Panasonic FP7 Series manuals

FP7 Series
Table of contents
- Table Of Contents
- Table Of Contents
- Table Of Contents
- Table Of Contents
- Overview of Functions
- For Using Logging and Trace Functions
- Selection of SD Memory Cards
- Overview of Trace Function
- Format of Saved Files
- File Format (For Trace Function)
- Data Format
- Configuration
- Definition of Buffer Memory
- Logging Information Setting
- LOG FIle Setting Items (For Logging)
- Trace Information Setting
- LOG FIle Setting Items (For Trace)
- Registration of Device Information
- Operation When Setting Cycle for Logging Trigger
- Downloading Setting Data to CPU Unit
- Saving to SD Memory Card (In SD Memory Card Operation)
- Precautions on Downloading Setting Data
- Start-Stop and Monitor
- Start and Stop of Logging/Trace Operation
- Start and Stop with Instructions
- Operation Check Using Logging/Trace Monitor
- System Relays Relating to Logging/Trace Operation
- System Data Registers Relating to Logging/Trace Operation
- Operation Check Using System Monitor
- Logging Operation
- Flow of Logging Operation
- Operation When Logging is Selected for Application
- Operation When the Card Cover of CPU Unit Opens
- Operation When the Number of Determination Files Reaches the Maximum Number of Generations
- System Management Information Relating to Logging Function
- Trace Operation and Time Chart
- Flow of Trace Operation
- Operation When Trace is Selected for Application
- Trace Monitor (Time Chart)
- Explanation of Time Chart Monitor
- Restrictions on Time Chart Monitor
- Troubleshooting
- Operations When Errors Occur
- Operations When Inserting/Removing SD Memory Card During Logging/Trace
- Error of Logging/Trace

FP7 Series
Table of contents
- Table Of Contents
- Table Of Contents
- Overview
- Restrictions on unit combination
- Parts and functions
- FP7 PROFIBUS DP Master
- FP7 DeviceNet Master
- FP7 CANopen Master
- FP7 PROFINET IO-Controller
- Installation and wiring
- Attaching units
- Using DIN rails
- Wiring of the FP-FMU Connectors
- Programming information
- FMU_DataExchange
- dutNetworkStatus output
- GlobalBusStateField for PROFIBUS
- GlobalBusStateField for DeviceNet
- GlobalBusStateField for CANopen
- GlobalBusStateField for PROFINET IO
- Slaves_abIsConfigured output
- abSl_cfg for PROFIBUS
- Slaves_abIsConnected output
- abSI_Con for DeviceNet
- Slaves_abHasDiagnostic output
- abSl_diag for DeviceNet
- abSl_diag for CANopen
- SlaveDiagnostic_bIsDone Output
- SlaveDiagnostic_awData Output
- awDiagData for PROFIBUS
- awDiagData for DeviceNet
- awDiagData for CANopen
- awDiagData for PROFINET IO
- Specifications
- Dimensions

FP7 Series
Table of contents
- Table Of Contents
- Security Function
- Overview of Security Function
- Target Items of Security Functions
- Password Protection Function
- How to Set Password (2) User Privileges
- Reading Project that Password Has Been Set (1) Administrative Previleges
- Reading Project that Password Has Been Set (2) User privileges
- Cancelling Password
- Limited Distribution Password
- Upload Protection Setting
- Cancelling Upload Protection Setting
- Encryption Setting
- Confirming Encrypted State (Decryption)
- Changing or Deleting Encryption Key
- How to Set Encryption Keyword for PLC (1)
- How to Set Encryption Keyword for PLC (2)
- Cancelling Security Setting
- Restrictions on SD Memory Card Operation and Copy Operation

