YASKAWA motoman NX100 manuals

motoman NX100
Table of contents
- instruction manual
- Table Of Contents
- Table Of Contents
- Table Of Contents
- General
- Safety
- Handling ESD sensitive devices
- Terms
- Installation
- NX100 Installation
- Software configuration
- Manual I/O allocation (FD 134)
- Fieldbus input data map
- Fieldbus status byte
- General installation in IP-based networks
- Anybus IPconfig
- The module is not shown
- Reg.No. ME00107EN-02 Page
- Profibus DPV1 Slave AB3601
- Connectors 9-pin D-sub
- PROFIBUS network setup
- Profibus DPV1 Master AB3602
- Configuration online
- DeviceNet Adapter Slave AB3603
- Connectors
- DeviceNet Scanner Master AB3604
- AnyBus NetTool for DeviceNet
- AS-Interface Master AB3605
- Principle of Input/Outputs in ASI
- Menu Tree Overwiev
- Change settings
- EtherNet/IP Adapter/Modbus TCP Slave AB3606
- Status LEDs
- Network setup
- EtherNet/IP Scanner Master AB3607
- PROFINET-IO Slave AB3609
- FL-Net AB3610
- FIPIO Slave AB3611
- Interbus-S Slave AB3615
- Setup
- CanOpen Slave AB3616
- EtherCAT slave AB3617
- revision history

motoman NX100
Table of contents
- Table Of Contents
- Table Of Contents
- INTRODUCTION
- system requirements
- Connection types
- Configuration of robot controller
- file menu
- view menu
- tools menu
- Mode menu
- Menü Hilfe
- WORKING WITH MOTOADMIN
- Exit application
- Refresh status
- Change operation mode
- Edit Jobs
- Job Liste laden
- Access variables
- Watch I/O Signals
- Saving, Loading and Deleting files
- Jobs
- system data
- One-Button Backup
- Deleting data
- system information
- Read Alarm History
- KNOWN LIMITATIONS

motoman NX100
Table of contents
- Table Of Contents
- Table Of Contents
- Table Of Contents
- Table Of Contents
- Introduction
- Seam Finding
- Macro Jobs
- Features
- System Requirements
- Setup and Operation
- Setting the Q1 Focal Length:
- AccuFast II
- Using the Zero Shift Function (If Temperature Variance is a Concern)
- Job Setup
- AutoTeach
- TCH Macro, One Touch (1TCH) Routine
- Limitations
- AutoTeach Mode
- Macro Job Setup
- Interface
- Programming Instructions
- TCH Macro, Two Touch (2TCH) Routine
- EDGE: Edge Finding Routine
- Programming
- AutoTeach 1 (Robot Position 2)
- AutoTeach 2 (Robot Position 3)
- R1 CIRCLE: Circle Touch Routine
- Setup Macro Instruction and Detect Robot Position 1
- Detect Robot Position 2
- Cylinder to Plate
- Programming Suggestions
- AccuFast II Orientation
- Perpendicular Search Paths
- Pattern Type and AutoTeach Descriptions
- AutoTeach 0
- AutoTeach 2
- Pattern Type 2
- Pattern Type 4
- AutoTeach 2, Step Offset 0
- Target for TCP Update for AccuFast or AccuFast II
- Breakdown of Procedure
- Detailed Usage
- Adjust Settings of ACCUFAST - TCP - UPDATER robot job
- Set and Program the AccuFast - TCP - UPDATER Robot Job
- Run the Robot Job in Train Mode
- Appendix B
- Run the Robot Job in Calc Mode
- TCP Detection Mode (Optional)
- Appendix A
- B.1 Value B Variables
- Appendix C
- Appendix D

motoman NX100
Table of contents
- Table Of Contents
- Table Of Contents
- Table Of Contents
- Table Of Contents
- Table Of Contents
- Table Of Contents
- Table Of Contents
- Coordinated Control
- Independent Control
- Outline
- Function Keys
- General Application
- Example of Job Teaching
- System Setup
- Calibration between Manipulator and Station
- Teaching Positions for Calibration
- Calibration
- JOB CONTENT Window
- Synchronized/Single
- Single
- Selecting Axis to be Handled
- Registering Job
- Registering Move Instruction (S)MOV+MOVJ
- Operating Slave Side (Manipulator)
- Specific Keys
- Opening and Closing Handling Tool
- Example of Teaching Job
- Calibration between Manipulators
- Teaching Position for Calibration
