start Delay
- Encoder resolution multiplier
- Brake engage time
- Software version
- X2A Input state
- X2A Output state
- Inverter load
- Phase current
- Inverter status
- Run Parameters
- Actual torque
- Output voltage
- Output fl ag state
- Analog option raw
- Motor pot
- Motor temperature
- Advanced Adjustments
- Speed for min KI
- Min KP gain at high speed
- Phase current check
- Analog pattern gain
- Analog Output 2 Confi guration
- Input/Output Confi guration
- Digital Output Parameters
- Timing Graph - Analog Control
- Timing Graph - Digital Control
- Elevator Drive Data
- Stator resistance
- Vmax regulation
- Position Control
- Learning the slow down distance
- Min. slowdown dist
- Current position
- Operation Problems
- Diagnostic Solutions
- Drive Faults
- A.1 Parameter List Reference
- A.2 Customer Parameter Values


COMBIVERT F5
Table of contents



COMBIVERT F5
Table of contents

COMBIVERT F5
Table of contents
- Table Of Contents
- Preface
- Copyright
- Pay attention to markings
- Product Description
- Operation TTL with zero singal
- Material number
- Scope of delivery (option or replacement delivery)
- Description of the Interface
- Description of X3A
- Connenction of the encoder Biss + 1 Vpp / EnDat + 1 Vp
- Encoder cable for evaluation without 1 Vpp-signals
- Tested encoders
- Start-up
- Error Messages


COMBIVERT F5
Table of contents
- Preface
- Laws and guidelines
- Table Of Contents
- Table Of Contents
- Table Of Contents
- Table Of Contents
- Table Of Contents
- Glossary
- Standards for drive converters / control cabinets
- Standards that are used in the environment of the drive converter
- Installation
- Product Description
- Repair
- Part code
- Technical Data
- Mechanical ambient conditions
- Electrical operating conditions
- UNIT DATA
- Accessories
- Common mode filter
- DC fuses
- Additional precharging resistor at master-slave operation
- Connection of the COMbIVERT F5-AFE
- Terminal blocks of the units
- External fan power supply for housing size P and U
- Temperature detection T1, T2
- Input and precharging circuits
- Circuit examples
- Circuit example for the power unit with AFE/LCL filter
- Circuit example for the power unit with AFE/LCL filter and common mode filter
- Circuit example for the master-slave operation with AFE/LCL filter and common mode filter
- Circuit example for the control circuit
- Functional description
- Connection of the Control
- Analog inputs
- Relay outputs
- Operation of the Control
- Keyboard operation
- Interface operator
- Description of the RS232/485 interface X6C
- Wiring RS485 full duplex
- Dimensioning
- Technical data of KEb COMbIVERT drive converters
- Table 17: Technical data of KEB COMBIVERT drive converters
- Technical data of KEb COMbIVERT F5-AFE devices
- Maintenance
- Storage
- Cooling System
- Requirements on the coolant
- Coolant temperature
- Connection to the cooling system
- Fall of pressure depending on the rate of flow
- Connection scheme for a cooling circuit (series connection)
- Volume flow in dependence of the heat power dissipation and temperature difference
- Connection scheme for a cooling circuit (parallel connection)
- Revision History