FP7 Series
Table of contents
- Table Of Contents
- Table Of Contents
- Table Of Contents
- Table Of Contents
- Table Of Contents
- Table Of Contents
- Table Of Contents
- Table Of Contents
- Table Of Contents
- Table Of Contents
- Unit Functions and Restrictions
- Functions of Motion Control
- List of Models
- Restrictions
- Restrictions by Power Consumption in FP7 System
- System Configuration
- Type of Software
- Mechanism of Processing
- Operation When Powe Supply Turns On
- Names and Functions of Parts
- Operation monitor LEDs
- ESM (State Transition Diagram)
- Installation and Wiring
- Settings of Servo Amplifier A5B
- Connection of Input Signals
- Connection of Network
- Basic Procedure
- Section Details
- Registration in I/O Map
- Download of I/O map
- Confirmation of Slot Numbers
- Setting of Used Axes
- Setting of Network Configuration
- Registration of Slaves (Online)
- Setting of Station Addresses and Axis Numbers
- Download to FP7 MC Unit
- Restarting Power Supplies and Checking Communication State
- Connection of Limit and Near Home Switches
- Pin Assignment Setting of Servo Amplifier
- Checking Servo Amplifier Input State
- Settings of FP7 MC Unit
- Saving and Managing Files
- Export to CSV Files
- MC Common Settings
- MC Common Settings Parameters
- Axis Parameter Settings
- Axis Parameters (Basic Setup)
- Axis Parameters (Options)
- Axis Parameters (Operation)
- Positioning Table Setting
- Operation Patterns and Tables
- Synchronous Parameter and Cam Pattern Settings
- Cam Pattern Setting
- Confirmation of Setting Contents
- Transfer of Parameters
- Data Transfer to MC Unit and Test Operation
- Before Turning On the Power
- Procedure for Turning On the Power
- Checking While the Power is ON
- Checking Network Communication State
- Checking the safety circuit by the PLC unit
- Checking the Operation of Near Home Switch
- Monitor Function of CMI
- Data Monitor
- Tool Operation Function of CMI
- Serve ON/OFF with Tool Operation Function
- JOG Operation with Tool Operation Function
- Home Return by Tool Operation Function
- Positioning by Tool Operation Function
- Teaching by Tool Operation Function
- Creation of User Programs
- How to Create User Programs
- Overview of Programs
- Servo ON/OFF Control Program
- Start Enabled Program
- Writing Data to Output Control Area
- Precautions On Programming
- Automatic Operation (Position Control)
- Basic Operation
- Setting and Operation of E-point Control
- Setting and Operation of P-point Control
- Setting and Operation of C-point Control
- Setting and Operation of J-point Control
- Interpolation Control
- Type of Interpolation Control (Three-axis Interpolation)
- Setting and Operation of Two-Axis Linear Interpolation
- Setting and Operation of Two-Axis Circular Interpolation
- Setting and Operation of Three-Axis Linear Interpolation
- Setting and Operation of Three-Axis Spiral Interpolation
- Repeat Function
- Stop Operation During Repeat Operation
- Setting and Operation of Repeat
- Sample Programs
- Rewriting Positioning Data by User Programs
- Procedure of Rewriting
- Sample Program (Rewritign Positioning Tables)
- Automatic Operation (Synchronous Control)
- Synchronous Control
- Settings for Master and Slave Axes
- Selection of Slave Axes and Settings
- Setting by CMI
- Start and Cancel of Synchronous Control
- Precautions When Canceling or Starting Synchronous Control
- Electronic Gear Function
- Types and Contents of Setting Parameters
- Gear Ratio Changes while in Operation
- Electronic Clutch Function
- Trigger Types for Electronic Clutch
- Engagement Method of Electronic Clutch
- Electronic Cam Function
- Cam Pattern Setting Method
- Manual Operation (JOG Operation)
- Setting and Operation of Home Return
- Changing Speed During JOG Operation
- Setting and Operation of JOG Inching Operation
- Manual Operation (Home Return)
- Types of Home Return
- Operation of Home Return
- Stop Functions
- Type of Stop Functions
- Characteristics of Pause Function
- Settings Related to Stop Function
- Axis Parameter
- Operation During Stop
- Supplementary Functions
- Dwell Time
- Software Limit
- Auxiliary Output Code and Auxiliary Output Contact
- Current Value Update
- Home Coordinates
- Movement Amount Automatic Check
- Monitor Error (Torque / Actual Speed Judgement)
- EtherCAT Communication Setting
- Device Editor
- Overview of PDO Mapping
- Change of PDO Mapping
- EC Packet Monitor Function
- How to Set
- How to Execute
- Troubleshooting
- Errors and Warnings
- Clearing Errors/Warnings Using User Programs
- Error and Warning Logs
- Error Recovery Process
- Error Code Table
- Axis Operation Errors (From 00F0 3000H)
- Setting Value Errors (From 00F0 4000H)
- Synchronous Parameter Setting Errors (From 00F0 5000H)
- Warning Code Table
- Specifications
- Communication Specifications
- Performance Specifications
- I/O Allocation
- Whole Configuration of Unit Memories
- Unit Memories (Input and Output Control Areas)
- Configuration of Output Control Area
- List of Input Control Area Functions
- List of Output Control Area Function
- Unit Memories (Common Area)
- Setting Parameter Control Area
- Axis Group Setting Area
- Current Value Update Data Area
- Positioning Control Starting Table Number Setting Area
- Error Annunciation and Clear Area
- Warning Annunciation and Clear Area
- Synchronous Control Monitor Area
- Unit Memories (Each Axis Information Area)
- Each Axis Information & Monitor Area
- Unit Memories (Each Axis Setting Area)
- Configuration of Parameter Setting Area
- Parameter Setting Area
- Configuration of Positioning Data Setting Area
- Unit Memories (Synchronous Control Setting Area)
- Sychronous Control Setting Area
- Electronic Gear Setting Area
- Electronic Cam Setting Area
- Dimensions

