YASKAWA Varispeed f7 manuals

Varispeed f7
Table of contents
- general precautions
- safety information
- safety precautions
- trial operation
- warranty information
- Table Of Contents
- Table Of Contents
- Table Of Contents
- Table Of Contents
- Table Of Contents
- Table Of Contents
- Table Of Contents
- Table Of Contents
- Varispeed F7 Introduction
- Confirmations upon Delivery
- inverter specifications
- Component Names
- Exterior and Mounting Dimensions
- Enclosed Wall-mounted Inverters [NEMA1 (Type 1)]
- Checking and Controlling the Installation Site
- Installation Orientation and Space
- Removing and Attaching the Terminal Cover
- Removing/Attaching the Digital Operator and Front Cover
- removing the front cover
- Inverters of 22 kW or More
- Removing and Attaching the Protection Cover
- Attaching the Protection Cover
- Wiring
- Connections to Peripheral Devices
- Connection Diagram
- Terminal Block Configuration
- Wiring Main Circuit Terminals
- Main Circuit Terminal Functions
- Main Circuit Configurations
- Standard Connection Diagrams
- Wiring the Main Circuits
- ground wiring
- Wiring Control Circuit Terminals
- wiring method
- Control Circuit Terminal Functions
- Control Circuit Terminal Connections
- Control Circuit Wiring Precautions
- Wiring Check
- Installing and Wiring Option Boards
- Installation
- PG Speed Control Board Terminals and Specifications
- Wiring Terminal Blocks
- Selecting the Number of PG (Encoder) Pulses
- Digital Operator and Modes
- Digital Operator
- Modes
- Switching Modes
- Drive Mode
- Quick Programming Mode
- Advanced Programming Mode
- Verify Mode
- Autotuning Mode
- Trial Operation
- Trial Operation Procedure
- Trial Operation Procedures
- Checking the Display Status
- Basic Settings
- Settings for the Control Methods
- Autotuning
- Application Settings
- Check and Recording User Constants
- Adjustment Suggestions
- User Constants
- User Constant Descriptions
- Digital Operation Display Functions and Levels
- User Constants Settable in Quick Programming Mode
- User Constant Tables
- Application Constants: b
- Autotuning Constants: C
- Reference Constants: d
- Motor Constant Constants: E
- Option Constants: F
- Terminal Function Constants: H
- Protection Function Constants: L
- N: Special Adjustments
- Digital Operator Constants: o
- T: Motor Autotuning
- U: Monitor Constants
- Factory Settings that Change with the Control Method (A1-02)
- Factory Settings that Change with the Inverter Capacity (o2-04)
- Constant Settings by Function
- Application and Overload Selections
- carrier frequency
- Frequency Reference
- Using Multi-Step Speed Operation
- Varispeed F7 Function Block
- Run Command
- Stopping Methods
- Using the DC Injection Brake
- Using an Emergency Stop
- Acceleration and Deceleration Characteristics
- Accelerating and Decelerating Heavy Loads (Dwell Function)
- related parameters
- Adjusting Frequency References
- Operation Avoiding Resonance (Jump Frequency Function)
- Adjusting Frequency Reference Using Pulse Train Inputs
- Speed Limit (Frequency Reference Limit Function)
- Improved Operating Efficiency
- Hunting-prevention Function
- Stabilizing Speed (Speed Feedback Detection Function)
- Machine Protection
- Preventing Motor Stalling During Operation
- Changing Stall Prevention Level during Operation Using an Analog Input
- Detecting Motor Torque
- Changing Overtorque and Undertorque Detection Levels Using an Analog Input
- Motor Overload Protection
- Setting Motor Protection Operation Time
- Motor Overheating Protection Using PTC Thermistor Inputs
- Limiting Motor Rotation Direction
- Continuing Operation
- Speed Search
- Continuing Operation at Constant Speed When Frequency Reference Is Lost
- Inverter Protection
- Reducing Inverter Overheating Pre-Alarm Warning Levels
- Input Terminal Functions
- Blocking Inverter Outputs (Baseblock Commands)
- Stopping Acceleration and Deceleration (Acceleration/Deceleration Ramp Hold)
- Raising and Lowering Frequency References Using Contact Signals (UP/DOWN)
- Hold Analog Frequency Using User-set Timing
- Jog Frequency Operation without Forward and Reverse Commands (FJOG/RJOG)
- Output Terminal Functions
- Monitor Constants
- Using Pulse Train Monitor Contents
- Individual Functions
- communications connection terminal
- message format
- monitor data
- enter command
- error codes
- Using the Timer Function
- Using PID Control
- monitor functions
- Energy-saving
- Setting Motor Constants
- Setting the V/f Pattern
- Torque Control (SPEC: E or Later Only)
- Speed Control (ASR) Structure
- fine adjustments
- Droop Control Function (SPEC: E or Later Only)
- Zero-servo Function (SPEC: E or Later Only)
- Digital Operator Functions
- Copying Constants
- Prohibiting Writing Constants from the Digital Operator
- Displaying User-set Constants Only
- Options
- Using Digital Output Boards
- Using an Analog Reference Board (SPEC: E or Later Only)
- Using a Digital Reference Board (SPEC: E or Later Only)
- Using Inverters for Elevating Machines
- Stall Prevention during Deceleration
- I/O Open-phase Protection and Overtorque Detection
- Control-related Adjustments
- Reducing Shock during Elevating Machine Start, Stop, Acceleration and Deceleration
- Confirming Startup Current and Reducing Carrier Frequency
- Troubleshooting
- Protective and Diagnostic Functions
- Alarm Detection
- Operation Errors
- Errors During Autotuning
- Errors when Using the Digital Operator Copy Function
- If the Motor Does Not Operate
- If the Direction of the Motor Rotation is Reversed
- If the Slip Compensation Function Has Low Speed Precision
- If the Motor Overheats
- If There is Noise When the Inverter is Started or From an AM Radio
- If the Torque Generated for the Motor is Insufficient (Insufficient Power)
- If the Motor Rotates Even When Inverter Output is Stopped
- Maintenance and Inspection
- Periodic Maintenance of Parts
- Types and Number of Cooling Fans Used in the Drive
- Cooling Fan Replacement Outline
- Circulation Fan Replacement Outline
- Removing and Mounting the Control Circuit Terminal Board
- Specifications
- Standard Inverter Specifications
- Common Specifications
- Specifications of Options and Peripheral Devices
- Appendix
- Varispeed F7 Control Methods
- Control Methods and Applications
- Inverter Application Precautions
- Motor Application Precautions
- Using the Inverter for Special Motors
- Conformance to UL Standard
- Conformance to CE Markings
- wiring example
- emc directive
- Wiring Examples
- Using a Braking Unit and Braking Resistor Unit
- Using Braking Units in Parallel
- Using a Braking Unit and Three Braking Resistor Units in Parallel
- Using a VS Operator
- with an Internal Power Supply
- Using Transistors for Input Signals and a +24-V Common in Sourcing Mode
- Using Transistors for Input Signals and a 0-V Common in Sinking Mode with an External Power Supply
- Using Contact and Open Collector Outputs
- revision history