- Job Content Display
- Registering Move Instruction (S)MOV+MOV
- Operating Slave Side (Torch)
- Registering Handling Instructions
- Other Convenient Features
- Operation Method
- Manipulator Movement
- Wrist axes
- Job Configuration
- Leader and Follower
- Synchronizing with TSYNC
- Job Example
- Job Synchronized Mode for Subtask 1 and 2
- Switching Tasks
- Creating a Job in a Subtask - Method 1 and 2
- Method 1: Copy One Subtask Job and Create Another Job
- Teaching and Mirror Shift
- Jobs Not to be Converted
- Correcting Positional Dislocation
- Setting the Shift Value
- Executing Conversion
- Method 2: Perform Teaching for Each Manipulator
- Teaching using Master Task
- Teaching using SUPERVISORY Window
- Job in Master Task
- Confirming Operation
- Precautions for Confirming Operation
- in the TEACHING CONDITION Window
- Playback
- Automatic Correction of Shift Value
- Job Synchronized Mode for Subtask 1, 2, and 3
- Changing Tasks
- Method 1: Copy One Subtask Job and Create Other Two Jobs
- TEACHING CONDITION Window
- Group Combination
- Individual Interpolation
- Startup Method
- Starting Various Jobs
- Switching Task Window
- Registering Instructions
- TSYNC Instruction
- Concurrent Job
- Job Examples
- Synchronous Operation
- PSTART Instruction
- Switching on TEACHING CONDITION Window
- Registering Master Job
- Cancelling Registration
- Calling Master Job
- When the Master Job in a Subtask 1/2/3 is Called
- Registration of Root (startup) Job
- Registrering
- Precautions
- Connection of Signals for Servo Power Supply Individual Control
- Confirming Connection
- Application Examples
- System Output Signals
- Specification
- Coordinated Motion Instructions
- Independent Control Instructions
- CONVSFT Instruction
- Master Robot (Station) Position
- Example of Conversion
- Alarm
- Supplementary Note

motoman NX100
Table of contents
- Table Of Contents
- system requirements
- Connecting USB type key
- Software
- Installation of the NX100 RCS Module
- Installation Directory
- IGRIP D5-RRS/RCS-Module Connection Operation
- IGRIP-RRS Connection Operation
- IGRIP-RRS Disconnection Operation
- IGRIP-RRS Connection Using Parameters of Actual Manipulator
- When the MOTOMAN Model Required for Manipulator Selection is not Displayed
- IGRIP V5-RRS/RCS-Module Connection Operation
- Start-up of the RCS Server Program
- IGRIP V5-RRS Disconnection Operation
- APPENDIX

motoman NX100
Table of contents
- Table Of Contents
- Table Of Contents
- Table Of Contents
- Table Of Contents
- Table Of Contents
- Table Of Contents
- Table Of Contents
- Table Of Contents
- Table Of Contents
- Table Of Contents
- Table Of Contents
- Table Of Contents
- Table Of Contents
- Table Of Contents
- NX100 Overview
- Programming Pendant
- Key Description
- Programming Pendant Keys
- Programming Pendant Display
- General-purpose Display Area
- Main Menu Area
- Human Interface Display Area
- Screen
- Operation
- Alphanumeric Input
- Modes
- About the Security Mode
- Switching Security Modes
- Control Groups and Coordinate Systems
- Types of Coordinate Systems
- General Operations
- Servo ON
- Coordinate Systems and Axis Operation
- Cartesian Coordinates
- Cylindrical Coordinates
- Tool Coordinates
- Selecting the Tool
- User Coordinates
- Selecting User Coordinates
- Examples of User Coordinate Utilization
- Control Point Operation
- Control Point Change
- Preparation for Teaching
- Registering a Job
- Registering Comments
- Teaching Operation
- Interpolation Type and Play Speed
- Linear Interpolation
- Circular Interpolation
- Spline Interpolation
- Teaching Steps
- Registering Reference Point Instructions
- Registering Timer Instructions
- Overlapping the First and Last Steps
- Checking Steps