FP7 Series
Table of contents
- Table Of Contents
- Table Of Contents
- Table Of Contents
- Table Of Contents
- Table Of Contents
- Table Of Contents
- Table Of Contents
- Unit Functions and Restrictions
- Unit Functions and Operation
- Unit Type and Product Number
- Restrictions on Units Combination
- Restrictions on Interrupt Function
- Restrictions on I/O Allocation
- Names and Functions of Parts
- Operation monitor LEDs
- Input/Output Specifications and Wiring
- Input/Output Specifications
- Input Specifications
- Output Specifications
- Wiring of Input and Output
- Output Wiring
- Connection over Wire-pressed Terminal Cable
- Unit Allocation
- Registration in I/O Map
- Multi I/O Unit Setting
- Basic Setup
- Output Terminal Setting
- Allocation of Contacts to Output Terminals
- Application to Differential Output
- Application Setting
- Setting Items by Use
- Interrupt Function
- Overview of Interrupt Program
- Precautions for Use
- Execution Example of Interrupt Function
- Comparison Match Interrupt
- Counter Function
- Configuration Using Tool Software
- Linear Counter and Ring Counter
- Selection of Count Methods
- Control Signals
- Read/Write of Elapsed Value
- Elapsed Value Hold Function
- Operation
- Input Frequency Measurement Function
- Comparison Output Function
- Comparison Output and Comparison Match Signal
- Execution Example of Comparison Output Function
- Pulse Output / PWM Output Function
- Pulse Output Function Settings
- Data Update Timing (Output Frequency)
- Data Update Timing (Duty Ratio)
- Read/Write of PLS/PWM Counter Elapsed Value
- Execution Example of Pulse Output / PWM Output Function
- Setting Example of Pulse Output (Frequency Change)
- Setting Example of Pulse Output (Comparison Match Stop)
- Setting Example of PWM Output
- Positioning Function (H type)
- Positioning Function
- Control Mode
- Wiring
- Connections with Servo Motor Amplifier
- Connection with Stepping Motor Driver
- Initial Operation Check
- Before Turning On the Power
- Power-on and Power-off Sequences
- After Turning On the Power
- Setting of Positioning Function
- Positioning Table Settings (Configurator PMX)
- Parameter Settings
- Creating Positioning Data Table
- Saving Positioning Parameters
- Check on Parameter Data
- Stop Control
- Characteristics of Stop Operations
- JOG Operation
- Setting and Operation of JOG Operation (Speed Changes)
- Speed Changes in JOG Operation
- Home Return
- Operation Patterns of Home Return Operation
- Settings and Operations of Home Return
- Positioning Control
- E-point Control (Single Speed Positioning)
- P-point Control (Double Speed Positioning)
- C-point Control
- J-point Control (JOG Positioning)
- J-point Control (JOG Positioning: Speed Changes)
- Cautions on Programming
- Repeat Operation
- Settings and Operations of Repeat Operation
- Stop Operation During Repeat Operation
- Linear Interpolation Control
- Setting and Operation of Linear Interpolation
- Operational Difference Between Speed Parameters
- Operation Patterns and Start Speed Settings
- Other Characteristics
- Other Functions
- Creating of Ladder Programs Using Templates
- Creating Reading/Writing Program
- Troubleshooting
- Confirming Errors Using Self-diagnostic Function
- Operation Mode When an Error Occurs
- What to Do When Positioning Error Occurs
- ERR LED is Flashing on the Unit
- Specifications
- Function Specifications ( AFP7MXY32DWD/ AFP7MXY32DWDH)
- Positioning Function Specifications (AFP7MXY32DWDH)
- Allocation of I/O Numbers
- Output
- List of Unit Memories
- List of Unit Memories (AFP7MXY32DWD/ AFP7MXY32DWDH)
- List of Unit Memories (AFP7MXY32DWDH)
- Unit Memory Detailed Information
- Input Setting
- Output Setting
- Interrupt Setting Area
- Counter Mode Setting Area
- Counter Monitor Setting Area
- Comparison Output Setting Area
- Pulse Output / PWM Output Setting Area
- Pulse Output / PWM Output Monitor Setting Area
- Unit Memory Detailed Information (H type)
- Axis Information Area
- Axis Setting Area

FP7 Series
Table of contents
- Table Of Contents
- Table Of Contents
- Table Of Contents
- Table Of Contents
- Table Of Contents
- Unit Functions and Restrictions
- Unit Functions and How They Work
- Unit Type and Product Number
- Restrictions on Combinations of Units
- Names and Functions of Parts
- Wiring and Input/Output Specifications
- Connection over Wire-pressed Terminal Cable
- Assembly of Connector for Wire-pressed Terminal Cable
- Terminal Circuit Diagram
- Input/Output Specifications
- Precautions on Wiring and Connection of Count Input
- For Transistor Open Collector Type of Encoder Input
- Unit Allocation and Parameter Settings
- Unit Allocation
- Number of Occupied Points of High-speed Counter Unit
- Registration in I/O Map
- Configuration of High-speed Counter Unit
- Configuration Data Setting Items
- Configuration Data and Operation Ready Request
- Downloading Configuration Data
- Configuration Using User Programs
- Count Function
- Selection of Counters and Basic Settings
- Linear Counter and Ring Counter
- Selection of Count Methods
- Types of Count Operations
- Simple Count Operation
- Reset Count Operation
- Enable Count Operation
- Enable Reset Count Operation
- Enable Preset Count Operation
- Allocation of Reset, Preset and Enable Signals
- Preset Input
- Enable Input
- Reading Count Value and Changing Current Value
- Reading Count Value
- Input Time Constant Setting Function
- Measurement Function
- Overview of Measurement Function
- Configuration
- Reading Measuring Results
- Comparison Function
- Overview of Comparison Function
- Target Value Match Comparison and Band Comparison
- Operation of Target Value Match Function
- Examples of Ring Counter Settings
- Configuration of Target Value Match Comparison
- Operation of Band Comparison Function
- Configuration of Band Comparison
- External Output
- Output Pattern Setting (Only for Band Comparison)
- Forced Output Function
- Capture Function
- Overview of Functions
- Restrictions on Combinations
- Operations of Capture Function
- Continuous Operation
- Operations of Sampling Capture Function
- Operations of Buffer Function
- Reading Capture Data
- Reading Buffer Area Data
- Operation and Readout of Capture Done Flag (X4/X5)
- Reference Information (Manual Reset of Capture Done Flag)
- Clearing Capture Values Storage Area
- Interrupt Program Activation Function
- Precautions for Use
- What to Do If an Error Occurs
- Self-diagnostic Function
- Clearing Errors Using User Programs
- List of Error Codes
- Errors Occurred in Operations (1000H to 1043H)
- Specifications
- Function Specifications
- Allocation of I/O Numbers
- List of Unit Memories
- Unit Memory Detailed Specifications
- Monitor Display Area
- Capture Value Buffer Area
- Dimensions