COMBIVERT F5
Table of contents
- Table Of Contents
- Table Of Contents
- Table Of Contents
- General
- Model number information
- Mounting instructions
- Electrical connections
- Disconnect switch
- Line Chokes
- Motor Thermal Protection
- High Voltage Connections
- High Frequency Shielding
- Technical Data
- Technical Data 460V (Size 13 to
- Dimensions and weight
- Summary of the power circuit terminals
- Connection of the power circuit
- Time dependent overload curve
- Low Speed Overload
- Installation and Connection
- Connection of the control signals
- Voltage Input / External Power Supply
- Encoder Connections
- X3A TTL Inc. Enc. In Screw Terminals
- X3A Hiperface Encoder
- X3A EnDat Encoder
- X3A SIN/COS-SSI Encoder
- X3B Incremental Encoder Output
- Operation of the unit
- Parameter Identification
- Changing Parameter Values
- Saving Parameter Values
- Initial Start-up
- Setting The Control Type
- Induction Motor Data
- PM Synchronous Motors
- Auto-Tuning PM motors
- Machine Data
- Encoder Feedback
- Encoder serial com. verification
- Other encoder adjustments
- Running the Motor
- Absolute Encoder Setup (with ropes)
- Absolute Encoder Position Verification
- Encoder Synchronization
- Parameter Description
- Other US parameters
- LF-Elevator Parameters
- Drive configuration
- Selected motor
- Electronic motor overload current
- Rated motor power
- Rated motor speed
- Rated motor voltage
- Field weakening speed
- Rated motor torque
- PM motor resistance
- Contract speed
- Roping ratio
- Encoder interface
- Encoder pulse number
- Control Mode
- Kp speed accel
- Kp current
- Open loop torque boost
- Set Speed S INT1 , Intermediate Speed 2
- Acceleration jerk
- Recommended Profile Settings
- Speed following error
- Emergency operation mode
- Pre-torque gain
- Speed Start Delay
- Encoder resolution multiplier
- Brake engage time
- Software version
- X2A Input state
- X2A Output state
- Inverter load
- Phase current
- Error Messages and Their Cause
- Inverter overheat
- Encoder communication error
- Inverter status
- Run Parameters
- Actual torque
- Output voltage
- Output flag state
- Analog option processed
- Overload counter
- Active Motor Power
- Advanced Adjustments
- Speed for min KI
- Min KP gain at high speed
- Phase current check
- KP synthesized pre-torque
- Serial Com. Baud Rate
- Input/Output Configuration
- Digital Output Parameters
- Timing Graph - Analog Control
- Timing Graph - Digital Control
- Advanced Drive Data
- Vmax regulation
- Position Control
- Learning the slow down distance
- Min. slowdown dist
- A.1 Parameter List Reference
- A.2 Customer Parameter Values

COMBIVERT F5
Table of contents
- Table Of Contents
- Table Of Contents
- Preface
- Validity and liability
- Specified application
- Unit identification
- Installation instructions
- Control cabinet installation
- Safety and application notes
- Technical Data
- Technical data of the 230V class
- Technical data of the 400V class
- DC supply
- Dimensions and weights
- Dimensions Flat Rear (representation with optional mounting kit)
- Mounted version with/without operator
- Terminal strips of the power circuit
- Accessories
- Connection power unit
- Mains connection 3-phase
- Selection of the motor cable
- Temperature detection T1, T2
- Connection of a braking resistor
- Braking resistor with overheat protection
- A.1 Overload characteristic
- A.3 Calculation of the motor voltage
- A.4.3 Cooling circuit
- B.1 Certification
- C.1 Changing the response threshold of the braking transistor


COMBIVERT F5
Table of contents
- Table Of Contents
- Table Of Contents
- Preface
- Copyright
- Part code
- Transport instructions
- Control cabinet installation
- Safety and application notes
- Technical Data
- Technical data of the 230V class
- Technical data of the 400 V class
- DC supply
- Dimensions and Weights
- Through-mount version heat sink with fan (size 24...27)
- Mounted version water-cooled heat sink
- Through-mount version water-cooled heat sink
- Through-mount version water-cooled heat sink with stud
- Through-mount version water-cooled heat sink with stud (small design)
- Through-mount version water-cooled heat sink without stud (small design)
- Terminal strips of the power circuit
- Terminal strips for 230V units
- Connection Accessories
- Connection Power Unit
- Selection of the motor cable
- Temperature detection T1, T2
- Use of the temperature input in KTY mode
- Connection of a braking resistor
- Braking resistor without temperature monitoring
- Braking resistor with over-heat protection without GTR7 monitoring
- External fan power supply
- A.1 Overload characteristic
- A.3 Calculation of the motor voltage
- A.5.1 Cooling circuit
- B.1 Certification
- C.1 Installation of water-cooled units
- C.1.3 Requirements on the coolant
- C.1.4 Connection to the cooling system
- C.1.6 Coolant heating depending on power loss and flow rate with water
- D.1 Changing the response threshold of the braking transistor