- Selecting Manual Speed
- Moving to Reference Point
- Modifying Steps
- Displaying the JOB CONTENT Window for Editing
- Inserting Move Instructions
- Deleting Move Instructions
- Modifying Move Instructions
- Undo Operation
- Modifying Reference Point Instructions
- Modifying Timer Instructions
- Modifying Jobs
- JOB CONTENT Window
- COMMAND POSITION Window
- JOB CAPACITY Window
- Editing Instructions
- Inserting Instructions
- Deleting Instructions
- Modifying Additional Numeric Data
- Modifying Additional Items
- Inserting Additional Items
- Deleting Additional Items
- Editing Jobs
- Selecting the Range
- Copying
- Pasting
- Reverse Pasting
- Test Operations
- Other Job-editing Functions
- Modification by TRT (Traverse Time)
- Editing Interpolation Type
- Editing Condition Files
- User Variables
- and Real Type Variables
- Setting Character Type Variables
- Registering Variable Name
- Displaying Position Variables
- Setting Position Variables
- Setting Position Variables Using the Numeric Keys
- Setting Position Variables Using the Axis Keys
- Deleting Data Set of Position Variables
- Checking Positions by Position Variables
- Manipulator Types
- Editing Local Variables
- Setting the Number of Local Variables
- Searching
- Line Search
- Label Search
- Instruction Search
- Tag Search
- Preparation for Playback
- Registering the Master Job
- Calling the Master Job
- The PLAYBACK Window
- Display of Cycle Time
- Playback
- Low Speed Operation
- Dry-run Speed Operations
- Check Mode Operation
- Stop and Restart
- Emergency Stop
- Restart After Emergency Stop
- Stop by Alarm
- Others
- Modifying Play Speed
- Setting Speed Overrides
- Playback with Reserved Start
- Enabling Reserved Start
- Registering Reserved Start I/O Signal
- Registering Jobs to Stations
- Deleting Registered Jobs from Stations
- Playback from Reserved Start
- Checking Job Reservation Status
- Resetting Job Reservation
- Hold Operation
- Hold at the Station
- Displaying Job Stack
- Copying Jobs
- Copying Jobs on the JOB LIST Window
- Deleting Jobs
- Deleting Jobs on the JOB LIST Window
- Modifying Job Names
- Modifying Job Names on the JOB LIST Window
- Editing Comments
- Setting Edit Lock on Individual Job Units
- Enabling the Modification of Position Data Only
- One-touch Operation "Direct Open"
- Parallel Shift Function
- Setting the Shift Value
- Registering Shift Instructions
- SFTON Instruction
- SFTOF Instruction
- Continuation of the Parallel Shift Function
- Examples of Use
- Example of Use of MSHIFT Instruction
- Parallel Shift Job Conversion Function
- Coordinate Systems for Conversion
- Executing the Parallel Shift Job Conversion
- Parallel Shift Job Conversion Operation
- Specifying the Shift Value by Position Variables
- Jobs Targeted for Conversion
- Conversion of Coordinated Jobs
- Operation Procedure
- PAM Function
- Operating Methods
- Executing the Adjustment
- Editing Data
- Mirror Shift Function
- Object Job
- Position Variables
- Notes on the Mirror Shift Function
- Operation Procedures
- Explanation of the Mirror Shift Window
- Memory Devices
- Compact Flash (CF Cards)
- Notes on handling Compact Flash
- Inserting a Compact Flash
- Handling Data
- Collective Backup
- File Existence
- Operation Flow
- Operating a Folder
- Saving Data
- Loading Data
- Verifying Data
- Deleting Data
- Job Selection Mode
- Parameter Configuration
- Motion Speed Setting Parameters
- S1CxG018 to S1CxG025: POSITION ANGLE SPEED
- S1CxG044: LOW-SPEED START
- S1CxG057: SEARCH MAX. SPEED
- PATH DEVIATION
- S2C326: DEVIATED POSITION
- POSITION CONTROL
- POSITION
- FUNCTION DURING PLAYBACK
- Mode Operation Setting Parameters
- S2C158: ADDITIONAL STEP POSITION
- OPERATION IN PLAY MODE