FP7 Series
Table of contents
- Table Of Contents
- Unit Functions and Restrictions
- Unit Functions and How They Work
- Restrictions on Combinations of Units
- Specifications
- Analog I/O Cassette and Analog Input Cassette
- Output Specifications (AFP7FCA21)
- Switch Settings
- Wiring
- Input Conversion Characteristics (AFP7FCA21 / AFP7FCAD2)
- Output Conversion Characteristics (AFP7FCA21)
- Thermocouple Input Cassette
- I/O Allocation and Programs
- I/O Allocation
- Sample Programs

FP7 Series
Table of contents
- Table Of Contents
- Table Of Contents
- Table Of Contents
- Table Of Contents
- Table Of Contents
- Communication Functions of CPU Unit
- Communication Ports of CPU Unit
- Communication Functions Supported by Each Port
- Overview of Communication Functions
- MEWTOCOL Master/Slave Communication
- MODBUS RTU Master/Slave Communication
- General-Purpose Communication
- Wiring the COM. Port
- Attaching a Communication Cassette
- Wiring of COM Port Terminal Block
- Applicable Cable
- Wiring Method
- Wiring for CPU Unit (GT Power Supply and COM0 Port)
- Wiring for Communication Cassettes COM1 and COM2 ports
- Communication Cassette AFP7CCS2 (RS-232C, 2-channel insulated type)
- Communication Cassette AFP7CCM2 (RS-422 / RS-485, 2-Channel Insulated Type)
- Communication Cassette AFP7CCS1M1 (RS-232C 1-Channel +
- Setting and Confirming Communication Conditions
- Setting Applications and Communication Conditions
- Settings Using Tool Software FPWIN GR7
- Input/Output Signals Used for Communication
- PLC Link
- Operation of PLC link MEWNET-W0
- Operation of Link Relays and Link Registers
- Configuration Required for PLC Link
- List of Setting Items
- Setting Items for PLC Link
- Response Time of 1 Transmission Cycle
- Response Time When There is a Station Yet to be Added
- Configuration
- List of MEWTOCOL / MEWTOCOL7 Supporting Commands
- MEWTOCOL-COM Master Communication (RECV)
- RECV Command (When MEWTOCOL-COM is Used)
- MEWTOCOL-COM Master Communication (SEND)
- SEND Command (When MEWTOCOL-COM is Used)
- List of MODBUS RTU Supported Commands
- MODBUS RTU Master Communication (RECV)
- RECV Command (MODBUS Function Code Specified Type)
- RECV Command (MODBUS Function Code Unspecified Type)
- MODBUS RTU Master Communication (SEND)
- SEND Command (MODBUS Function Code Specified Type)
- SEND Command (MODBUS Function Code Unspecified Type)
- Operation of General-Purpose Communication
- Sending Operation
- Contents of Sent Data
- GPSEND (General-Purpose Communication Sending Command)
- Precautions on Sending Data
- Receiving Operation
- Contents of Received Data
- Operations of the "Reception done copy" flag and multiplex reception
- GPRECV (General-Purpose Communication Receiving Command)
- Sending/Receiving Flag Operation
- Start Code "STX", End Code "ETX":
- Specifications
- Communication Function Specifications
- Extension Cassette Communication Specifications
- MEWTOCOL-COM Format
- MEWTOCOL-COM Response Format
- MEWTOCOL7-COM Format
- MEWTOCOL7 Response Format
- MODBUS RTU Format
- MODBUS RTU Response Format

FP7 Series
Table of contents
- Table Of Contents
- Table Of Contents
- Table Of Contents
- Unit Functions and Restrictions
- Unit Functions and Operation
- Basic Operation of Analog Input Processing
- Restrictions on Units Combination
- Names and Functions of Parts
- Analog Input Unit
- Wiring
- Wiring of Terminal Block
- Connecting Analog Input
- Current Input (0 to +20, +4 to +20 mA)
- Connecting Trigger Input Terminal TRIG
- Unit Settings and data Reading
- Confirming the I/O Number Allocations and First Word Number
- Confirming the I/O Number Allocations
- Option settings
- Unit Setting and Conversion Processing Time
- Reading Analog Input Data
- Data Acquisition Timing
- Conversion Characteristics of Analog Input Unit
- Voltage Range
- Voltage Input Range: 0 to +10 V (0.32 mV, 1/31,250)
- Voltage input range: 1 to 5 V (0.16 mV, 1/25,000)
- Current Range
- Optional Settings for Analog Input
- Average Processing Settings
- Time Average
- Moving Average
- Offset/Gain processing
- Scale Conversion
- Comparison for Upper and Lower Limits
- Holding Max./Min. Values
- Disconnection detection
- Buffer Settings
- Buffering by Trigger Output Relay
- Buffering by External Input Trigger
- Buffering Triggered by Value Change in Analog Input
- Configuration by Programming
- What to Do If an Error Occurs
- What to Do If an Error Occurs (Analog Input)
- Specifications
- I/O Allocation
- List of Unit Memories
- List of Detailed Specifications of Unit Memories
- Dimensions