COMBIVERT F5
Table of contents
- Table Of Contents
- Table Of Contents
- General
- Model number information
- Mounting instructions
- Electrical connections
- Disconnect switch
- High Voltage Connections
- High Frequency Shielding
- Technical Data
- Dimensions and weight
- Summary of the power circuit terminals
- Connection of the power circuit
- Time dependent overload curve
- Low Speed Overload
- Control Circuit
- Connection of the control signals
- Voltage Input / External Power Supply
- Encoder Connections
- X3A TTL Inc. Enc. In Screw Terminals
- X3A Hiperface Encoder
- X3A EnDat Encoder
- X3B Incremental Encoder Output
- Digital Operator
- Parameter Identification
- Changing Parameter Values
- Keypad Display
- Initial Start-up
- Setting The Control Type
- Measuring the Motor Resistance
- Machine Data
- Controller Settings
- Running the Motor
- Absolute Encoder Setup (with ropes)
- Absolute Encoder Position Verification
- Encoder Synchronization
- Parameter Description
- Other US parameters
- Signal Operating Mode
- Drive Configuration
- Electronic Motor Overload Protection
- Electronic Overload Current
- Rated Motor Speed
- Power Factor
- Rated Motor Torque
- Motor Stator Resistance
- Contract Speed
- Roping Ratio
- Encoder Feedback
- Encoder Sample Time
- Control Method
- Kp Speed
- Kp Current
- Set Speed SI, Inspection Speed
- Set Speed SINT, Intermediate Speed
- Acceleration
- Speed Following Error
- Brake Set Speed
- Pre-torque Direction
- KI Decel
- Absolute Encoder Position
- Current Hold Time
- Software Version
- X2A Input State
- X2A Output State
- Motor Set Speed
- Peak DC Voltage
- Error Messages and their Cause
- Encoder Signal Loss
- Encoder Card Change
- Overload
- Run Parameters
- Actual torque
- Output Voltage
- Output flag state
- Analog option raw
- Motor pot value
- Advanced Adjustments
- Speed for min KI
- Min KP gain at high speed
- Phase current check
- Input/Output Configuration
- Digital Output Parameters
- Parameter List Reference
- Customer parameter values

COMBIVERT F5
Table of contents
- Preface
- Laws and guidelines
- Table Of Contents
- Table Of Contents
- Table Of Contents
- List of Tables
- basic Safety Instructions
- Electrical connection
- Product Description
- List of literature
- Hardware
- Diagnostic interface X6b (cOMbIVIS)
- Software
- Parameter addressing with 16-Bit PNU plus 16 Bit Subindex (PROFIdrive)
- Set-addressing with subindex
- Error codes of the acyclic communication
- Process data communication (general)
- Process data communication (asynchronous mode)
- Profile mode (from SW V3.3)
- DRIVECOM profile mode (Fb.01.Bit9, 8 = 01)
- Process data mapping
- Fieldbus watchdog
- Identification of a device by flashing LED (DCP-set)
- Diagnosis
- Address several IP devices
- File
- Operator Parameters
- Parameter description
- Instructions for F5 PROFINET operator to Simatic S7
- Install GSD files
- Configure object properties as sync master
- Additional project design for synchronous communication according PROFINET IO-IRT
- Set KEB slave as Sync slave
- Set synchronization role
- Synchronous alarms
- IO-cycle characteristics
- Step7 Software
- Annex
- Examples for the setting of PD mappings
- x 32-bit Pdout plus 4 x 16-bit Pdin