- S2C166: INSTRUCTION INPUT LEARNING FUNCTION
- STEP"
- S2C174: RESERVED START
- WHEN "IO" IS SELECTED FOR REMOTE MODE
- S2C211: REMOTE FIRST CYCLE MODE
- S2C297: SIGNAL NAME ALIAS FUNCTION
- S2C298: VARIABLE NAME ALIAS FUNCTION
- S2C299: I/O VARIABLE CUSTOMIZE FUNCTION
- S2C317 to S2C321: TIME RESET
- FUNCTION
- Parameters according to Interference Area
- S2C001: CUBE SOFT LIMIT CHECK
- CHECK
- S2C051 to S2C114: CUBE USING METHOD
- S2C188 to S2C193: ROBOT INTERFERENCE CHECK
- S3C024 to S3C031: S-AXIS INTERFERENCE AREA
- Parameters according to Status I/O
- S4C000 to S4C007: PARITY OF USER INPUT GROUPS
- GROUPS
- S4C016 to S4C023: DATA OF USER INPUT GROUPS
- S4C024 to S4C031: DATA OF USER OUTPUT GROUPS
- S4C032 to S4C039: USER OUTPUT GROUP TO BE INITIALIZED AT SWITCHING MODE
- CONTROL
- S2C195 to S2C206: STATION AXIS DISPLAYED UNIT
- MULTI-JOB (When Twin Synchronous Function Used)
- Parameters for Other Functions or Applications
- S2C332: RELATIVE JOB OPERATION METHOD
- Hardware Control Parameters
- S2C646 to S2C648: COOLING FAN ALARM
- RS038: BLOCK CHECK METHOD
- FC1 Protocol
- Application Parameters
- AxP011, AxP012: MANUAL WIRE OPERATION SPEED
- AxP005: STROKE CHANGE ANSWER TIME LIMIT
- Function Keys
- Outline of Operations and Painting Functions
- Settings for Panting System When Using a Spray Gun
- Teaching for Painting Operations
- Anticipation Output Function
- Notes on Anticipation Output Function
- Registering Work Instructions
- One-touch Operation
- Notes on the SPYON Instruction
- SPYOF
- Notes on the SPYOF Instruction
- PAINTSET
- CALL
- Registering the Job Registration Table
- Registering the CALL Instruction (JET)
- Painting Condition File
- Managing Painting Condition Files
- Editing Painting Condition Files
- Registering Painting Condition Files
- Painting System Setting File
- Calling Up Painting System Setting Files
- Editing Painting System Setting Files
- Painting System Characteristics Setting File
- Editing Painting System Characteristics Setting Files
- Instruction
- Notes on the ON/OFF Timing of the Work Start Instruction
- Work Instruction List
- Move Instructions
- I/O Instructions
- Control Instructions
- Shift Instructions
- Operating Instructions
- Error Message List
- System and General Operation
- Editing
- External Memory Equipment
- Concurrent I/O
- Maintenance Mode

motoman NX100
Table of contents
- Table Of Contents
- Table Of Contents
- Table Of Contents
- Table Of Contents
- Conveyor Synchronized Operation
- Hardware Specifications
- Connecting Conveyor Home-Position Signals
- Connection Example of One Conveyor
- Connector Connection
- Sensor Cable Connection
- Closing the Front Door
- Displaying Conveyor Condition File
- Editing "BROKEN LINE DETECT"
- Editing "BASE AXIS"
- Editing "CONVEYOR SPEED DOWN MODE"
- Setting Conveyor Positional Resolution
- Resolution
- SYSTART Instruction
- Format
- SYEND Instruction
- Registering SYEND Instruction
- SYMOV¨ Instruction
- Operation
- When Adding or Changing Step After Interruption of
- Notes on Operation
- Job Example
- Playback
- Accuracy
- Continuance of Parallel Shift Status
- Conveyor Monitoring Windows
- Virtual Encoder Mode
- Setting Up the Turntable Synchronized System
- Calibration between Manipulator and Turntable
- Teaching Calibration Position
- Operating Calibration
- Settings for Manual Conveyor Function

motoman NX100
Table of contents
- Table Of Contents
- Table Of Contents
- Contents Confirmation
- Order Number Confirmation
- Transporting Method
- Shipping Bolts and Brackets
- Installation of the Safeguarding
- Mounting Example
- Grounding
- Manipulator Cable Connection
- Basic Specifications
- Part Names and Working Axes
- Alterable Operating Range