FP7 Series
Table of contents
- Table Of Contents
- Table Of Contents
- Table Of Contents
- Table Of Contents
- Table Of Contents
- System Configuration
- Unit Functions and Types
- Unit Type
- Network Type
- MEWNET-F
- Function Overview
- Data Transfer (MEWNT-W / MEWNET-W2)
- Remote I/O Control (MEWNET-F)
- Restrictions on Combinations of Units
- Restrictions on Installation Position
- Restrictions on Communication
- Names and Functions of Parts
- Switch Settings
- Operation Monitor LEDs
- Wiring
- Applicable Cables and Solderless Terminals
- Terminals
- MEWNET-W
- Overview
- Setting the Switches of the Unit
- Configuration
- No. of Occupied I/O Points of MEWNET-W
- W Link Unit Setting Procedure
- W Link Unit Setting Dialog Box
- Configuration Using User Programs
- PLC Link
- Holding Start Number Setting
- Data Transfer
- Data Transfer from Destination Unit to Own Unit
- Precautions When Using Data Transfer Function
- MEWNET-W2
- No. of Occupied I/O Points of MEWNET-W2
- W2 Link Unit Setting Procedure
- W2 Link Unit Setting dialog box
- PLC Link Operation State Flag
- Link Error Information
- Settings of the Unit
- Number of Occupied I/O Points for the Unit
- F Link Unit Setting Procedure
- F Link Unit Setting Dialog Box
- Allocation of Remote I/O Map
- Registration by Configuration
- Online Mount Allocation
- Starting MEWNET-F System
- Setting and Operation of Slave Connection Wait Time
- Checking Before Operation (Before Switching to RUN Mode)
- Behavior During Operation
- Other Functions
- Remote Programming
- Operation of Tool Software
- Computer Link
- Specifications and Restrictions
- Hierarchy Link
- Relevant Information
- Format of [0C] Command Response
- Troubleshooting
- Self-diagnostic Function
- Operation Monitor LEDs of FP7 MW Unit
- Confirmation by System Relays / System Data Registers
- Confirmation by System Data Registers
- Monitor and Operation by User Programs
- Clearing Errors by ERR Instruction
- What to Do If an Error Occurs
- Instruction References
- Communication Instructions
- RECV instruction (When using FP7 MW Unit)
- PMGET Instruction (For MEWNET-W)
- PMGET Instruction (For MEWNET-W2)
- PMGET Instruction (For MEWNET-F)
- PMSET/pPMSET Instruction (For MEWNET-W)
- PMSET/pPMSET instruction (For MEWNET-W2)
- Special Instructions
- Specifications
- List of System Relays (SR)
- List of System Data Registers (SD)
- Appendix
- Compatibility with Conventional Model FP2SH
- Data Transfer Function (W Mode, W2 Mode)
- Command Relay Function (W Mode, W2 Mode)
- Remote I/O Function (F Mode)

FP7 Series
Table of contents
- Table Of Contents
- Table Of Contents
- Table Of Contents
- Table Of Contents
- Overview
- System Configuration
- Restrictions on Combinations of Units
- Restrictions on Communication Functions to be Used
- Selection of Power Supply and Restrictions on Combination
- Power Supply for External Circuit
- Programming Tools
- Names and Functions of Parts
- CPU Unit
- Power Supply Unit
- I/O Number Allocation
- Basics of I/O Allocation
- Occupied I/O Points for Each Unit
- Optional Allocation Using FPWIN GR7
- Optional Settings in the "Unit Selection" Dialog Box
- Mount Allocation Using FPWIN GR7
- Changing the Starting Word Number
- Automatic Allocation
- I/O Map Registration
- Installation and Wiring
- Installation
- Attaching Units
- DIN Rail Attachment
- Wiring the Power Supply
- Wiring for Power Supply Units
- Wiring for the Power Supply Part of the CPU Unit
- Grounding
- Safety Measures
- Alarm Output
- Operation
- Before Powering On
- Procedures before Starting Operation
- RAM/ROM Operation
- Operations following Powering On
- Data Hold During Power Failure
- Backing Up the Project
- Transmission from the Backup Memory ROM2 to the Execution Memory RAM/ROM1
- SD Memory Card Operation
- How to Insert an SD Memory Card
- Saving an Execution File for SD Memory Card Operation
- Provisional Operation by an SD Memory Card
- Transmission from an SD Memory Card to the Execution Memory
- Precautions Concerning SD Memory Card Operation
- Troubleshooting
- Self-Diagnosis Function
- What to Do If an Error Occurs
- PROG Mode Does Not Change to RUN
- POWER LED Does Not Turn ON on the Power Supply Unit
- If Expected Output Is Not Available
- Maintenance and Inspection
- Handling of Backup Battery
- Replacement of Backup Battery
- Lifetime and Replacement Interval of Backup Battery
- Inspection
- Specifications
- CPU Unit Specifications
- Performance Specifications
- CPU Unit Communication Specifications
- Operation Memory Area
- List of System Relays
- List of System Data Registers
- Error Codes Table
- Power Supply Unit Specifications
- Dimensions
- Connector Type Unit
- Serial Communication Unit
- End Unit