COMBIVERT F5
Table of contents
- Preface
- Laws and guidelines
- Table Of Contents
- Table Of Contents
- Table Of Contents
- Table Of Contents
- Table Of Contents
- Table Of Contents
- Glossary
- Standards for drive converters / control cabinets
- Standards that are used in the environment of the drive converter
- basic Safety Instructions
- Installation
- electrical connection
- EMC-compatible installation
- Start-up and operation
- Maintenance
- repair
- Product Description
- Product features
- Part code
- Technical Data
- Mechanical environmental conditions
- Electrical operating conditions
- Block diagram of energy flow in the device
- Technical data 400V class
- Table 7: Technical data of the 400V class - Single Drive
- Master / slave system
- Table 8: Technical data of the 400 V class master / slave
- Master / slave / slave system
- Table 9: Technical data of the 400 V class master / slave / slave
- Technical data 690V class
- Table 10: Technical data of the 690V class - Single Drive
- Table 11: Technical data of the 690 V class master / slave
- Table 12: Technical data of the 690 V class master / slave / slave
- Dimensions and weights
- Dimensions air-cooled inverter through-mount version
- Dimensions liquid cooler through-mount version
- Dimensions liquid cooler installation version
- Dimensions liquid cooler built-in version with stainless steel tube
- Mechanical Installation
- Assembly aids
- cooling system
- Air cooler
- Liquid cooling
- Series connection cooling circuit
- Connection diagram series connection cooling circuit
- Parallel connection of the coolant circuit
- Operation of liquid-cooled devices
- Materials in the cooling cicuit
- Requirements on the coolant
- Requirements for open and half-open cooling systems
- Supply of temper coolant
- Diagrams of the cooling design
- Pressure drop aluminium heat sink with stainless steel tubes
- Series connection of liquid coolers
- Parallel connection of liquid coolers
- electrical Installation
- Connection of the shield connection
- connection terminals power unit
- External fan power supply
- Mains connection
- Motor connection
- Recommended type of the motor cable
- Cable cross-sections
- Motor cable lengths
- Dc connection
- Temperature detection T1, T2
- Use of the temperature input in KTY mode
- connection of a braking resistor
- Monitoring braking transistor
- External braking resistor with overtemperature protection
- connection of the master / slave wiring
- Figure 25: Master / slave connections
- Connection master / slave / slave
- Figure 28: Master / slave / slave connections
- Wiring Diagrams
- Unit size 32...35
- Connection braking resistor master / slave system
- DC connection master / slave system
- Mains connection master / slave system
- Unit size 36...39
- Connection braking resistor master / slave / slave system
- DC connection master / slave / slave system
- Mains connection master / slave / slave system
- Protection of drive converters
- Certification
- Table 30: External filters and chokes
- Table 31: UL fuses
- Further informations and documentation
- characteristics
- Power dissipation of the 400V class at rated operation
- Power dissipation of the 690V class at rated operation
- Power dissipation at 4 kHz switching frequency
- Accessories
- revision History


COMBIVERT F5
Table of contents
- Table Of Contents
- Table Of Contents
- Preface
- Copyright
- Product description
- Installation instructions
- Control cabinet installation
- Safety and operating instructions
- Technical Data
- Technical Data of the 230 V Class
- Technical Data of the 400 V Class
- DC supply
- Dimensions and Weights
- Permissible cable cross-sections and tightening torques of the terminals
- Accessories
- Connection Power Unit
- Selection of the motor cable
- Connection of the motor
- Use of the temperature input
- Connection of a braking resistor
- A.1 Overload characteristic
- A.3 Calculation of the motor voltage
- B.1 Certification
- D.1 Changing the response threshold of the braking transistor

COMBIVERT F5
Table of contents
- Table Of Contents
- Introduction
- Safety and Operating Instructions
- Overview of control connections
- Motor encoder connection X3A
- Hiperface encoder interface
- BISS encoder interface
- Wiring examples / flow charts
- Connection F5-Lift for ogive travel with correction input (Lb.05=1, Lb.12=9)
- Control terminal strip X2A
- Lift-Operator
- The Operator Panel
- Parameter description
- Lift functions
- Positioning mode
- Information, indications and measured values
- Adjustment of analog inputs and outputs
- Start-up
- Start-up of an asynchronous motor with speed encoder and gearbox
- Start-up of a synchronous motor with speed encoder without gearbox
- Error diagnosis
- Adjustment Speed Controller of F5 Lift with "speed jump

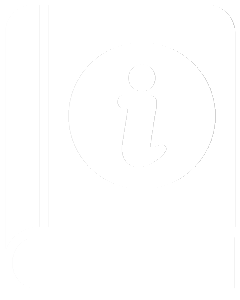
manualsdatabase
Your AI-powered manual search engine