- Components for Altering Operating Range
- Notes on the Mechanical Stopper Installation
- Grease Replenishment for Balancer Connection Part
- Notes for Maintenance
- parts list
- L-Axis
- URBT-Axis Link
- Wrist
- Balancer

motoman NX100
Table of contents
- Table Of Contents
- Table Of Contents
- Table Of Contents
- Table Of Contents
- Table Of Contents
- Table Of Contents
- Table Of Contents
- Table Of Contents
- Table Of Contents
- Table Of Contents
- Table Of Contents
- Table Of Contents
- Table Of Contents
- Table Of Contents
- Table Of Contents
- NX100 Overview
- Programming Pendant
- Key Description
- Programming Pendant Keys
- Programming Pendant Display
- General-purpose Display Area
- Main Menu Area
- Human Interface Display Area
- Screen
- Operation
- Alphanumeric Input
- Modes
- About the Security Mode
- Switching Security Modes
- Control Groups and Coordinate Systems
- Types of Coordinate Systems
- General Operations
- Servo ON
- Coordinate Systems and Axis Operation
- Cartesian Coordinates
- Cylindrical Coordinates
- Tool Coordinates
- Selecting the Tool
- User Coordinates
- Selecting User Coordinates
- Examples of User Coordinate Utilization
- Control Point Operation
- Control Point Change
- Preparation for Teaching
- Registering a Job
- Registering Comments
- Teaching Operation
- Interpolation Type and Play Speed
- Linear Interpolation
- Circular Interpolation
- Spline Interpolation
- Teaching Steps
- Registering Reference Point Instructions
- Registering Timer Instructions
- Overlapping the First and Last Steps
- Checking Steps
- Selecting Manual Speed
- Moving to Reference Point
- Modifying Steps
- Displaying the JOB CONTENT Window for Editing
- Inserting Move Instructions
- Deleting Move Instructions
- Modifying Move Instructions
- Undo Operation
- Modifying Reference Point Instructions
- Modifying Timer Instructions
- Modifying Jobs
- JOB CONTENT Window
- COMMAND POSITION Window
- JOB CAPACITY Window
- Editing Instructions
- Inserting Instructions
- Deleting Instructions
- Modifying Additional Numeric Data
- Modifying Additional Items
- Inserting Additional Items
- Deleting Additional Items
- Editing Jobs
- Selecting the Range
- Copying
- Pasting
- Reverse Pasting
- Test Operations
- Other Job-editing Functions
- Modification by TRT (Traverse Time)
- Editing Interpolation Type
- Editing Condition Files
- User Variables
- and Real Type Variables
- Setting Character Type Variables
- Registering Variable Name
- Displaying Position Variables
- Setting Position Variables
- Setting Position Variables Using the Numeric Keys
- Setting Position Variables Using the Axis Keys
- Deleting Data Set of Position Variables
- Checking Positions by Position Variables
- Manipulator Types
- Editing Local Variables
- Setting the Number of Local Variables
- Searching
- Line Search
- Label Search
- Instruction Search
- Tag Search
- Preparation for Playback
- Registering the Master Job
- Calling the Master Job
- The PLAYBACK Window
- Display of Cycle Time
- Playback
- Low Speed Operation
- Dry-run Speed Operations
- Check Mode Operation
- Stop and Restart
- Emergency Stop
- Restart After Emergency Stop
- Stop by Alarm
- Others
- Modifying Play Speed
- Setting Speed Overrides
- Modifying Play Speed
- Playback with Reserved Start
- Enabling Reserved Start
- Registering Reserved Start I/O Signal
- Registering Jobs to Stations
- Deleting Registered Jobs from Stations
- Playback from Reserved Start
- Checking Job Reservation Status
- Resetting Job Reservation
- Hold Operation
- Hold at the Station
- Displaying Job Stack
- Copying Jobs
- Copying Jobs on the JOB LIST Window
- Deleting Jobs
- Deleting Jobs on the JOB LIST Window
- Modifying Job Names
- Modifying Job Names on the JOB LIST Window