FP7 Series
Table of contents
- Table Of Contents
- Table Of Contents
- Table Of Contents
- Table Of Contents
- Table Of Contents
- Table Of Contents
- Table Of Contents
- Table Of Contents
- Functions of Unit and Restrictions on Combinations
- Functions of Positioning Unit
- Unit Type
- Restrictions on Combinations of Units
- Names and Functions of Parts
- Operating Status LEDs
- Wiring
- Connection over Wire-pressed Terminal Cable
- Assembly of Connector for Wire-pressed Terminal Cable
- I/O Specifications and Terminal Wiring
- Supply of Power to Drive Internal Circuit
- Connecting Pulse Instruction Signal Input
- Connecting Deviation Counter Clear Output Signal
- Connecting Servo On Output Signal
- Connecting Home Input/Near Home Input Signal
- Connecting Near Home Input Signal
- Connecting Pulse Input
- Wiring Cautions
- Power On/Off and Check Items
- Safety Circuit Design
- Before Turning On the Power
- Procedure for Turning On the Power
- Procedure for Turning Off the Power
- Check with Power Turned On
- Check on External Safety Circuit
- Operation Checks on Near Home Switch and Home Switch
- Checking Rotating and Moving Directions and Moving Distance
- Unit Allocation and Parameter Settings
- Unit Allocation
- Check on I/O Allocation Information
- Axis Allocation for Use
- Parameter Settings
- Parameter Setting Items
- Synchronous Parameter/Cam Pattern Settings
- Cam Pattern Settings
- Creating Positioning Data Table
- Table No. Positioning Start
- Operation Patterns and Tables
- Saving Parameters
- Transfer to Unit and Commissioning
- Check on Setting Contents
- Transfer of Parameters
- Monitoring on Configurator PM7
- Tool Operation
- JOG Operation with Tool Operation Function
- Tool Operation - Home Return
- Tool Operation - Positioning
- Tool Operation - Teaching
- Automatic Operation (Positioning Control)
- Basic Operation
- Setting and Operation of E-Point Control
- Setting and Operation of P-Point Control
- Setting and Operation of J-point Control
- Sample Program (E-Point, P-Point, and C-Point Control)
- Programming Precautions
- Interpolation Control
- Setting and Operation of 2-Axis Linear Interpolation
- Setting and Operation of 2-Axis Circular Interpolation
- Setting and Operation of 3-Axis Linear Interpolation
- Setting and Operation of Three-Axis Linear Interpolation
- Sample Program (Interpolation Control)
- Setting and Operation of Positioning Repeat Function
- Automatic Operation (Synchronous Control)
- Synchronous Control
- Settings for Master and Slave Axes
- Selection of Slave Axes and Settings
- Enabling/Disabling Synchronous Control
- Electronic Gear Function
- Types and Contents of Setting Parameters
- Gear Ratio Changes while in Operation
- Electronic Clutch Function
- Trigger Types for Electronic Clutch
- Engagement Methods of Electronic Clutch
- Electronic Cam Function
- Cam Pattern Setting Method
- Manual Operation (JOG Operation)
- Setting and Operation of JOG Operation
- Changing the Speed During JOG Operation
- Manual Operation (Home Return)
- Pattern of Home Return
- Setting and Operation of Home Return
- Manual Operation (Pulser Operation)
- Setting and Operation of Pulser Operation
- Stop functions
- Settings and Operations of Stop Functions
- Settings and Operations of Pause Functions
- Supplementary Functions
- Dwell Time
- Software Limit
- Auxiliary Output Code and Auxiliary Output Contact
- Current Value Update
- Coordinate Origin
- Pulse Input
- Monitoring Pulse Input Values
- Pulser Input Function
- High-speed Counter Function
- Startup speed
- Programming Cautions
- Types of Positioning Data Setting Areas
- Errors and Warnings
- About Errors and Warnings
- Check and Clearing with User Program
- Error and Warning Logs
- Changes in Recovery from Errors
- Error Code Table
- Axis operation error (from 3000H)
- Set Value Error (from 4000H)
- List of Warning Codes
- Troubleshooting
- What to Do If an Error Occurs
- Reversed Rotation or Movement Direction
- Specifications
- Performance Specifications
- I/O Number Allocation
- Entire Configuration of Memory Unit Area
- Details of Common Area in Unit Memory
- Setting Parameter Control Area
- Current Value Update Data Area
- Positioning Control Starting Table Number Setting Area
- Positioning Control Area
- Error Annunciation & Clear Area
- Warning Annunciation & Clear Area
- Pulse Count Control Area
- Synchronous Control Monitor Area
- System Operation Setting Area
- Details of Each Axis Information Area in Unit Memory
- Each Axis Information & Monitor Area
- Details of Each Axis Setting Area in Unit Memory
- Parameter Setting Area
- Positioning Data Setting Areas
- Unit Memory Synchronous Control Setting Area
- Detailed Information on Synchronous Control Setting Area
- Dimensions
- Sample program
- Basic Configuration and Contact Allocations of Sample Programs
- When Setting Positioning Data in Extended Area by Programming
- When Setting Positioning Data in Standard Area by Programming