Varispeed f7
Table of contents
- Table Of Contents
- Table Of Contents
- Table Of Contents
- Table Of Contents
- F7 Model Number, Enclosure, Heat Loss, and Weight
- Confirmations upon Delivery
- Component Names
- Exterior and Mounting Dimensions
- Checking and Controlling the Installation Site
- Installation Orientation and Clearances
- Removing and Attaching the Terminal Cover
- Removing/Attaching the Digital Operator and Front Cover
- Chapter 2 - Electrical Installation
- Terminal Block Configuration
- Wiring Main Circuit Terminals
- Control Wiring
- Electromagnetic Compatibility (EMC)
- Installing and Wiring Option Boards
- Chapter 3 - Digital Operator
- Digital Operator Display
- Digital Operator Keys
- Drive Mode Indicators
- Drive Main Menus
- Quick Setting Menu (-QUICK-)
- Programming Menu (-ADV-)
- Example of Changing a Parameter
- Chapter 4 - Start-Up
- Drive Start-Up Preparation
- Drive Start-Up Procedures
- Chapter 5 - Basic Programming
- Description of Parameter Tables
- Speed Command Source
- Run Command Source
- Stopping Method
- Accel/Decel Time
- Carrier Frequency
- Preset Reference
- Input Voltage Setting
- Motor Setup
- Analog Output Gain
- Motor Overload Fault
- Stall Prevention
- Chapter 6 - Diagnostics & Troubleshooting
- Fault Detection
- Alarm Detection
- Operator Programming Errors (OPE)
- Auto-Tuning Faults
- Digital Operator COPY Function Faults
- Troubleshooting
- Peripheral Devices
- Main Circuit Test Procedure
- Drive Date Stamp Information
- Chapter 7 - Maintenance
- Preventive Maintenance
- Periodic Maintenance of Parts
- Heatsink Cooling Fan Replacement
- Removing and Mounting the Terminal Card
- Appendix A - Parameters
- F7 Parameter List
- F7 Monitor List
- F7 Fault Trace List
- Drive Capacity Selection
- Parameters Affected by Drive Capacity Setting
- Standard Drive Specifications
- Appendix D - Communications
- Using Modbus Communication
- Modbus Function Code Details
- Modbus Data Tables
- Modbus Self-Diagnosis

Varispeed f7
Table of contents
- Introduction
- Safety Precautions
- installation and wiring
- Warranty Information
- Restrictions
- Table Of Contents
- Overview
- Parts List
- Communications Connectors
- Switch Setting
- Installation and Wiring
- MECHATROLINK Communications Cables
- Transmission Interface
- Basic Format of Data Transfer
- Communications Phases
- Application Layer Specifications
- Initial Setup
- MECHATROLINK-II Commands
- Sub-commands
- Status Details
- Protective Operations
- Alarm Processing
- specifications
- revision history

Related products
VIPA SPEED7SPEED7 CPU-SC 313-5BF23VIPA SLIO FM 050VIPA SLIO FM 050-1BB00FM 054FM 050FM 250SSI-EP3/VS-V SeriesVIPA IM 053IPYASKAWA categories
Controller
DC Drives
Servo Drives
Inverter
Touch Panel
Robotics
Control Unit
Industrial Equipment
Media Converter
Industrial Electrical
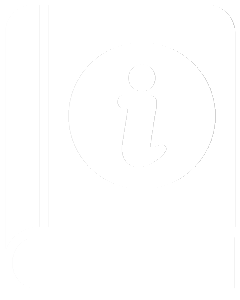
manualsdatabase
Your AI-powered manual search engine