- Editing Comments
- Setting Edit Lock on Individual Job Units
- Enabling the Modification of Position Data Only
- One-touch Operation "Direct Open"
- Parallel Shift Function
- Setting the Shift Value
- Registering Shift Instructions
- SFTON Instruction
- SFTOF Instruction
- Continuation of the Parallel Shift Function
- Examples of Use
- Example of Use of MSHIFT Instruction
- Parallel Shift Job Conversion Function
- Coordinate Systems for Conversion
- Executing the Parallel Shift Job Conversion
- Parallel Shift Job Conversion Operation
- Specifying the Shift Value by Position Variables
- Jobs Targeted for Conversion
- Conversion of Coordinated Jobs
- Operation Procedure
- PAM Function
- Operating Methods
- Executing the Adjustment
- Editing Data
- Mirror Shift Function
- Object Job
- Position Variables
- Notes on the Mirror Shift Function
- Operation Procedures
- Explanation of the Mirror Shift Window
- Memory Devices
- Compact Flash (CF Cards)
- Notes on handling Compact Flash
- Inserting a Compact Flash
- Handling Data
- Collective Backup
- File Existence
- Operation Flow
- Operating a Folder
- Saving Data
- Loading Data
- Verifying Data
- Deleting Data
- Job Selection Mode
- Parameter Configuration
- Motion Speed Setting Parameters
- S1CxG018 to S1CxG025: POSITION ANGLE SPEED
- S1CxG044: LOW-SPEED START
- S1CxG057: SEARCH MAX. SPEED
- PATH DEVIATION
- S2C326: DEVIATED POSITION
- CONTROL
- POSITION
- FUNCTION DURING PLAYBACK
- Mode Operation Setting Parameters
- S2C158: ADDITIONAL STEP POSITION
- OPERATION IN PLAY MODE
- S2C166: INSTRUCTION INPUT LEARNING FUNCTION
- STEP"
- S2C174: RESERVED START
- WHEN "IO" IS SELECTED FOR REMOTE MODE
- S2C211: REMOTE FIRST CYCLE MODE
- S2C297: SIGNAL NAME ALIAS FUNCTION
- S2C298: VARIABLE NAME ALIAS FUNCTION
- S2C299: I/O VARIABLE CUSTOMIZE FUNCTION
- S2C317 to S2C321: TIME RESET
- FUNCTION
- Parameters according to Interference Area
- S2C001: CUBE SOFT LIMIT CHECK
- CHECK
- S2C051 to S2C114: CUBE USING METHOD
- S2C188 to S2C193: ROBOT INTERFERENCE CHECK
- S3C024 to S3C031: S-AXIS INTERFERENCE AREA
- Parameters according to Status I/O
- S4C000 to S4C007: PARITY OF USER INPUT GROUPS
- GROUPS
- S4C016 to S4C023: DATA OF USER INPUT GROUPS
- INITIALIZED AT SWITCHING MODE
- Synchronized Operation
- S2C195 to S2C206: STATION AXIS DISPLAYED UNIT
- MULTI-JOB (When Twin Synchronous Function Used)
- Parameters for Other Functions or Applications
- S2C332: RELATIVE JOB OPERATION METHOD
- Hardware Control Parameters
- S2C646 to S2C648: COOLING FAN ALARM
- RS033: TRANSMISSION SPEED
- FC1 Protocol
- Application Parameters
- AxP011, AxP012: MANUAL WIRE OPERATION SPEED
- AxP005: STROKE CHANGE ANSWER TIME LIMIT
- Function Keys
- General Descriptions of Instructions and Functions
- Functions Used During Teaching
- Function Outlines
- Welding Execution Function During Teach Mode
- Arc Retry Function
- Arc Restart Function
- Wire-stick Check Function
- Automatic Wire-stick Release Function
- Slope Up/Down Function
- Enhanced Welding Condition File Function
- Setting Welding Start Conditions
- ARCOF
- Setting Welding End Conditions
- ARCSET
- ARCCTS
- Registering the ARCCTS Instruction
- ARCCTE
- Registering the ARCCTE Instruction
- Welding Condition Files
- Selecting Welding Condition Files
- Arc Start Condition File
- Arc End Condition File
- Arc Auxiliary Condition File
- Arc Restart Function Setting
- Automatic Wire Anti-stick Function Setting
- Enhanced Arc Start Condition File
- Enhanced Arc End Condition File
- Editing Welding Condition File
- Editing the Arc Start Condition File
- Editing the Arc End Condition File
- Changing Welding Conditions During Playback
- Changing Welding Conditions