FP7 Series
Table of contents
- Table Of Contents
- Table Of Contents
- Table Of Contents
- Unit Functions and Restrictions
- Unit Functions and Operation
- Basic Operation of Analog Output Processing
- Restrictions on Units Combination
- Names and Functions of Parts
- Analog Output Unit
- Wiring
- Wiring of Terminal Block
- Analog Output Connections
- Current Output (0 to +20 and +4 to +20 mA)
- Unit Settings and Data Writing
- Confirming the I/O Number Allocations and First Word Number
- Confirming the I/O Number Allocations
- Configuration Settings
- Unit Setting and Conversion Processing Time
- Writing Analog Output Data
- Timing Chart of Output Processing
- Conversion Characteristics of Analog Output
- Voltage Range
- Voltage Output Range: 0 to +10 V (0.32 mV, 1/31,250)
- Voltage Output Range: +1 to +5 V (0.16 mV, 1/25,000)
- Current Range
- Option Settings for Analog Output
- Offset/Gain Processing Settings
- Scale Conversion Settings
- Settings for Upper and Lower Output Clipping
- Analog Output Hold while in PROG. Mode
- Configuration by Programming
- What to Do If an Error Occurs
- Specifications
- List of I/O Allocations
- List of Unit Memory
- List of Unit Memory Specifications in Detail
- Dimensions

FP7 Series
Table of contents
- Table Of Contents
- Table Of Contents
- Table Of Contents
- Table Of Contents
- Table Of Contents
- Introduction of EtherNet/IP Function
- Description of EtherNet/IP Communication Function
- What is EtherNet/IP?
- Cyclic Communication Function
- Definitions of Terms
- Examples of Network Configuration Using Cyclic Communication Function
- Connecting One Adapter Device or Multiple Adapter Devices to One FP7 CPU
- Overview of System Configuration Method
- Ethernet and EtherNet/IP Specifications of FP7
- Number of Connections for Each Communication
- Performance and Functions of FP7
- EtherNet/IP Setting Method
- Setting Method of Cyclic Communication
- How to Use EtherNet/IP Setting Tool
- Setting Example of One Scanner Device and Multiple Adapter Devices
- Setting Example of Multiple Scanner Devices and Multiple Adapter Devices
- Method of PLC Link
- EtherNet/IP Setting Tool
- Selection for Using EtherNet/IP Function
- How to Change the Built-in ET-LAN Setting Dialog Box
- Restrictions and Precautions on Setting EtherNet/IP Function
- How to Display the EtherNet/IP Setting Screen
- Starting Method from I/O Map Setting Screen
- How to Operate EtherNet/IP Setting Tool
- EtherNet/IP Setting Procedure
- Registering EDS Files in Device List
- How to Use I/O Map and Scan List
- Registering Adapter Devices
- How to Use "Device Setting" Tab
- How to Use "Connection Setting" Tab
- Device Allocation
- Adding I/O Map Registered Information
- Setting I/O Map Registered Information
- How to Use "Calculate Load Factor" Tab
- How to Use Device List
- How to Use I/O Map and Scan List Screen
- Editing I/O Map
- Device Property Setting
- How to Use "Save Setting" and "Read Setting"
- Migration of Device Database
- Import of Device Database
- When You Want to Restore the Registration Information Before Import
- Control Data
- Types of Control Data
- Cyclic Communication State Tables of EtherNet/IP
- Startup Operation of Cyclic Communication
- Abnormality Judgement and Operation
- High-level Instructions
- High-level Instructions Used for EtherNet/IP Control
- EtherNet/IP Node Status Acquisition Instruction (EIPNDST)
- Cyclic Communication Start Request (EIPSTART)
- Cyclic Communication Stop Request (EIPSTART)
- EtherNet/IP Input Refresh (EIP_IN)
- EtherNet/IP Output Refresh (EIP_OT)
- Data Refresh of Cyclic Communication
- What is Data Refresh?
- Data Refresh Method
- Delay Time of Transmission Data
- Delay Time of Reception Data
- Cyclic Communication Load Factor
- Calculation Method of Load Factor
- PLC Link and Ethernet Switch
- Other Ethernet Communications
- Performance of Other Ethernet Communications at the Time of Cyclic Communication
- Communication Status Monitoring with System Web
- Overview of FP7 System Web
- Starting System Web Screen
- Overview of EtherNet/IP Monitor
- CPU Status Indication > EtherNet/IP Monitor
- LED Display
- Lighting State of LED for EtherNet/IP Setting
- Lighting Patterns When PLC is Operating
- List of Cyclic Communication Errors
- Cyclic Communication: List of Abnormal Statuses

FP7 Series
Table of contents
- Table Of Contents
- Table Of Contents
- Table Of Contents
- Table Of Contents
- Table Of Contents
- Add-ons Specifications
- Ethernet Add-ons
- Using Add-ons
- IP Address Setting Specifications
- Recommended Connection Settings
- I/O Allocation
- I/O Relays of Extended Connections
- Confiming and Setting I/O Map
- Extension of the Number of Connections
- Overview of Extension of the Number of Connections
- How to Use Add-on for the Number of Connections
- Instructions Used in Master Communication
- Overview of Routing Setting
- How to Use Routing Setting
- FTP Client Function
- Overview of FTP Client Function
- FTP Client Function Specifications
- Details of FTP Client Function
- Logging/Trace Transfer Settings
- Overwrite Method and Rename Method
- How to Use File Transfer
- FTP File Transfer Settings (Sending and Overwriting File)
- FTP File Transfer Settings (Sending and Renaming File)
- FTP File Transfer Settings (Getting File)
- FTP File Transfer Settings (Sending and Overwriting Device)
- FTP File Transfer Settings (Sending and Renaming Device)
- FTP File Transfer Settings (Getting Device)
- Setting with Instructions
- Destination Server Setting (FTPcSV)
- Transfer Settings (FTPcSET)
- Executing File Transfer with Instructions
- Transfer Control (FTPcCTL)
- Information Acquisition of Ethernet Unit (ETSTAT)
- How to Use Logging/Trace Transfer
- Logging/Trace Transfer Settings (Send Rename)
- Settings with Instructions
- Confirming the Execution of Transfer with Instruction
- Precautions When Using FTP Client
- Number of Transferable Data and Processing Time
- HTTP Client Function
- Overview of HTTP Client Function
- Details of HTTP Client Function
- How to Use Transfer Settings
- HTTP Transfer Settings - Send (Upload)
- HTTP Transfer Settings - Get (Download)
- Transfer Settings (HTTPcSET)
- Executing Transfer with Instructions
- Transfer Control (HTTPcCTL)
- Status Acquisition of Ethernet Unit (ETSTAT)
- Precautions When Using HTTP Client
- Mail Transmission Function
- Overview of Mail Transmission Function
- Details of Mail Transmission Function
- How to Use Event Mail Transmission
- Destination Server Setting (SMTPcSV)
- Destination Group Setting (SMTPcADD)
- Mail Transmission Settings (SMTPcSET)
- Set Mail Text (SMTPcBDY)
- Read Mail Text (SMTPcBRD)
- Create Text (PRINT)
- Sending Mails with Instructions
- Mail Send Control (SMTPcCTL)
- How to Use Logging/Trace Mail Transmission
- character constant
- Confirming the Execution of Transmission with Instruction
- Precautions When Using Mail Transmission Function
- Instruction References
- List of Instructions Added to CPU Ver.3
- IP Address and Connection Setting Instructions
- CONSET
- OPEN
- CLOSE
- Communication Instruction
- PING Request Instruction (PINGREQ)
- Special Instruction
- Comparison Instruction
- Common Items
- List of Common Items
- MC Protocol Communication Function
- Overview of MC Protocol Communication Function
- Communication Specifications of MC Protocol
- How to Use MC Protocol Communication
- Communication Format
- Command and Subcommand
- Format of Request Data Part and Response Data Part
- Device Codes and Device Numbers
- Bulk Read and Bulk Write
- Example of Bulk Write
- Exit Codes When Communication Error Occurs
- MC Protocol Master Communication (RECV)
- RECV Instruction (MC Protocol)
- MC Protocol Master Communication (SEND)
- SEND Instruction (MC Protocol)

FP7 Series
Table of contents
- Table Of Contents
- Table Of Contents
- Table Of Contents
- Unit Functions and Restrictions
- Unit Functions and How They Work
- Unit Type and Product Number
- Restrictions on Combinations of Units
- Names and Functions of Parts
- Thermocouple Multi-analog Input Unit and RTD Input Unit
- Wiring
- Wiring of Terminal Block
- Connection of Thermocouple Multi-analog Input Unit
- For Voltage Input
- For Current Input
- Connection of RTD Input Unit
- Unit Settings and Data Reading
- Confirming the I/O Number Allocations and Starting Word Number
- Confirming Allocation of I/O Numbers
- Configuration Settings
- Unit Setting and Conversion Processing Time
- Reading Analog Input Data
- Data Acquisition Timing
- Conversion Characteristics of Analog Input
- Input Conversion Characteristics (AFP7TC8)
- Voltage Input Range
- Current Input Range
- Input Conversion Characteristics (AFP7RTD8)
- Optional settings
- Average Processing Settings
- Time Average
- Moving Average
- Offset/Gain Processing
- Scale Conversion (AFP7TC8 Voltage/Current Range Only)
- Comparison for Upper and Lower Limits
- Holding Maximum and Minimum Values
- Disconnection Detection (AFP7TC8)
- Disconnection Detection (AFP7RTD8)
- Configuration by Programming
- What to Do If an Error Occurs
- What to Do If an Error Occurs (Analog Input)
- Specifications
- Specifications of Thermocouple Multi-analog Input Unit (AFP7TC8)
- Specifications of RTD Unit (AFP7RTD8)
- I/O Allocation
- List of Unit Memories
- List of Detailed Specifications of Unit Memories
- Dimensions

FP7 Series
Table of contents
- Table Of Contents
- MEWTOCOL-COM
- Basic Instructions
- List of Instructions
- TM16 (16-bit Timer)
- CT16- (16-bit Counter)
- Precautions for Programming
- High-level Instructions
- BKEXT (16-bit Data Sign-extended Block Move)
- BKMV16 (Block Move (32-bit Data to 16-bit Data))
- DIVFP2 (Division (FP2 Compatible))
- BTS (16-bit Data Specified Bit Set)
- BTR (16-bit Data Specified Bit Reset)
- FP2/FP2SH Program Conversion Function
- List of Conversion Instructions to FP7
- Conversion of Special Relays
- Conversion of Special Data Registers
- List of Commands
- Multi Connection Server Function
- Precautions When Connecting Multi Connection Servers
- How to Set Connections
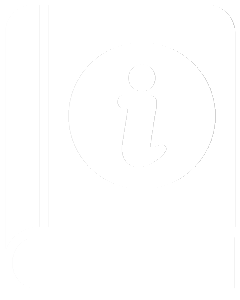
manualsdatabase
Your AI-powered manual search engine