- Notes on Modification of Welding Conditions
- ARCON Instruction
- ARCCTS and ARCCTE Instructions
- Editing Condition Files During the Play Mode
- Arc Welding Management and Maintenance
- Editing the ARC WELD DIAGNOSIS Window
- Displaying Welding Alarm History
- Notes on Arc Welding
- Weaving Condition File
- WEAVING CONDITION Window
- Editing the Weaving Condition Files
- Editing the Condition Data
- Cases that Require the Registration of Reference Points
- Prohibiting Weaving
- or FWD Operation
- System Input Signal
- WVOF Instruction
- Power Source Condition File
- Power Supply is Used
- POWER SOURCE CONDITION Window
- Output
- Editing the Power Source Condition Files
- Reading a Power Source Condition File
- Editing a Power Source Condition File
- Current/Voltage Output
- Registering the Power Source Condition File Data
- Power Source Condition File Initial Value
- Contents of 24 Welder Condition Files
- Table of Work Instructions
- Move Instructions
- I/O Instructions
- Control Instructions
- Shift Instructions
- Operating Instructions
- Error Message List
- System and General Operation
- Editing
- External Memory Equipment
- Concurrent I/O
- Maintenance Mode

motoman NX100
Table of contents
- Table Of Contents
- Table Of Contents
- Circle
- How to Teach a Pattern
- Tool Position and Cutting Pattern
- Cutting Width Correction Function
- Example of Form Cutting Function
- Example of a Motion Path
- Motion Example 1
- Motion Example 2
- FORMAPR Instruction (Form Cutting Start Motion Instruction)
- Registering Instructions
- Registering in Variables
- FORMCUT (Form Cutting Motion Instruction)
- Settings
- Details of File Settings
- Specifying the ROTATION DIRECTION
- Displaying and Editing File

motoman NX100
Table of contents
- Table Of Contents
- Table Of Contents
- Table Of Contents
- For Your Safety
- Special Training
- Personnel Safety
- Motoman Safety
- Work Area Safety
- Operation Safety
- Notes for Moving and Transferring the MOTOMAN
- Notes on MOTOMAN Disposal
- Contents Confirmation
- Order Number Confirmation
- Handling Procedure
- Using a Forklift to Move the Controller
- Location
- Mounting the Controller
- Notes on Cable Junctions
- Power Supply
- Noise Filter Installation
- Primary Power Supply Switch Installation
- Connection Methods
- Connecting the Manipulator Cable
- Connecting the Programming Pendant
- Turning ON the Main Power Supply
- Initial Diagnosis
- Turning ON the Servo Power
- Procedures for Operation Mode Change
- During Teach Mode
- Turning OFF the Power Supply
- Specification List
- Function List
- Programming Pendant
- Equipment Configuration
- Cooling System of the Controller Interior
- Power Supply Contactor Unit
- Connection for Tool Shock Sensor (SHOCK)
- Connection for External Axis Overrun (EXOT)
- CPU Unit
- Units and Circuit Boards in the CPU Unit
- WAGO Connector
- Major Axes Control Circuit Board (SGDR-AXA01A)
- System I/O Signal Related to Start and Stop
- Connection of External Power Supply for I/O
- Robot System Input Terminal Block (MXT)
- External Emergency Stop
- Safety Plug
- Maintenance Input
- Full-speed Test
- External Servo ON
- External Enable Switch
- Direct-in 1 to 4 (Option)
- Contact Output of Emergency Stop Button
- SERVOPACK
- User I/O Signal Assignment
- Handling
- General Application
- Spot Welding
- JANCD-XEW01 Circuit Board

Related products
Motoman MLX200JUSP-NS100JAPMC-MC2100JAPMC-MC2100-EJUSP-NS300JEPMC-MP2300U1000 SeriesJUSP-NS300-EMP2000 SeriesJEPMC-MP2300-EYASKAWA categories
Controller
DC Drives
Servo Drives
Inverter
Touch Panel
Robotics
Control Unit
Industrial Equipment
Media Converter
Industrial Electrical
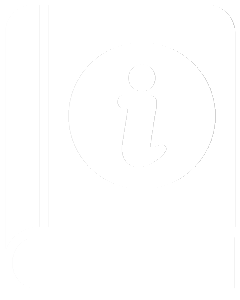
manualsdatabase
Your AI-powered manual search engine